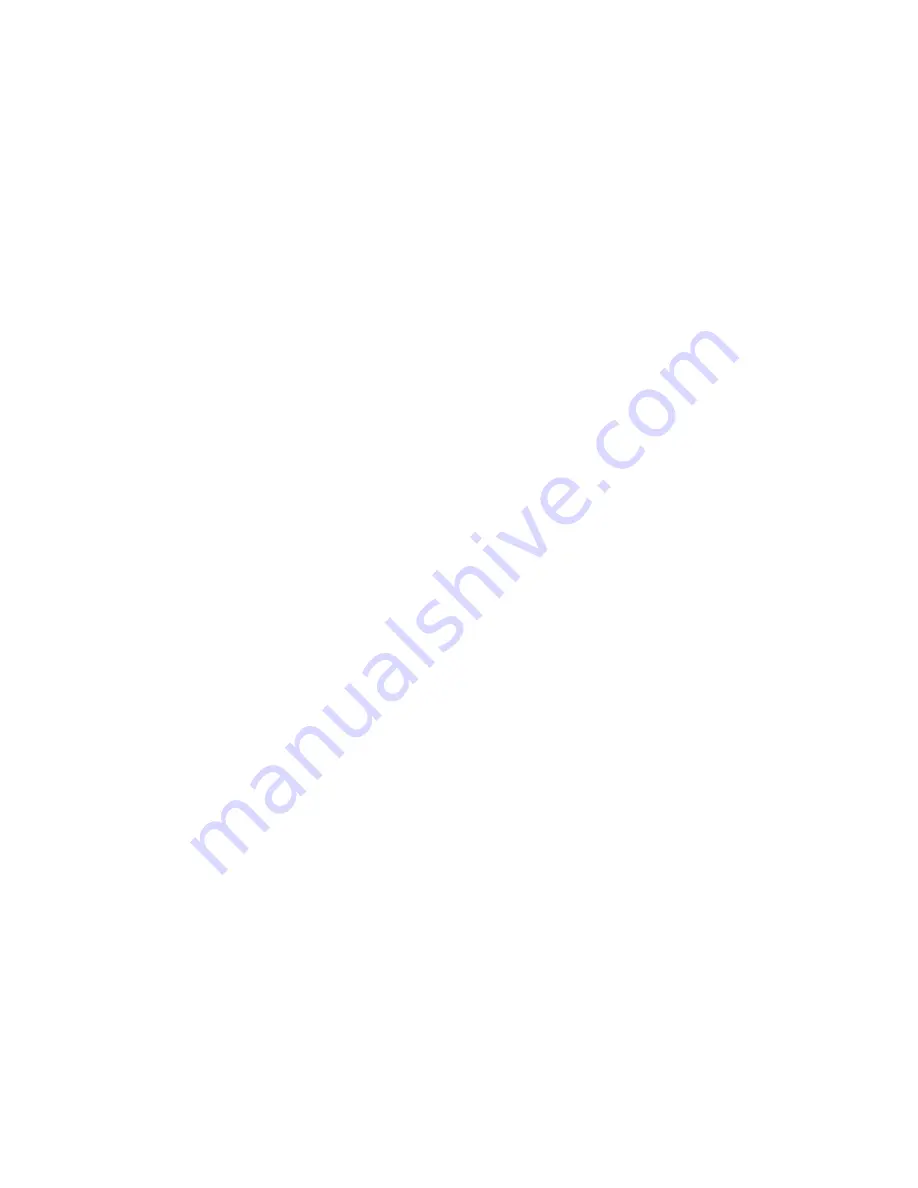
7
SECTION IV. INSTALLATION STEPS
All plumbing should be done in accordance with
state and local plumbing codes.
NOTE:
Some codes may require installation by a
licensed plumber; check with the local plumbing
authority prior to installation.
In restricted under-sink areas, it may be easier to
install the faucet first. Allow adequate tubing
lengths for any final component position.
A. Install the Faucet
See Figure 1 for Faucet Installation Diagram
The customer should be consulted before
determining faucet location. The faucet should be
positioned so that it empties into the sink and the
spout swivels freely for convenience.
If the sink already has a hole provided that can
accommodate the RO faucet, then no drilling is
required and you can proceed to the section on
mounting the faucet.
1. Make the Faucet Mounting Hole
IMPORTANT: It is mandatory that safety glasses
be worn during sink hole drilling operations to
prevent eye injury.
Before starting the hole making operation, always
check below the sink so that nothing interferes with
mounting the faucet such as reinforcing ribs,
support brackets or cabinet construction.
STAINLESS STEEL SINK:
Recommended tools:
Center punch
Variable speed drill and high speed drill bits.
Greenlee chassis punch 7/8” hole size
(alternate 9/16” size may be used for non air
gap faucet)
Protective gloves
Procedure:
a) Center punch a small indent at the desired
faucet location.
b) Slowly drill the required pilot hole for the
chassis punch.
c) Set up the chassis punch per instructions
and tighten nut to cut the desired hole
size.
d) Clean up sharp edges with a file if
necessary.
PORCELAIN/ENAMEL/CERAMIC ON SHEET
METAL OR CAST IRON BASE:
Recommended tools:
Variable speed drill
Relton porcelain cutter tool set 7/8" size
(alternate 9/16: size may be used for non-air
gap faucet)
Plumber’s putty
It is important to understand what is involved in this
procedure. First, the glassy layer of porcelain must
be penetrated through to the base metal. Second, a
center disc of porcelain must be removed while
protecting the surrounding porcelain against chip
ping or fracturing. Third, the base metal must be
drilled through to complete the hole.
Procedure:
a)
Mark the center for the 7/8” hole
b) Form shallow putty dam around hole area
and fill with enough water to lubricate
carbide drill bit.
c) Carefully drill plot hole through
porcelain/enamel and base metal using
carbide type pilot drill.
IMPORTANT: Always operate drill with light
pressure at slow speed (300-400 rpm).
d) Insert pilot tip of spring-loaded porcelain
cutter into pilot hole.
e) Drill porcelain/enamel using spring-loaded
porcelain cutter, making certain a complete
ring has been cut through the
porcelain/enamel to the metal base.
f) Change to the metal cutter. With slow
speed and light pressure, cut away the inner
porcelain/enamel disc down to base metal.
Make certain that the cutter does not touch
outer rim of the cut porcelain/enamel.
Continue with this bit to cut through metal
until sink has been completely penetrated.
IMPORTANT: When using a porcelain
cutter it is critical to take precautions that it
is always in a sharpened condition. Dull
cutters are known to chip sinks.