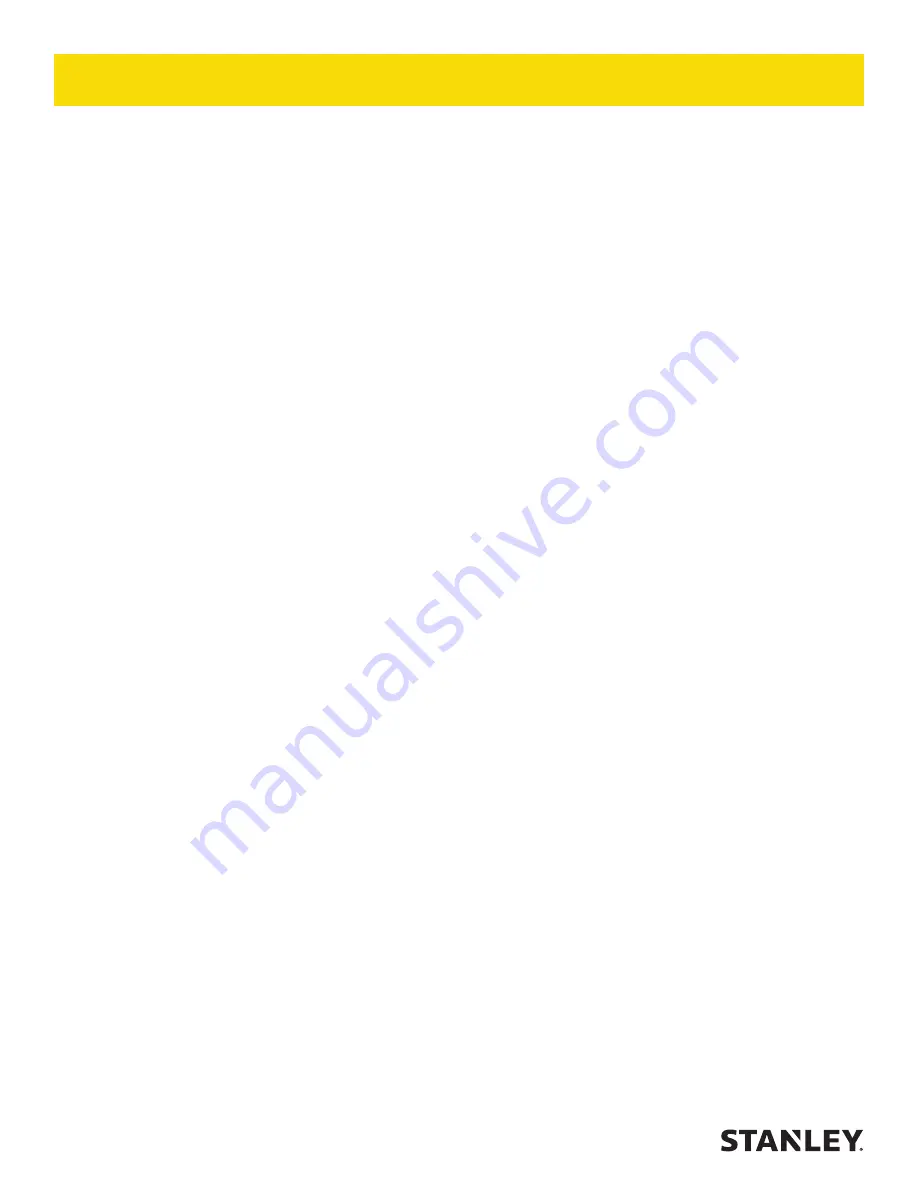
12 ► CO23
User Manual
TOOL OPERATION
Note: At the beginning of each shift or when a
new cutoff wheel has been installed, run the saw
at operating speed for at least one minute before
starting work. Keep personnel from in front of or in
line with the wheel.
GENERAL PROCEDURES
1. Whenever possible, the work should be held down
and securely supported on both sides of the cut.
2. Press down the safety catch; then slowly squeeze
the trigger. Start the cut with the wheel rotating. Start
the work gently, do not “bump” the work.
3. Feed the wheel through the material as fast as
possible without allowing the wheel to reduce its
speed. Cutting through the material too slowly
allows heat expansion and can cause wheel
“pinching” in the material. “Pinching” the wheel from
heat expansion is one of the most common causes
of wheel breakage.
CARE OF ABRASIVE CUTOFF WHEELS
All abrasive cutting-off wheels are breakable and,
therefore, care must be exercised during handling and
storage to prevent damage.
STORAGE
Thin, organic bonded wheels such as cutting off wheels
should be laid horizontally on a flat surface of steel
or similar rigid material away from excessive heat or
moisture. Wheels should not be stored where they will
be exposed to high humidity, water, other liquids, or
freezing temperatures. Temperatures low enough to
cause condensation on the wheels when moving them
from storage to an area of higher temperatures should
be avoided.
When used on cutoff saws carried on emergency
vehicles, wheels should be removed after use and
discarded or carefully stored as described in this section.
If wheels are supplied with blotters attached, suitable
separators should be used to preserve flatness.
INVESTIGATION OF WHEEL BREAKAGE
Wheels designed for use with hand-held portable saws
are specifically manufactured for this application. They
are manufactured to be extremely tough and are difficult
to break under normal use.
If a wheel breaks during use, a careful investigation
should be conducted by the user to determine the cause
of the breakage. The cause must then be corrected as
soon as possible.
If the user is unable to determine the cause of breakage,
the wheel manufacturer should be consulted.
COLD WEATHER OPERATION
If the saw is to be used during cold weather, preheat
the hydraulic oil at low engine speed. When using the
normally recommended oils, oil should be at or above
50 °F/10 °C (400 ssu/82 centistokes) before use.
Damage to the hydraulic system or saw can result from
use with oil that is too viscous or thick.
UNDERWATER MODEL PREVENTATIVE
MAINTENANCE
After each use, the movable portions of the tool that
were exposed to water should be flushed with a water
displacing oil, such as WD-40™. Remove any remaining
water and debris as follows:
1.
Spray oil into the On/Off valve trigger slot area.
2. Dip or spray the entire tool.
3. Cycle the tool hydraulically several times before
storing away.
OPERATION