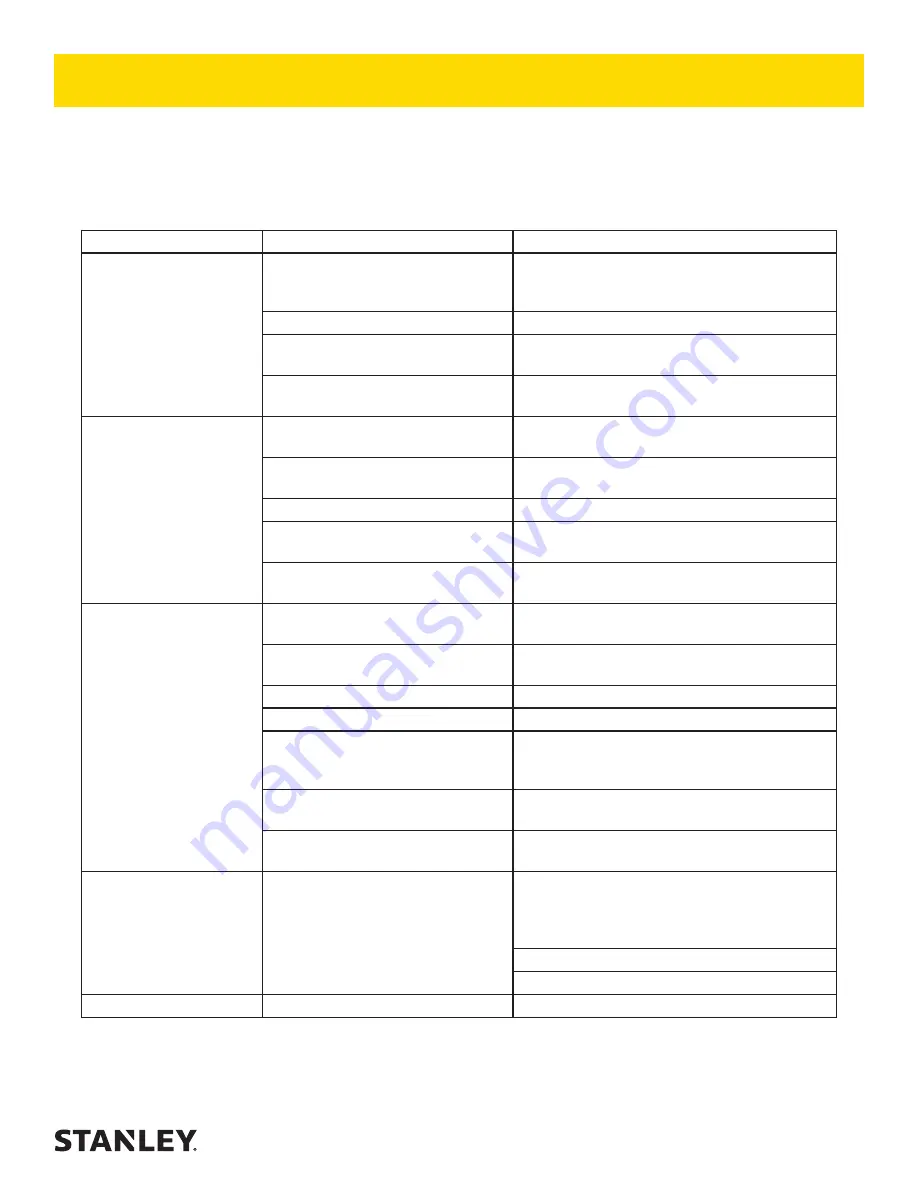
PD45 User
Manual ◄ 13
If symptoms of poor performance develop, the following chart can be used as a guide to correct the problem.
When diagnosing faults in operation of the tool, always make sure the hydraulic power source is supplying the
correct hydraulic flow and pressure as listed in the table. Use a flow meter know to be accurate. Check the flow with
the hydraulic fluid temperature at least 80 °F/27 °C.
PROBLEM
CAUSE
SOLUTION
Tool does not run.
Power unit not functioning.
Check power source for proper flow and
pressure (7–9 GPM/26–34 LPM, 2000 psi/140
bar).
Couplers or hoses blocked.
Remove restriction.
Pressure and return line hoses
reversed at ports.
Be sure hoses are connected to their proper
ports.
Mechanical failure of piston or
automatic valve.
Disassemble post driver and inspect for
damaged parts.
Tool does not hit
effectively.
Low accumulator charge (pressure
hose will pulse more than normal).
Recharge accumulator. Replace diaphragm if
charge loss continues
Power unit not functioning.
Check power unit for proper flow and pressure
(7–9 GPM/26–34 LPM, 2000 psi/140 bar).
Couplers or hoses blocked.
Remove restriction.
Fluid too hot (above 140 °F/60 °C). Provide cooler to maintain proper oil
temperature (130 °F/55 °C maximum).
The anvil is not sliding freely in the
post driver foot.
Remove, clean, lubricate and replace anvil as
required.
Tool operates slowly.
Low GPM supply from power unit.
Check power source for proper flow (7–9
GPM/ 26-64 LPM).
High back-pressure.
Check hydraulic system for excessive back-
pressure (over 250 psi/17 bar).
Couplers or hoses blocked.
Remove restriction.
Orifice blocked.
Remove restriction.
Fluid too hot (above 140 °F/60 °C)
or too cold (below 60 °F/16 °C).
Check power source for proper fluid
temperature. Bypass cooler to warm fluid up or
provide cooler to maintain proper temperature.
Relief valve set too low.
Adjust relief valve to 2100–2250 psi/145–155
bar.
The anvil is not sliding freely in the
post driver foot.
Remove, clean, lubricate and replace as
required.
Tool gets hot.
Hot fluid going through tool.
Check power unit. Be sure flow rate is not too
high causing part of the fluid to go through the
relief valve. Provide cooler to maintain proper
fluid temperature (140 °F/60 °C max).
Check relief valve setting.
Eliminate flow control devices.
Oil leakage on post.
Lower piston seal failure.
Replace seal.
TROUBLESHOOTING
Summary of Contents for PD45
Page 2: ......
Page 17: ...PD45 User Manual 17 PD45132 PD45151 PARTS ILLUSTRATION 44A 21A 15A 16 ...
Page 19: ......