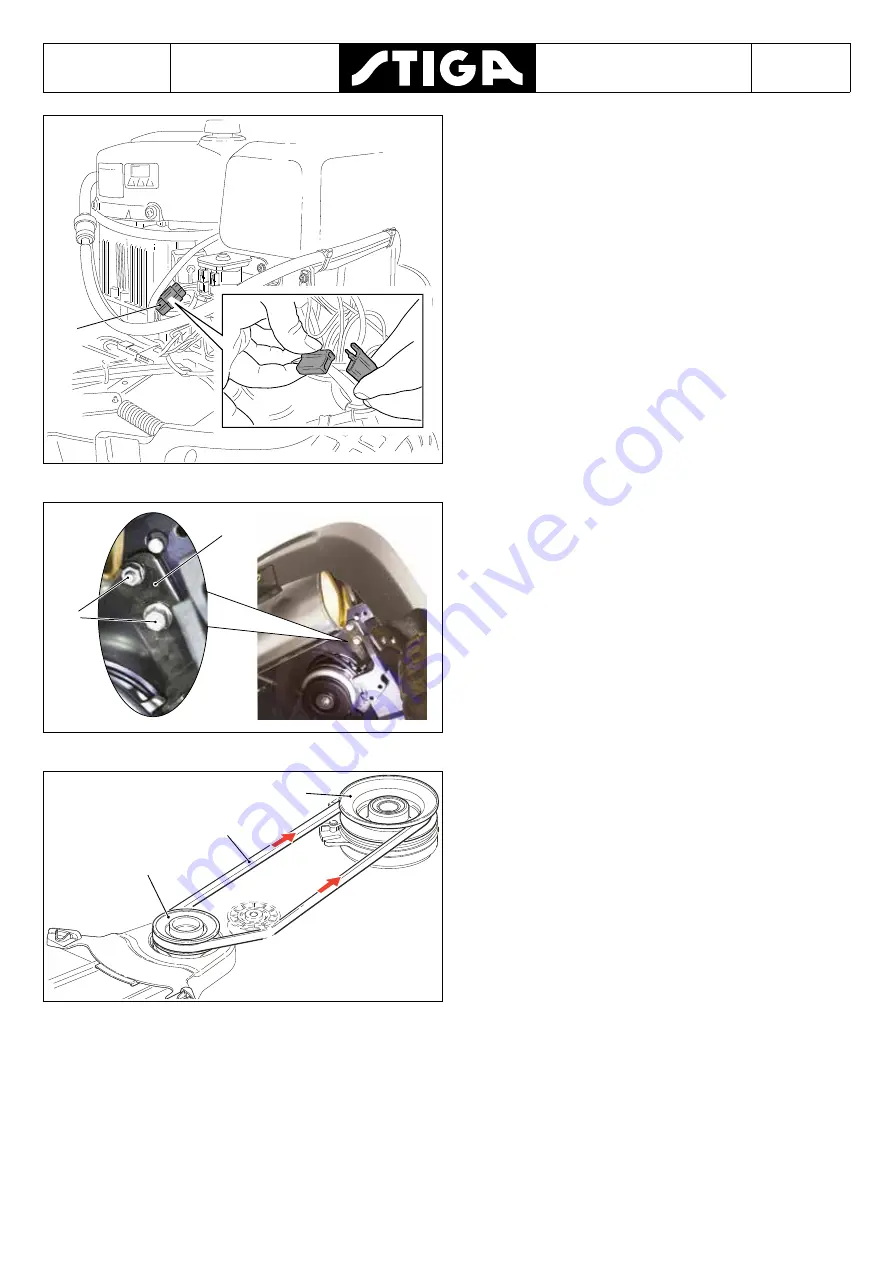
Edition
2016
Workshop Manual
PARK 120 - PARK 220
Chapter
Page
37
15
6. Cut the tie which holds the cable to the clutch.
7. Disconnect the connector (15) from the clutch
cable.
17
16
8. Remove the clutch stopper (16) by unscrewing
the two screws (17).
C
10
5
9. Remove the belt from the double pulley (5).
10. Remove the belt (C) from the pulley (10) on
the drive shaft and slip the belt out from the
rear.