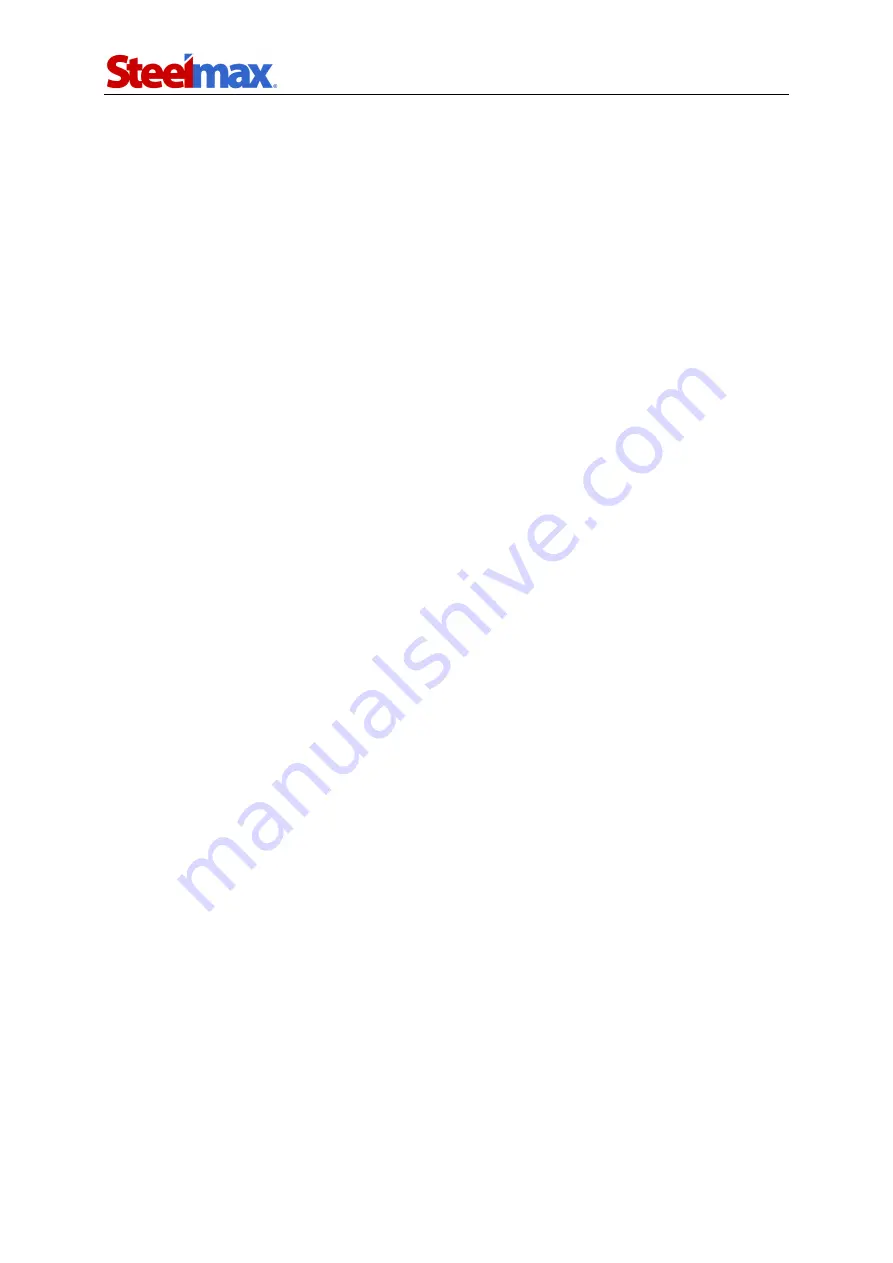
Torch Runner (HS)
Torch Runner (HS) Operator’s Manual
13
4. MAINTENANCE
Daily:
1. Clean the wheels.
2. Clean the torch nozzle. Replace if damaged.
Monthly:
1. Check whether the knob and switches work as intended. Replace if loose or
damaged.
2. Inspect cables, cords, and hoses. Replace if damaged.
3. Tighten screws if loose.