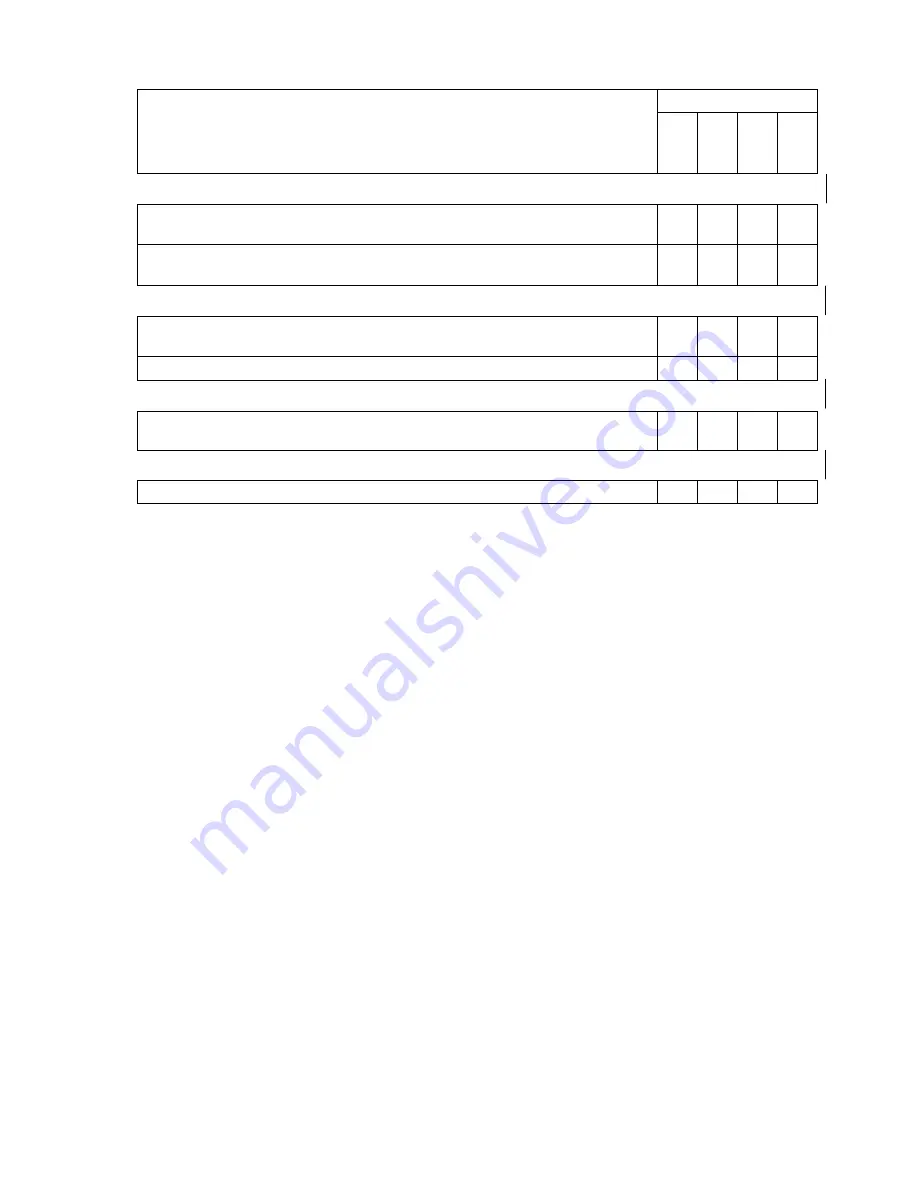
Maintenance Manual STEMME S10
Date of Issue: Oct. 01, 1990
page: 29
Amendment No.: 18
Date: Oct. 15, 2012
A4010021_B19.doc
Doc.No.: A40-10-021
Inspection Type
Type and Subject of Inspection
T
y
p
e
1
a
T
y
p
e
1
b
T
y
p
e
2
T
y
p
e
3
5.3.13 Electrical System
1. Inspect wiring and conduits for improper routing, insecure mounting and
obvious defects, electrical components for tightness of fit and poor condition.
X
2. Inspect the main battery for poor condition (check drop in voltage during starter
operation). For battery maintenance refer to manufacturer instructions.
X
5.3.14 Radio and Navigation Equipment
1. Inspect radio and navigation equipment (refer to the Equipment List) for poor
condition, improper operation and, if applicable, service life limits.
X
2. Check each antenna installed
X
5.3.15 Oxygen System
1. Inspect oxygen system, if installed, including mounting. Observe Maintenance
Instructions of the Manufacturer (Annex A).
X
5.3.16 Completition works
1. After end of maintenance on the drive train system – Engine check run
X
X
X
X
Summary of Contents for S10
Page 23: ......
Page 24: ......
Page 47: ......
Page 48: ......
Page 49: ......
Page 50: ......
Page 51: ......
Page 52: ......
Page 62: ......
Page 63: ......
Page 64: ......
Page 65: ......
Page 66: ......
Page 67: ......
Page 68: ......
Page 69: ......
Page 70: ......
Page 71: ......
Page 72: ......
Page 73: ......
Page 74: ......
Page 75: ......
Page 76: ......
Page 77: ......
Page 82: ......
Page 83: ......
Page 85: ......
Page 86: ......
Page 87: ......
Page 93: ......