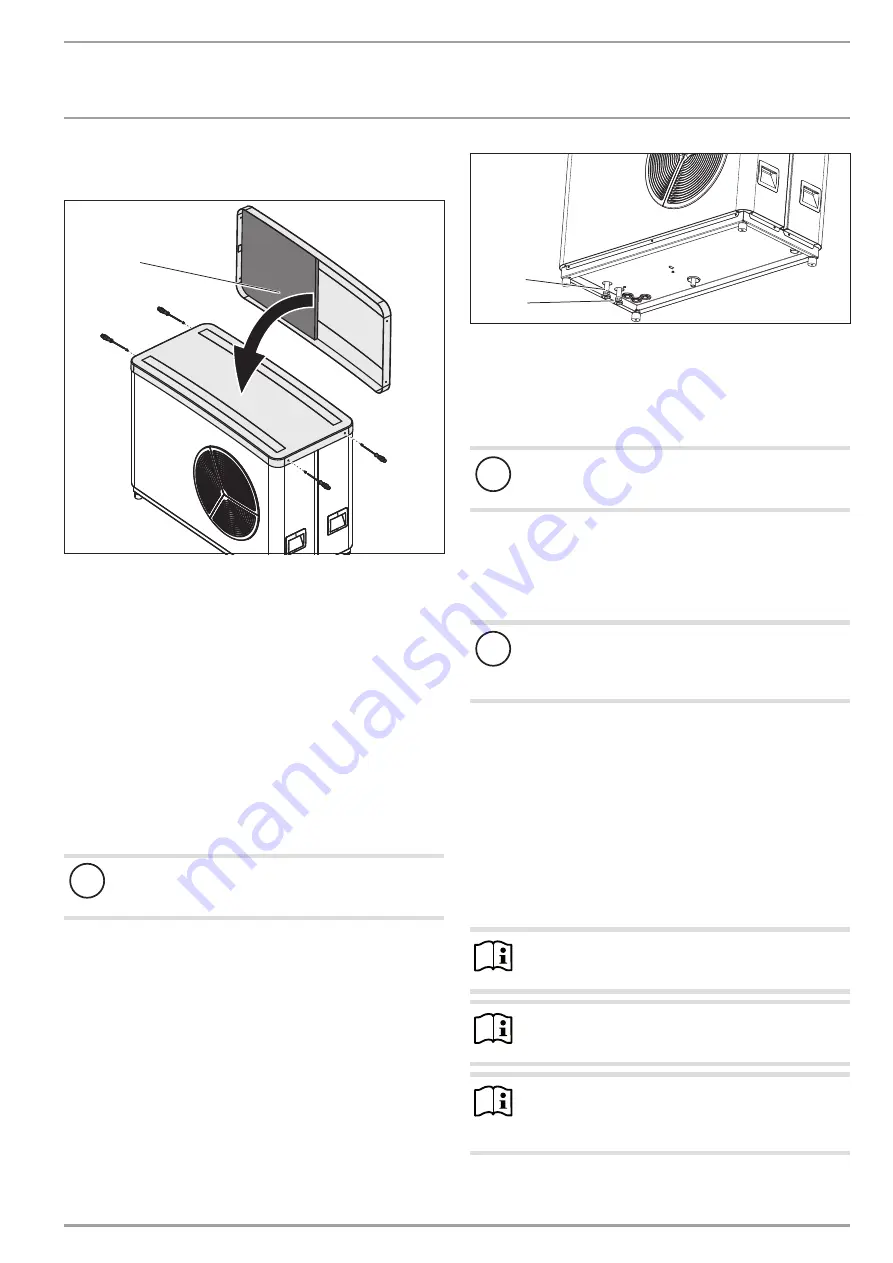
INSTALLATION
Installation
www.stiebel-eltron.com
WPL 10 AC | WPL 10 ACS |
11
f
f
Remove the transport locks (threaded rods) from the
compressor.
1
26
�0
3�
01
�1
75
9
1 Sound insulation
f
f
Position the cover on the appliance.
f
f
Secure the cover with the four screws.
10.2 Heating water connection
The heat pump heating system must be installed by a qualified
contractor in accordance with the water installation drawings that
are part of the technical documents.
f
f
Thoroughly flush the pipework before connecting the heat
pump. Foreign matter, such as welding pearls, rust, sand
or sealant will impair the operational reliability of the heat
pump and can result in the heat pump condenser becoming
blocked.
10.3 Flow and return connection
!
Material losses
Insulate the heating flow and return lines with vapour
diffusion-proof material.
Fit an anti-vibration mount at least 1 m long to the connectors.
Structure-borne noise is largely prevented by the anti-vibration
construction of the heat pump and by the flexible pressure hoses,
which act as anti-vibration mounts.
f
f
Take the position of the heating flow and return from the fol-
lowing figure:
26
�0
3�
01
�1
552
1
2
1 Heating circuit flow
2 Heating circuit return
f
f
Connect the heat pump to the heating circuit. Check for
tightness.
10.4 Oxygen diffusion
!
Material losses
Avoid open heating systems and plastic pipes in under-
floor heating systems which are permeable to oxygen.
In underfloor heating systems with plastic pipes that are per-
meable to oxygen and in open vented heating systems, oxygen
diffusion may lead to corrosion on the steel components of the
heating system (e.g. on the indirect coil of the DHW cylinder, on
buffer cylinders, steel heating elements or steel pipes).
!
Material losses
The products of corrosion (e.g. rusty sludge) can settle in
the heating system components and can result in a lower
output or fault shutdowns due to reduced cross-sections.
10.5 Filling the heating system
10.5.1 Water quality
Carry out a fill water analysis before the system is filled. This may,
for example, be requested by the relevant water supply utility.
To avoid damage as a result of scaling, it may be necessary to
soften or desalinate the fill water. Always observe the fill water
limits specified in the "Specification / Data table" chapter.
f
f
Recheck these limits 8-12 weeks after commissioning and as
part of the annual system maintenance.
Note
With a conductivity >1000 μS/cm, desalination treatment
is recommended in order to avoid corrosion.
Note
If you treat the fill water with inhibitors or additives, the
same limits as for desalination apply.
Note
Suitable appliances for water softening, as well as for
filling and flushing heating systems, can be obtained via
trade suppliers.