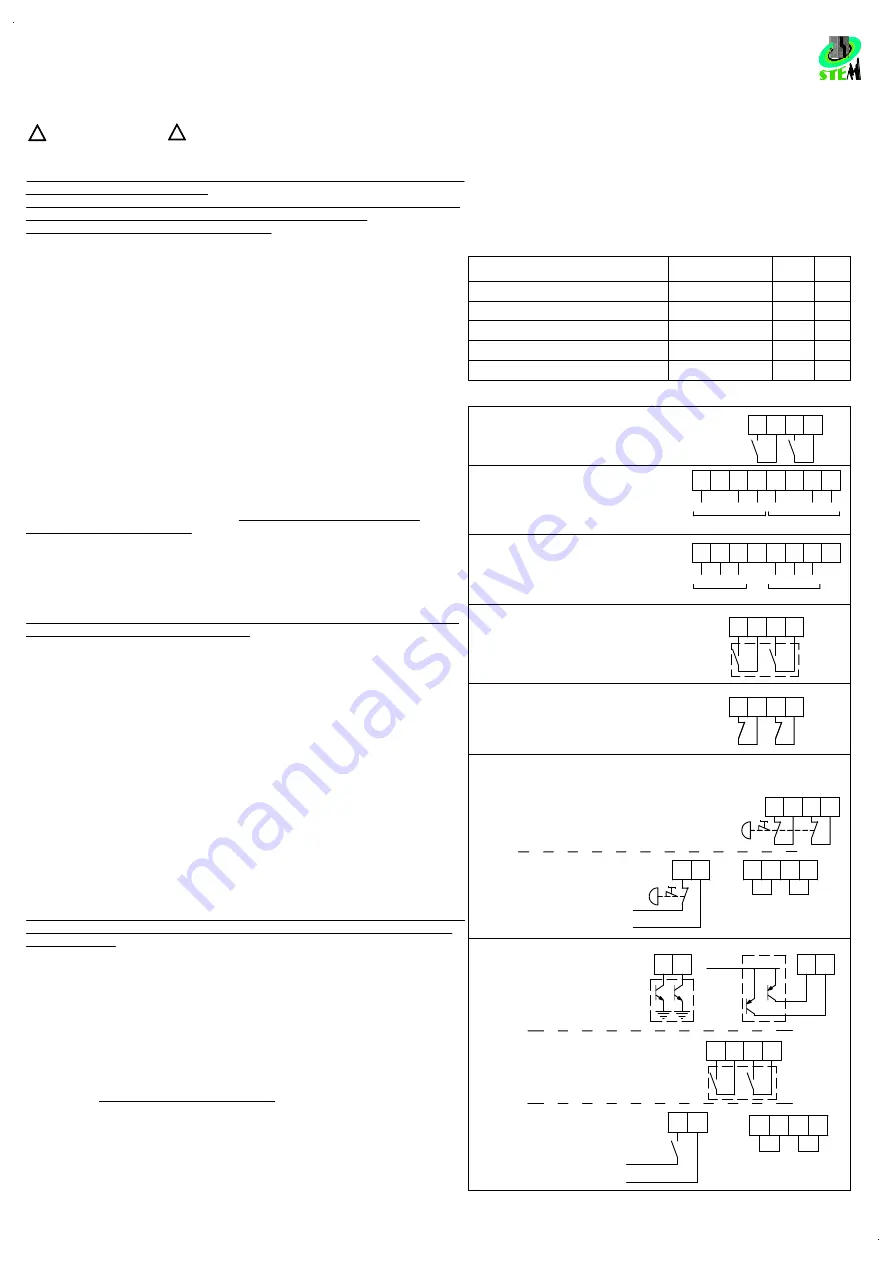
Operating instructions for safety control unit mod. NC85
- Original instructions -
!
Description
The NC85 safety relay is created for use in safety circuit intended by
EN 81-20, EN 81-50, EN 60204-1, EN ISO 13849-1, EN 61496-1.
