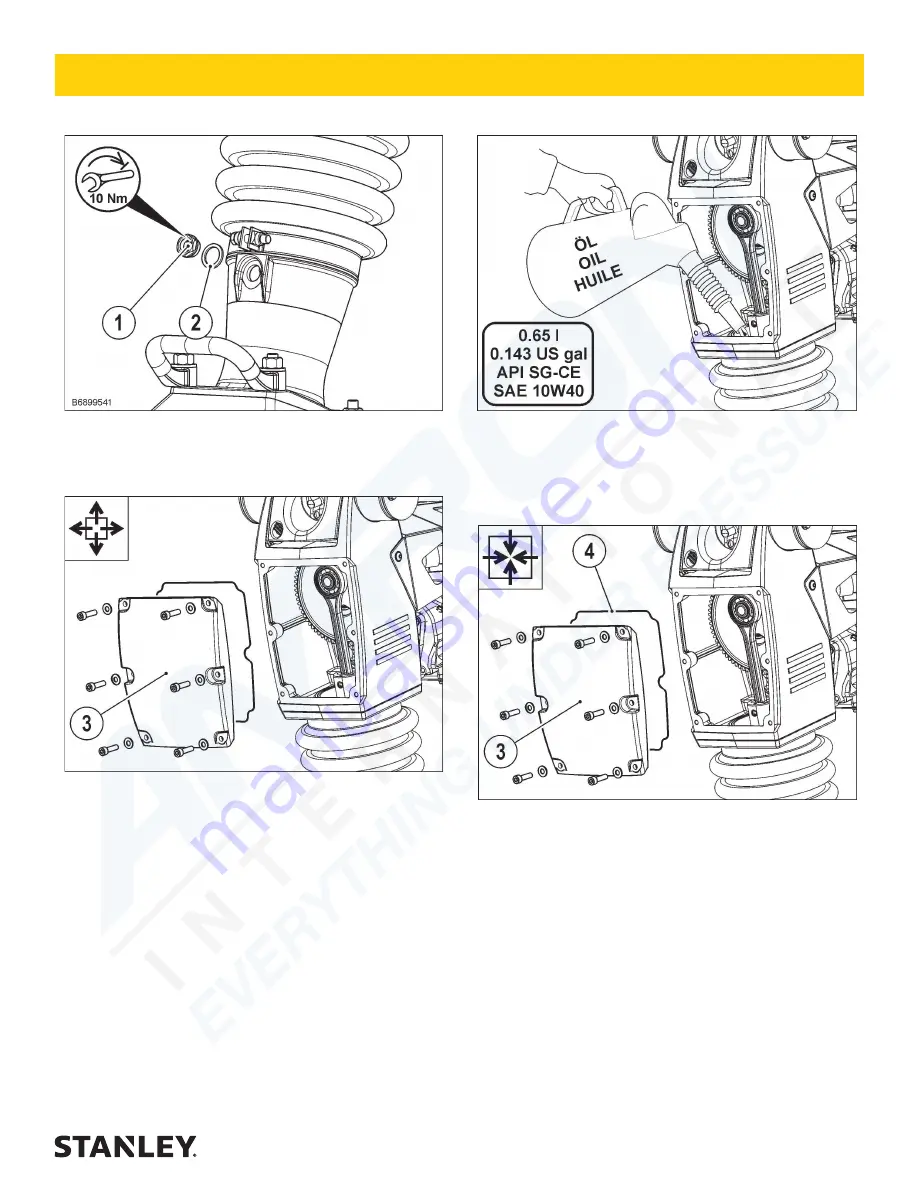
SRA User
Manual ◄ 25
MAINTENANCE
• Stand the tamper back up, and screw in the oil sight glass
(1) with its seal (2).
• Remove the housing cover (3).
• Pour fresh oil directly into the guide tube.
• Clean the sealing surfaces between the cover (3) and the
housing; avoid damage.
• Check the oil level in the sight glass, and add oil, if
necessary.
• Install the cover (3) with its seal, making sure the seal is
seated properly. Replace defective seals.