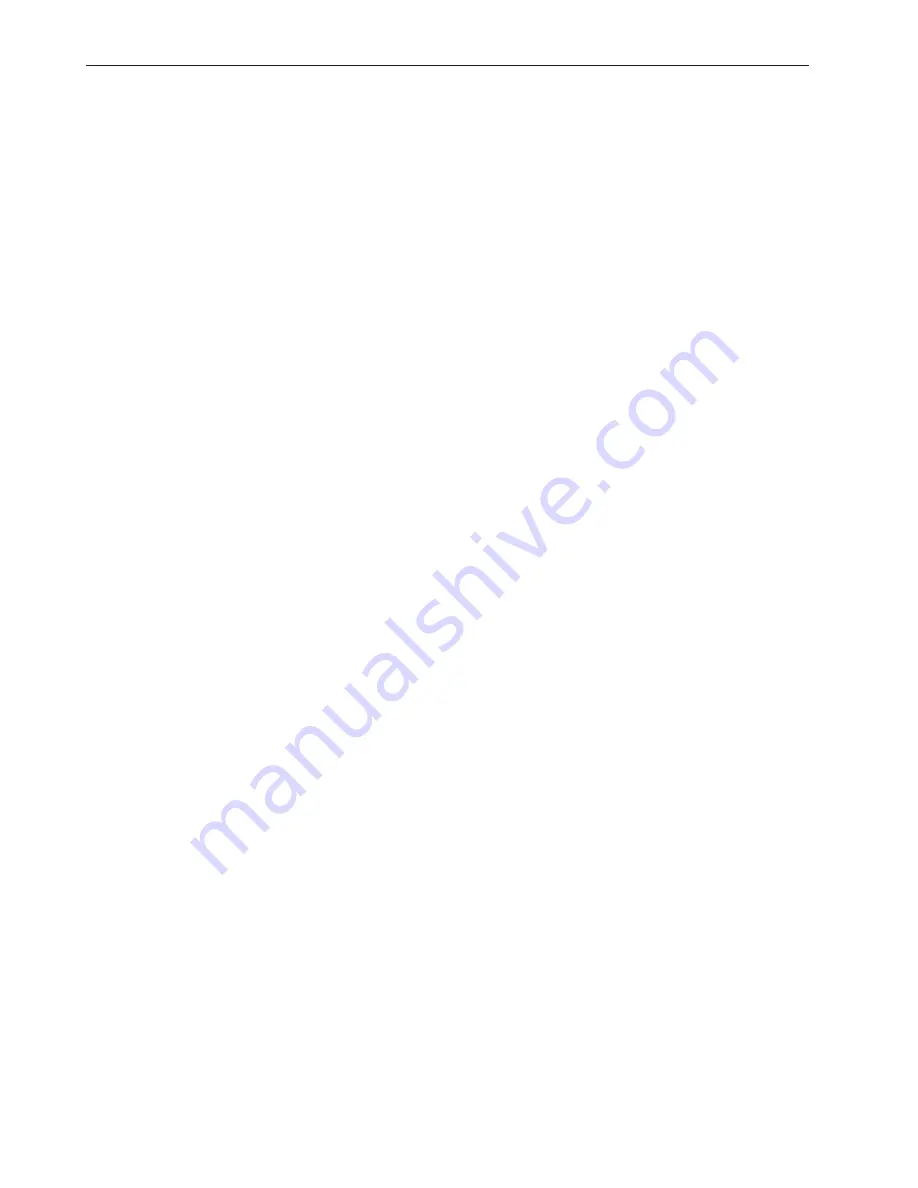
STEALTH DIGI-MIG 200
17
1. Choose welding mode key:
On TIG or MIG, press the key to choose 2T or 4T welding mode.
2. Choose welding method key:
Press the key to choose three functions – MMA/TIG/MIG.
3. Welding current knob:
Set the welding current.
4. Current display:
Displays when machine is working. Set current display before welding. Unit A.
5. Current LED:
When the current LED is lit, it displays the actual output welding current (MIG).
6. Wire speed LED:
Use current setting knob to set the wire speed when LED is lit (MIG).
7. Voltage display:
Displays when machine is working Set voltage display to MIG mode before welding.
Unit V.
8. Welding voltage / Down slope / Arc force knob:
On MIG, when the program voltage cannot match the welding current, the knob
can adjust voltage. On TIG, the knob can adjust the current down time. On MMA,
the knob can adjust the force current.
9. Power LED:
Power LED is lit when the machine is turned on.
10. Alarm LED:
When the welder is over voltage, less voltage, over current or over heated, the
alarm pilot lamp will light.
11. Wave control knob:
Controls arc characteristics determines the rate at which the amperage rises when
a short circuit is produced.
12. TIG GAS connect.
13. MIG GUN connect.
14. Output cathode:
When in MIG mode, this polarity must connect to the work piece
15. TIG gun control connecter.
16. Output anode:
When in TIG mode, this polarity must connect to the work piece.
17. Remote switch.
18. Spool Gun switch.
19. Burnback knob.
20. Slow feed knob.
21. Manual wire switch and air check switch: UP for manual wire and DOWN for air check.
22. Post flow knob.
23 Pre-flow knob.