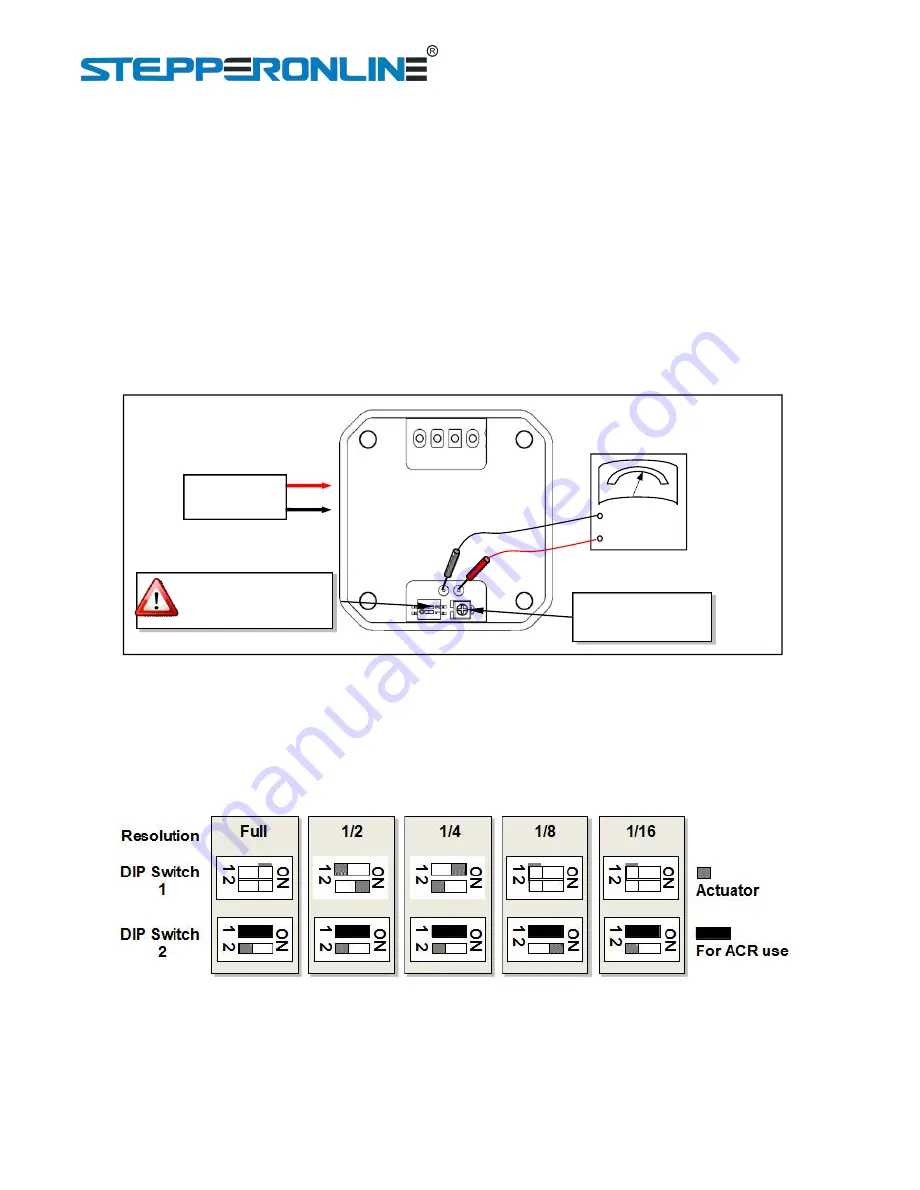
I
ntegrated Stepper Motor Driver ISD02/04/08
5
the output current.
For ISD02, a mapped voltage “Va” of 0 - 2V proportionally represents 0 - 2A.
For ISD04, a mapped voltage “Va” of 1. 5 - 4V proportionally represents 1. 5 - 4A.
For ISD08, a mapped voltage “Va” of 1. 5 - 4V proportionally represents 3 - 8A.
Note
:
The driver needs to be powered before mapped voltage “Va” can be measured. (Motor is not required to
be connected at this time. )
DIP1 (on the bottom side DIP switch 2) needs to be turned off to shut down the ACR Function.
After adjustment, user can choose to turn on the DIP1 to enable the automatic current reduction.
Current Adjustment
Trimmer
Before measuring Va:
1) Apply Power
2) Turn off DIP
Voltmeter
Mapped Voltage
Va
Bottom Side
12 ~ 40VDC
Figure 5: Adjusting the Output Current
5.2 Microstep Resolution
The microstep resolution is set by both DIP switch 1 and DIP switch 2 located at top and bottom side of
the driver as shown in following figure. ISD02/04/08 driver can provide microstep control at 200, 400, 800,
1600, 3200 step resolutions.
Figure 6: Microstep settings
5.3 Power Supply Selection
ISD02/04/08 drivers accept a wide range input voltage from 12 to 40VDC. (ISD02 takes 10 - 28 VDC) In
general, higher supply voltage improves motor performance under high speed situation, but also increases
the power loss and temperature raise.