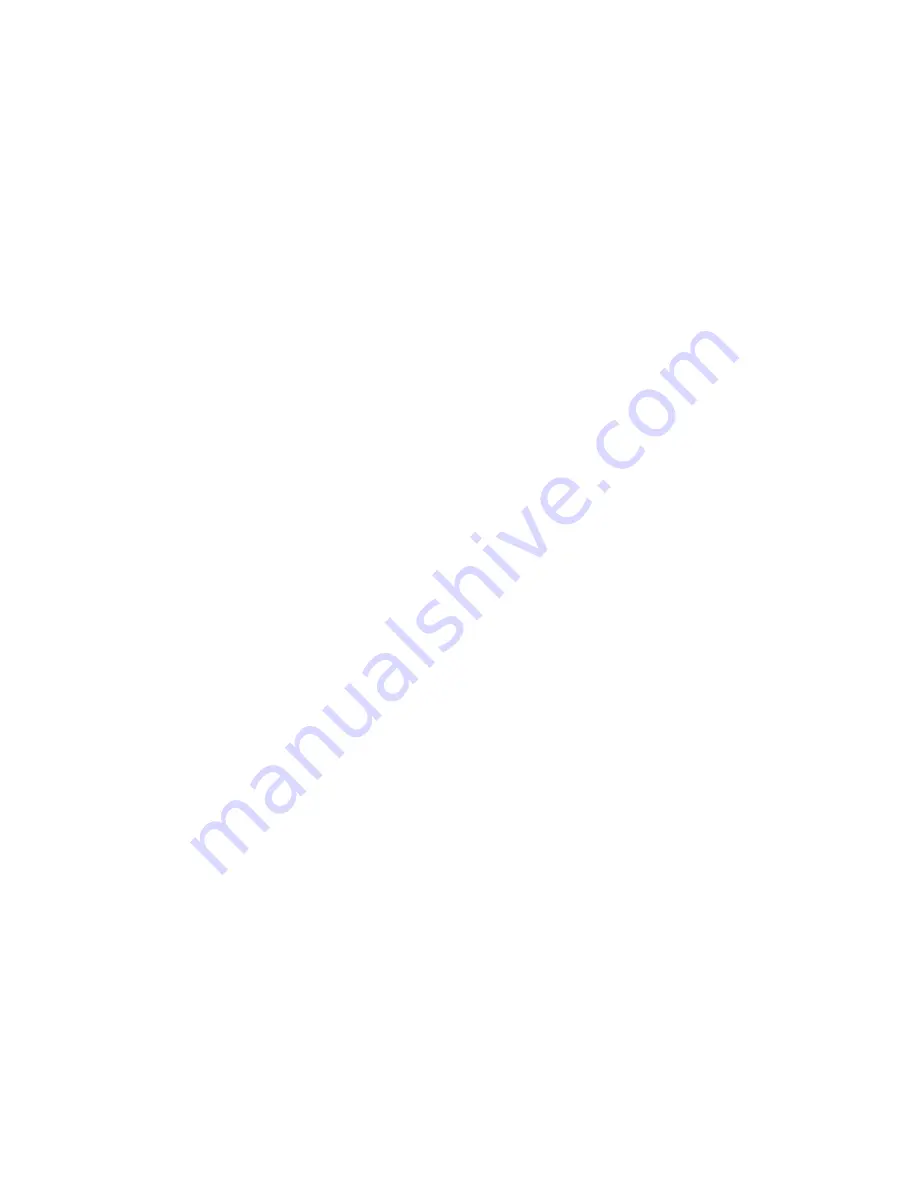
3-9
764333-675
RATE LOW"
), and the cycle aborts. The printout
indicates the temperature rate measured in the event
of a failure.
Event 11 – Test #10,
Drain Valve Test:
HTR1
de-energizes and LS3 is checked. If a not-full
condition is found, then fluid has leaked out of fluid
block or chamber, and the test fails and an alarm
occurs (Alarm:
"DRAIN VALVE FAULT"
), and the
cycle aborts. Otherwise, cycle continues to
Event 12
.
Event 12 – Test #11,
Drain Time Test:
The control
de-energizes SOL4, opening V5 and energizes SOL3,
closing V6. P1 remains on and unit starts to drain.
The control monitors the time required for LS3 to
sense a not-full condition. If the time it takes LS3 to
sense not-full is greater then five seconds, the test
fails, an alarm occurs (Alarm:
"DRAIN TIME
FAULT"
), and the cycle aborts. Otherwise, cycle
continues to
Event 13
.
Event 13 – Test #15, HP Pump Test:
During the
beginning of the drain phase, the control monitors
LS6 for open (no pressure) condition. If LS6 is not
sensed open within 10 seconds, the test fails and an
alarm occurs (Alarm:
"HP PUMP FAULT:
CLOSED"
) and the cycle aborts. Otherwise the
control energizes SOL4, closing V5, and energizes P2.
The control waits five seconds and then reads LS6 for
20 seconds. If the switch closes (senses pressure) in
allotted time, the control de-energizes SOL4, opening
the V5 and the drain continues for the remaining
40-second time period. Cycle continues to
Event 14
.