This module is based upon the use of guided-contact safety relays.
Safety Precautions
The manufacturer or the technician that install the machinery is responsible for correct and
safe overall function.
Auxiliary output Y1/Y2 is optoinsulated and gives informations about the state of the device;
it must not be used as a safety output.
The
NC85
is not proper for the operation in presence of ionizing and not ionizing radiations
(rays X, microwaves, laser, ultraviolet rays) (EN 60204-1:2018, §4.4.7).
The
NC85
CANNOT be disposed as generic waste.
Functioning
The
NC85
Module can control the state of two contacts (Reed or Hall effect sensors,
emergency stop button, mechanical safety switches, interlocks for mobile guards, safety light
curtains): the output is activated by pressing the START button only if the contacts of two
sensors are closed. The opening of one input contact (S1 and/or S2), leads to a safety
situation, by putting the safety outputs in open state and by preventing the closing even after
the re-closing of the contact and the pressure of the START button.
WARNING: the start command does not fulfill the requirements of §5.2.2
of EN ISO 13849:2015 standard because it works on the rising edge of the signal.
If the
NC85 is used to control emergency stop button, after the intervention of the
device, the reset of the command shall not restart the machinery but only permit restarting
(EN 60204-1:2018, §9.2.3.4.2, EN ISO 13850:2015, §4.1.4). If the NC85 is used to control
interlocks for mobile guards, the reclosing or resetting of an interlock safeguard shall not
initiate hazardous machine operation (EN 60204-1:2018, §9.3.1).
If START button is not used (automatic rearmament), see the connection diagram in the
following page; the behavior of the machinery to the restart of the device - or the not
automatic restart of the dangerous elements of the machinery - depends on the realization of
the command circuit of the machinery according to the risk evaluation effected by the user.
Input channels work on opposite potentials (S11,S31
→
-
; S21,S41
→
+
).
It's available an input (X1-X2) for feedback with contactors or external relays
(see Ka and Kb on the connection diagram); if not used, X1-X2 have to be bridged.
Safety category 4 is granted only if (see connection diagram):
- to interrupt the load are used two relays, each connected to an input of the safety unit;
- the contacts of the relays controlled by the safety unit are inserted into the feedback loop.
The safety is ensured by using guided contacts, by the redundance and by the
interconnection schematic of the contacts.
The responsibility to choose the adequate components for safety applications, for example
guided contacts safety relays, falls to the user.
Assembly
Installation must be performed by authorized personnel only. The NC85 control unit must be
assembled in a suitable operating area (switch cabinet, protective housing).
The unit is installed by clipping it to a standard 35 mm top-hat rail.
Electrical Connection
Electrical connection must be performed by authorized personnel only following the
indications of EN ISO 13849-1 and EN ISO 13849-2.
All the electrical inputs must either be isolated from the mains supply by a separate coils
safety transformer in accordance with IEC EN 61558-2-6 with limited output voltage in the
event of a defect or by another equivalent movable mechanism.
The outputs of the relays have a maximum current of 3 A; the supply connectedto the outputs
must be protected from overcurrents by devices adequate to the loads that have to be
protected. All the output contacts must have an adequate protective circuit for capacitive and
inductive loads.
If a common power supply is used, all the inductive and capacitive loads (e.g. relay
contactors) connected to the power supply must be connected to appropriate interference
suppressors.
Service and Inspection
The correct functioning of the NC85 safety unit must be controlled by the operator and/or by
the control circuit of the machine in which it is used periodically (at the beginning of every
shift), by checking:
- Correct switching function of each sensor by checking:
a) that the opening of the single sensor / safety guard will cause the opening of the
safety outputs (13-14 / 23-24)
b) that the closure of the same sensor / safety guard will cause the closing of the
safety outputs (13-14 / 23-24) as a result of a startup command
- secure mounting of components
- correct connection fixing.
