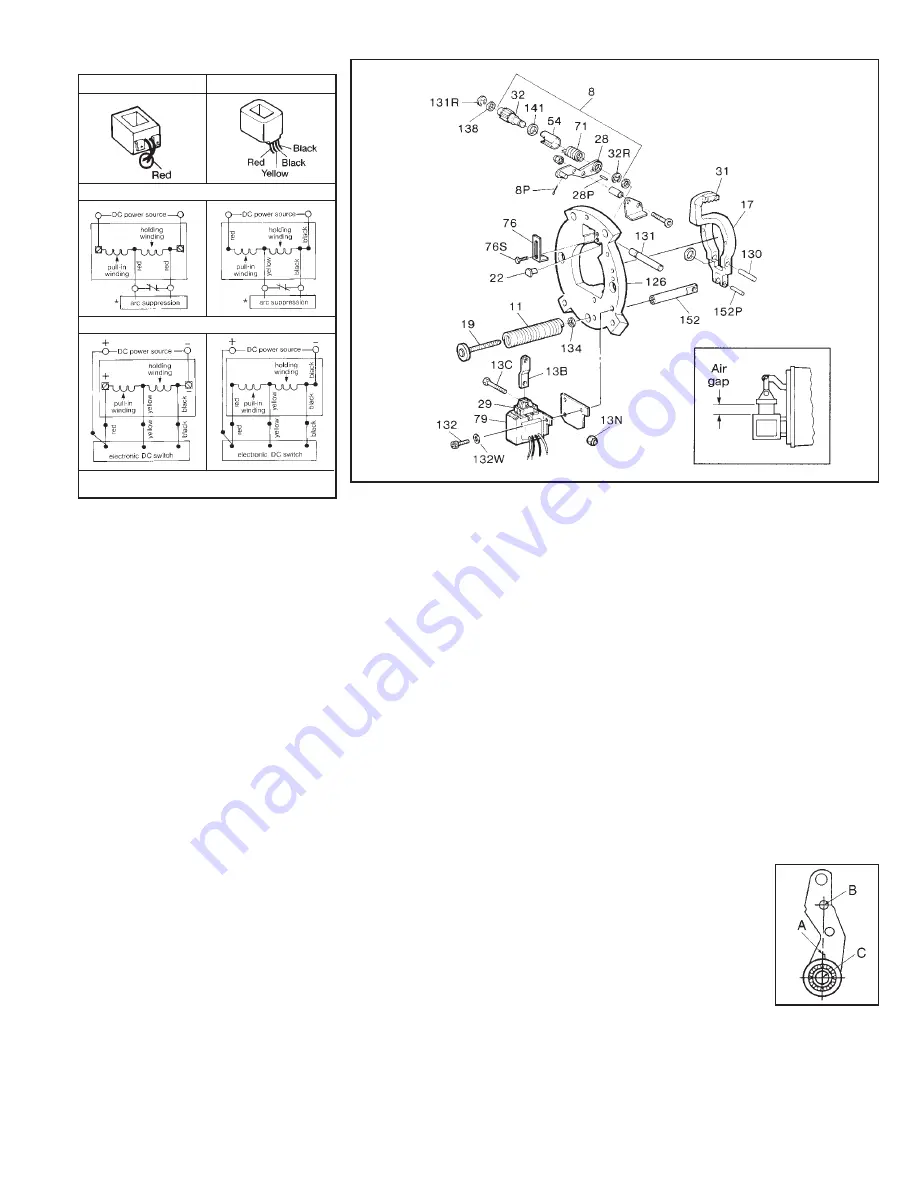
III. General Maintenance
Warning! Any mechanism or load held in
position by the brake should be secured to
prevent possible injury to personnel or damage
to equipment before any disassembly of the
brake is attempted or the manual release lever
is operated on the brake. Observe all
cautions
listed at the beginning of this manual.
Note 1: Replacement part kits for many items
are available and contain retrofit instructions.
Note 2: Do not lubricate any part of the brake
as this may cause a malfunction and/or loss of
torque.
A. Coil replacement
All standard NEMA AC voltage coils are
available in kits. Select coil kit from appropriate
replacement parts list for the particular brake
series being serviced.