If the test fails, an alarm occurs (Alarm:
"HP PUMP
FAULT: OPEN"
) and the cycle aborts.
Event 14 – Test #12, Concentration Monitor Test:
Units take a reading of the concentration monitor
during the heat rate test. The highest reading is stored
in memory. At the end of the drain phase, SOL3 and
P1 de-energize; however, P2 remains energized for
five additional seconds. During the drain phase a
second concentration reading is taken. The difference
between the two readings must be >3 counts. If
<3 counts, the test fails and an alarm occurs (Alarm:
"CONC. MONITOR FAILED"
) and the cycle aborts.
Otherwise, the cycle continues to
Event 15
.
Event 15 – Test # 13, MaxPure Filter Test:
The control
energizes SOL8 and controls COMP1 by PT1. If 55 psi
is not reached within a three-minute time period, the
first part of this test fails, an alarm occurs (Alarm:
"MAXPURE FILTER MEMBRANE TEST
FAILED"
), and the cycle aborts.
If pressure is achieved within three minutes, the test
enters a three-minute stabilization phase where
COMP1 is energized and de-energized to maintain
55 psi for three minutes. After three minutes, the
control measures PT1. If <52.83 psi, the test fails, an
alarm occurs (Alarm:
"MAXPURE FILTER
MEMBRANE TEST FAILED"
), and the cycle aborts.
If the pressure is >52.83 psi, then COMP1 is
de-energized while SOL3 and SOL4 are energized.
The control waits 15 seconds and reads PT1. If
pressure is <51.73 or >58.75 psi, an alarm occurs
(Alarm:
"MAXPURE FILTER MEMBRANE TEST
FAILED"
). PT1 is monitored for two minutes, during
which time if the pressure drop exceeds 4.4 psig, the
test fails, an alarm occurs (Alarm:
"MAXPURE
FILTER MEMBRANE TEST FAILED"
), and the
cycle aborts. In the event of a failure, the printout
indicates three values: the pressure level achieved,
the pressure when the test failed, and the time (in
seconds) to failure. Otherwise, cycle continues to
Event 16
.
Event 16 – Test #14,
Drain Check Test:
SOL8 is
de-energized, venting the pressure from the housing
of the MaxPure Filter through CK8. After 10 seconds,
PT1 is read. If pressure is <3.51 psi or >11.7 psi, the
test fails, an alarm occurs (Alarm:
"DRAIN CHECK
FAULT"
), and the cycle aborts. Otherwise, cycle
continues to
Event 17
.
Event 17 –
Seal deflates when SOL2 energizes and
cycle is complete.
3.6 CONTROL
3.6.1 Control Assembly
The SYSTEM 1E Processor control features a
microcomputer control system. The control includes
an ink-on-paper impact printer and a 2-line x 16-
character display, to provide visual indications to the
user.
3.6.2 Control Board
The control board has two flash chips: U5 and U22.
RAM is backed up by a replaceable battery.
There are 10 low-current drivers, in sockets, on the
board, U38 through U45, U59 and U60, that provide
voltage to solenoids and solid-state relays. Each of
these outputs is protected by a replaceable fuse.
Components protected by the fuses are as follows:
Fuse
Output
Component
Device
Designation
F1
AC0
Take Up Paper
U38
F2
AC1
S8
U39
F3 AC2
S5
U40
Summary of Contents for SYSTEM 1E
Page 1: ...MAINTENANCE MANUAL SYSTEM 1E Liquid Chemical Sterilant Processing System 12 09 10 P764333 674 ...
Page 3: ......
Page 71: ...5 19 764333 675 Figure 5 2 Analog Cable Assembly Pin Out Locations ...
Page 74: ...5 22 764333 675 Figure 5 7 DC Power Supply Harness Pin Out Locations PS P1 ...
Page 96: ...7 19 764333 675 Figure 7 17 Aquafine STERIUV5 Control Panel The Control Panel A B 3 2 1 ...
Page 108: ......
Page 110: ...ii 764333 676 Example 1 How To Use IPB Page Typical ...
Page 119: ...10 764333 676 Figure 1 SYSTEM 1E Piping Schematic ...
Page 121: ...12 764333 676 Figure 2 SYSTEM 1E Complete 4 3 2 ...
Page 128: ...19 764333 676 Figure 5 Fluid and Air Components 2 of 2 51 53 48 47 50 49 52 ...
Page 133: ...24 764333 676 Figure 7 Float Block Switch Assembly 1 5 8 7 5 4 10 4 2 6 9 9 3 CK2 CK3 LS3 CK1 ...
Page 137: ...28 764333 676 Figure 9 Drain Block Assembly 3 4 5 6 7 3 1 2 8 CK8 TC3 ...
Page 143: ...34 764333 676 Figure 12 Bulkhead Connector Assembly 1 2 2 2 3 1 1 3 5 4 4 6 ...
Page 155: ...46 764333 676 Figure 18 Harness Cable Assemblies 1 of 2 1 2 3 4 5 6 P10 PT1 P5B P11 P2 P5A ...
Page 166: ......
Page 167: ......
Page 168: ......
Page 169: ......
Page 170: ......