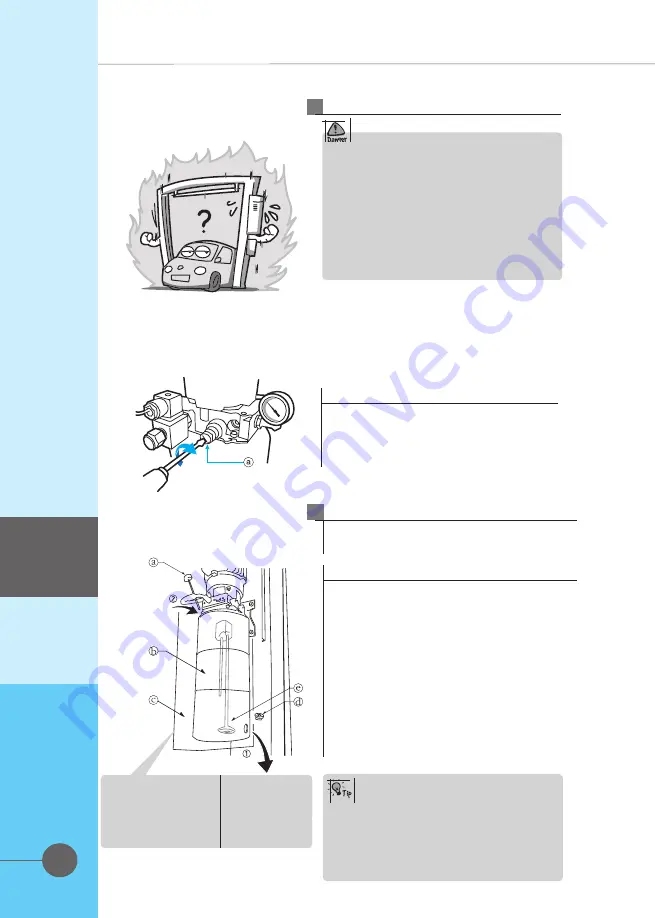
22
If machine can't lift 4,000㎏.
① Put the pressure gauge.
② Open the cap of relief valve and adjust
put up button.
The power pack pressure is set by the
factory in accordance with the lift's
maximum rated capacity. The
pressure regulator is sealed by the
factory and should not be tampered
with. Excessive adjustment can result in
serious damage. If the hoist fails to
raise the maximum rated load, contact
your approved maintenance engineer.
Power pack pressure
2
Standard pressure settings model
SB40
14 Mpa
Do this action
Maintenance
ⓐ Filter cap and dipstick
ⓑ Oil tank
ⓒ Drain plug
ⓓ Pump filter
①
Oil filter
②
Oil discharge
Oil change procedure
· Remove the cover of the hydraulic unit.
· Remove the oil filter cap and dipstick.
Carefully remove the oil drain plug and allow the oil
to discharge into a suitable container.
· Refit the drain plug and tighten
· Refill the oil tank with new oil
· Check with the dipstick that the level is
correct ; raise and lower the hoist and recheck
that the level is still correct. If not, top up with oil.
· Refit the cover
Oil change
3
Oil should be changed 2 months after
installation and thereafter annually.
At the annual oil change, after having
drained the oil tank, remove the oil
tank from the pump and check the
condition of the pump filter. Clean or
replace as necessary.
Replace tank and follow the above
procedure.