All standard NEMA DC voltage coils are
available in assemblies and may also be
obtained from appropriate parts list.
B. Friction disc replacement
Note: Replace friction discs in single disc
brakes when wear surface area is one half the
original disc thickness (1/4”). In multiple disc
brakes, replace all friction discs when throat of
lever arm (17) is within 1/16” of touching teeth
of pinion (32).
1. Replacement friction discs for use with either
square or splined brake hubs are available
in kits. Select applicable kit from appropriate
parts list for the brake being serviced.
2. If brake uses metal carrier rings with bonded
friction linings (P/N 5-18-7001-00) for use
with splined hub obtain required quantity.
Then proceed as follows:
a) Observe cautions and warnings
preceding
Installation Procedure
,
Section I. Follow Steps L and K then
disconnect solenoid lead wires.
b) Continue with Steps C through E and
Steps G through L. Be sure to reconnect
coil leads before replacing housing (7).
C. Other standard replacement parts
The standard 87,700 Series brakes use
replacement part kits or components
depending on the items involved. Consult Parts
List P/N 8-078-917-07 (Sheet 366) for material
needed.
D. Self-adjust maintenance
(See Figure 6)
Since the self-adjust brake automatically
adjusts itself for friction disc wear, maintenance
is held to a minimum. The solenoid is factory
set with a 13/16” to 15/16” air gap, and
requires no resetting, even when changing
friction discs. The gap is determined by the
position of wrap spring stop (76). Should air
gap change, follow the steps listed below:
1. If (stop) screws (76S) had been loosened
and retightened, the air gap may require
resetting. The gap is measured between
mating surfaces of plunger (29) and solenoid
frame (79), and may be increased by raising
slightly, or decreased by lowering slightly,
wrap spring stop (76). Be sure to retighten
(stop) screws (76S). Manually lift plunger to
maximum travel and release. Depress
plunger, manually or electrically, and allow it
to snap up. Repeat several times, then
recheck air gap for factory setting of 13/16”
to 15/16”.
Note: To measure solenoid air gap on
vertically mounted brakes, grasp solenoid
link to hold plunger in a free horizontal
position and move toward solenoid frame
until spring pressure is felt. Holding firmly in
this position measure air gap between
mating (ground) surface on solenoid frame
and solenoid plunger. Adjust to proper gap
as directed in
Self-Adjust Maintenance.
Check gap by again holding plunger as
directed.
2. Tang of wrap spring (71) must be below, and
must make contact with, wrap spring stop
(76) when solenoid lever (28) is manually
raised. If stop is bent outward, allowing tang
to bypass it, rebend to square position,
assemble correctly, and reset solenoid air
gap as described in Paragraph 1.
3. Should air gap have decreased or
disappeared, the solenoid lever and pinion
assembly (8) may have become
contaminated due to lubrication or residue
as a result of overheating of brake. Cleaning
is required. Loosen pressure spring nut (19)
until pressure spring (11) is free. Remove
support plate assembly (142). Remove
cotter pin (8P) from solenoid lever (28) and
retaining ring (131R) from pivot pin (131).
Note location of spacer washer (138) if used,
and push pivot pin out to free affected
assembly. Remove retaining ring (32R) from
pinion (32) and disassemble. Parts should
be thoroughly cleaned in a clean solvent that
does not leave a film M.E.K. or equivalent.
Dry all parts thoroughly
and reassemble.
Rotate
pinion and wrap spring
clockwise until tang (A)
is aligned with
centerline of the upper
hole of the lever arm.
Refer to Figure 7.
Reassemble in reverse
order of Steps in this
Paragraph. Do not
retighten cap screw (19)
until support plate
assembly is mounted on endplate. Refer to
Steps H and I of
Installation Procedure
to
complete assembly.
4. Check condition and positioning of pinion
(32) and rack (part of lever arm assembly
Figure 6
DC Voltage Coil Connection
Figure 5
*Arc suppression used for coil above 48 Vdc.
**Follow polarity for switch to operate.
Electronic Switch**
(New Style)
Mechanical Switch
(Old Style)
Class B
Class H
Figure 7