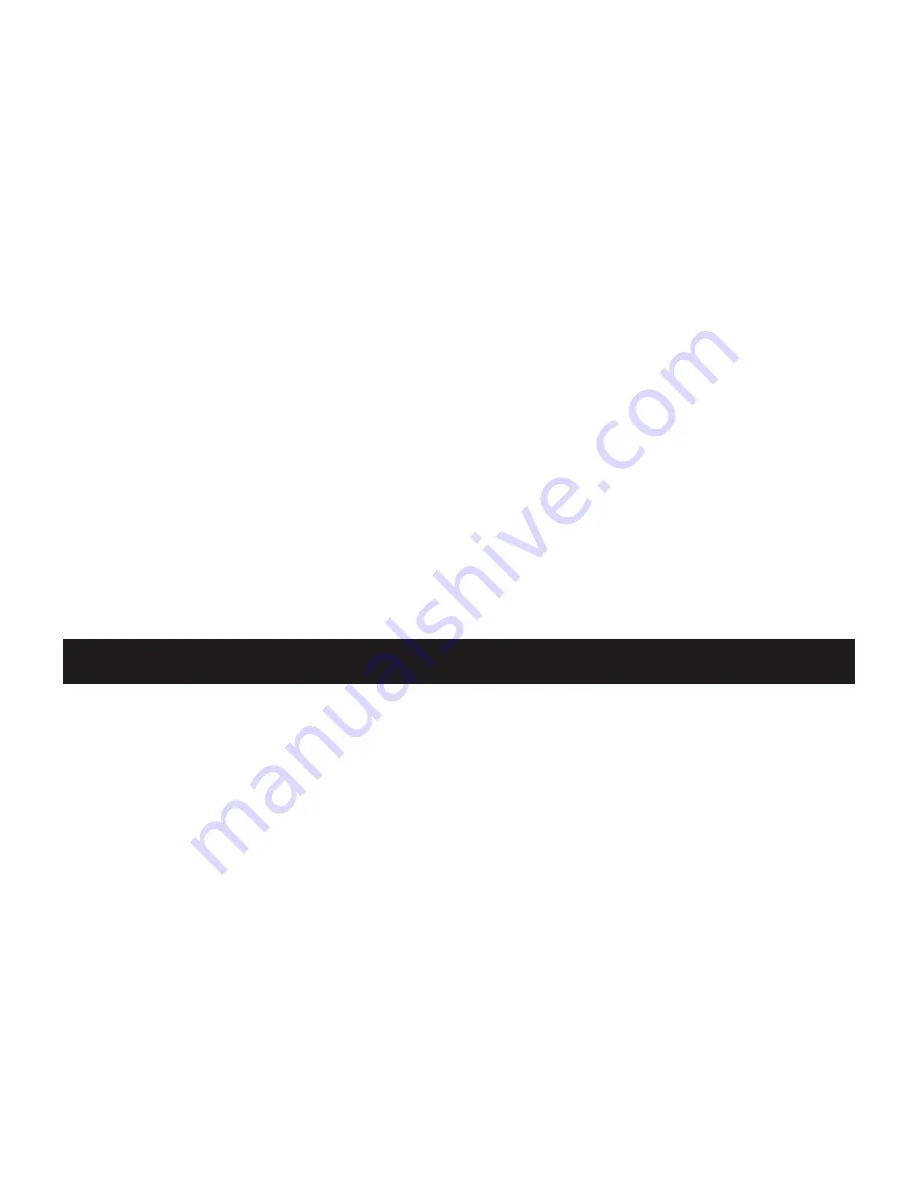
9
28.
OBTAIN ADVICE FROM YOUR SUPERVISOR
,
instructor, or another qualified person if you are not
familiar with the operation of this drill press.
29.
PROPERLY SUPPORT
long or wide workpiece and
clamp to the table.
30.
PROPERLY SECURE
the drill bit, cutting tool, or
sanding drum in the chuck before operating the drill
press.
31.
REPLACE
a damaged cord immediately.
DO NOT
use a damaged cord or plug.
32.
SECURE
the drill press to the floor or work bench.
Vibration can cause the drill press to slide, walk or
tip over. Do not attach the drill press to a mobile
base.
33.
SECURE
the workpiece firmly against the table.
Do not attempt to drill a workpiece that does not
have a flat surface against the table, or that is not
ELECTRICAL REQUIREMENTS
TO PREVENT
electrical shock, follow all electrical and
safety codes, including the National Electrical Code
(NEC) and the Occupational Safety and Health
Regulations (OSHA). All electrical connections and
wiring should be made by qualified personnel only.
TO REDUCE
the risk of electrical shock,
DO NOT
use
machine outdoors.
DO NOT
expose to rain or mois-
ture. Store indoors in a dry area.
DO NOT
connect the machine to the power source
before you have completed the set up process.
DO NOT
connect the machine to the power source until
instructed to do so.
The motor supplied with the drill press is a 115 volt,
single phase motor. The motor is wired from the factory
for 115-volt operation.
27.
NEVER START THE DRILL PRESS
with the drill
bit, cutting tool, or sanding drum against the work-
piece. Loss of control of the workpiece can cause
serious injury.
secured by a vise. Prevent the workpiece from
rotating by clamping it to the table or by securing it
against the drill press column. Loss of control of the
workpiece can cause serious injury.
34.
SECURELY LOCK
the head and table support to
the column, and the table to the table support
before operating the drill press.
35. The drill press is designed for home use or light
commercial duty
ONLY
.
36.
TO REDUCE THE RISK OF ELECTRICAL
SHOCK
, do not use outdoors. Do not expose to
rain. Store indoors in a dry area.
37.
TURN THE DRILL PRESS OFF
and unplug from
power source. Wait for the drill bit, cutting tool, or
sanding drum to come to a complete STOP before
cleaning off the table/work area, removing or secur-
ing workpiece, or changing setup.
38.
USE
only drill bits, cutting tools, sanding drums, or
other accessories with proper shank size recom-
mended in this instruction manual. The wrong size
shank can cause damage to the drill press and/or
serious injury.
39.
USE RECOMMENDED SPEEDS
for all operations.
Improper speeds may cause the machine to mal-
function causing damage to the drill press and or
serious injury.
26.
NEVER START THE DRILL PRESS BEFORE
CLEARING THE TABLE OF ALL OBJECTS
(tools,
scrap pieces, etc.). Debris can be thrown at high
speed.