The monitoring function of the unit is done at every switching cycle. If with all safety guards
closed and following the eventual start command, the safety device does not activate its
safety outputs, do not turn off and turn on the device , then proceed to the checking of the
possible safety guard open and perform the above tests in point a) and b).
In the event of damage or wear and tear, the damaged system component must be replaced.
Liability coverage is void under the following circumstances:
- if instructions are not followed
- non-compliance with safety regulations
- installation and electrical connection not performed by authorized personnel
- non-implementation of functional checks.
!
Setup
If the control unit does not appear to function when operating voltage
is applied (green LED PWR does not light up), the unit must be returned
unopened to the manufacturer.
Check whether the safety outputs are being switched (see LED display) by
activating the two inputs S1, S2 and START.
Operation according to EN 81-20:2014
The safety module ensures the opening of contacts within 15 ms from the
opening of the sensors S1 or S2.
It can be used as a detector, according to 5.6.7.7 EN 81-20:2014,to be
integrated in a A3 system.
1) Lift applications (EN81-20,EN81-50):
Reed contact sensors S1 e S2
2) Lift applications
(EN81-20, EN81-50):
NPN static output devices S1 and S2
3) Lift applications
(EN81-20,EN81-50):
PNP static output devices S1 and S2
4)
Machine safety applications
(cat.4 EN ISO 13849-1:2015):
sensor (S1) with 2 normally open
(N.O.) contacts
5)
Mobile guard interlock sensors with
normally closed
(N.C.) contacts
(EN 14119;
cat.4 EN ISO 13849-1;
EN 60204-1:2018, §9.3)
6)
Control of an emergency stop button in accordance with EN ISO 13850
(stop category 0, EN ISO 13850;
EN 60204:2018, §9.2.3.4)
LED Table
Inputs S1, S2, START: OPEN
S1, S2, START
Power
LED
OUT
OUT
on
State
on
off
off
-
green
green
-
Color
(ON)
Inputs S1, S2, START: CLOSED
on
green
S1, S2, START
7)
Safety light curtains:
2 static outputs NPN or PNP
(Tipo 4, EN 61496-1)
2 N.O. outputs (B1)
(Tipo 4, EN 61496-1)
Bridge the inputs if not
used for 2 NO contacts
sensor
Power supply
24 V ac/dc
with 2 N.C. contacts (S1) (cat 4 EN ISO 13849-1)
with 1 N.C. contact (S2)
(cat 4 EN ISO 13849-1)
Inputs
S21
B2
S12
S22 S11
Bridge the inputs if not
used for 2 NO contacts
sensor
Power supply
24 V ac/dc
A1 A2
L1 +
L2
-
1 N.O. output (B2)
(Tipo 2, EN 61496-1)
+
-
Outputs 13/14, 23/24 and Y1/Y2: CLOSED
Outputs 13/14, 23/24 and Y1/Y2: OPEN
Function
Supply Voltage
S
ub
je
ct
t
o
te
ch
ni
ca
l m
od
ifi
ca
tio
n
s
w
ith
ou
t n
o
tic
e
, n
o
li
a
bi
lit
y
w
ill
b
e
a
ss
um
ed
f
or
a
ny
d
et
ai
l.
©
S
T
E
M
S
.r
.l.
1
S
M
A
N
C
85
0
00
0
r
ev
.1
8_
03
/2
2
S11
S22
S21
S12
S2
S1
S31
S11
S22
S21
S41
S12
S42
S32
+
signal
+
signal
S1
S2
_
_
S22
+
S21
signal
_
+
S11
S41
S12
S42
signal
S31S32
S2
S1
_
+
-
S11
S22
S21
S12
S1
S11
S22
S21
S12
S2
S1
+
-
+
-
S21
S1
S12
S22 S11
+
-
S21
S2
S12
S22 S11
A1 A2
L1 +
L2
-
+
-
S12 S32
S22 S42
NPN
+24Vdc
PNP
S11
S22
S21
S12
B1
+
-