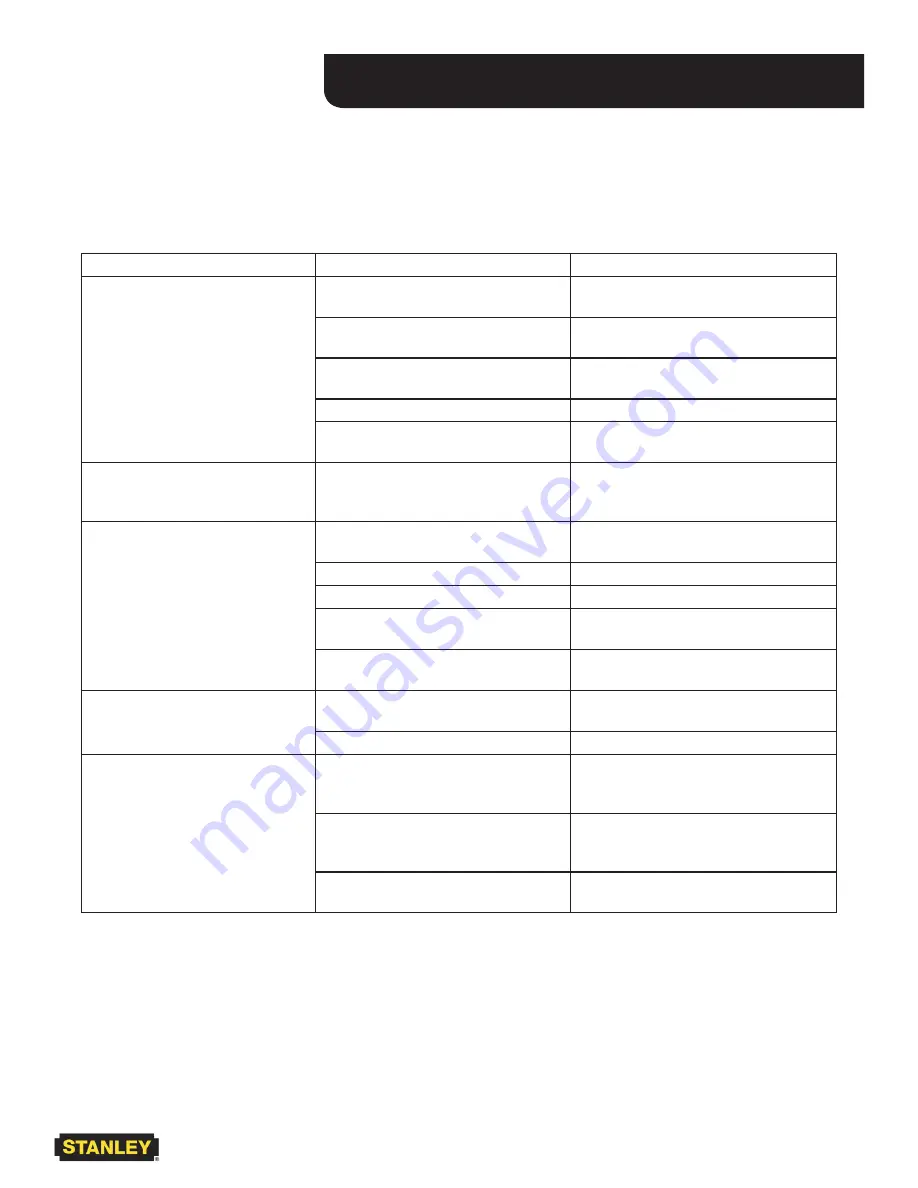
CT04 User
Manual ◄ 15
TROUBLESHOOTING
If symptoms of poor performance develop, the following chart can be used as a guide to correct the problem.
When diagnosing faults in operation of the grinder, always check that the hydraulic power source is supplying the
correct hydraulic flow and pressure to the grinder as listed in the table. Use a flowmeter known to be accurate.
Check the flow with the hydraulic oil temperature at least 80°F/27°C.
PROBLEM
CAUSE
SOLUTION
Tool does not operate.
Hydraulic hoses not connected
properly.
Make sure hoses are connected and
the couplers are tight.
Hydraulic control valve OFF.
Turn the hydraulic system control
valve ON.
Hydraulic system not functioning.
Check hydraulic power unit for correct
flow and pressure.
Couplers or hoses blocked.
Remove obstruction.
Pressure port check valve is
installed in tool return port.
Install pressure port check valve in
pressure port.
Tool operates in reverse (piston
advances/retracts when trigger is
squeezed).
Hoses connected to wrong ports on
tool.
Connect input (supply) line to IN port.
Connect output (return) line to OUT
port.
Tool under-crimps. Die load less
than 4.4 tons/4000 kg.
Hydraulic system pressure too low.
Check hydraulic power source for
correct flow and pressure.
Relief valve set too low.
Increase relief valve pressure.
Dirt or obstruction between dies.
Remove obstruction. Clean die area.
Piston seal worn or damaged.
Contact an authorized Stanley
distributor.
Improper die set for wire and
connector.
Install proper die set.
Tool over-crimps. Die load more
than 5 tons/4540 kg.
Hydraulic system pressure too high. Check hydraulic power source for
correct flow and pressure.
Relief valve set too high.
Decrease relief valve pressure.
Trigger difficult to operate.
Hoses connected to wrong ports on
tool.
Connect input (supply) line to IN port.
Connect output (return) line to OUT
port.
Excessive back-pressure.
If back-pressure is greater than
250 psi/17 bar, clear the return line
obstruction or restriction.
Trigger guard bent and binding on
spool in bore.
Repair or replace trigger assembly.