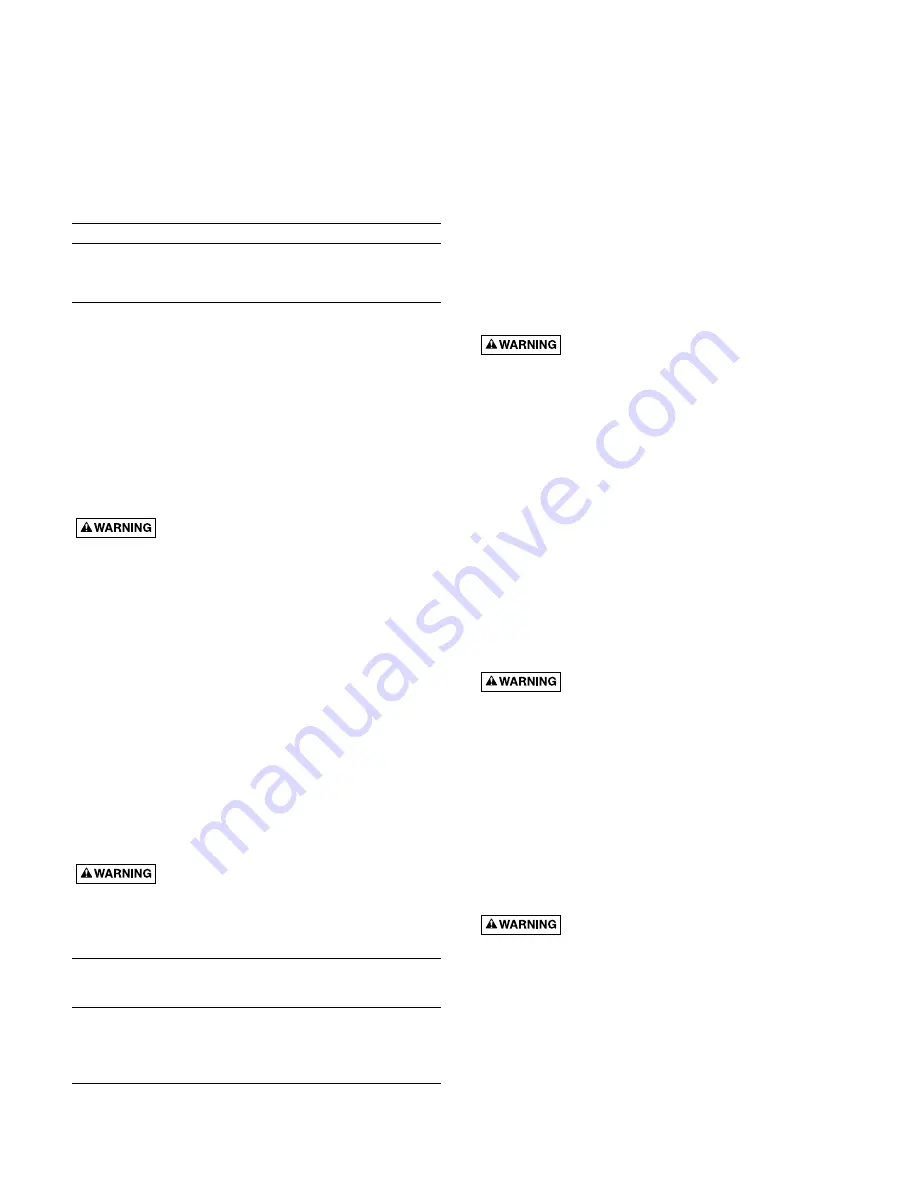
Piping
Piping must not be smaller than pump discharge.
When installed in a sewage system, pipe must be capable of
handling semi-solids of at least 51 mm (2") diameter.
The rate of flow in the discharge pipe must keep any solids pre-
sent in suspension in the fluid. To meet minimum flow require-
ments of 61 cm/sec (2 feet per second) in discharge line, size
pipe as follows:
A Pipe Size Of:
Will Handle a Flow Rate Of:
51 mm (2”)
79.5 L/M (21 GPM)
63.5 mm (2-1/2”)
113.5 L/M (30 GPM)
76 mm (3”)
182 L/M (48 GPM)
Use a 51 mm (2") check valve in pump discharge to prevent
backflow of liquid into sump basin. The check valve should be a
free flow valve that will easily pass solids.
NOTICE:
For best performance of check valve when handling
solids, do not install it with discharge more than 45° above the
horizontal. Do not install check valve in a vertical position as
solids may settle in valve and prevent opening on startup.
Drill a 5 mm (3/16") hole in discharge pipe about 25-50 mm
(1–2") above pump discharge connection (but below check
valve) to prevent airlocking the pump.
Electrical
Hazardous voltage. Can shock, burn, or
cause death
.
When installing, operating, or servicing this
pump, follow safety instructions below.
1.
DO NOT
splice the power cord, submerge electrical cord
plug, or use extension cords.
2.
DO NOT
handle or service pump while it is connected to
power supply.
3.
DO NOT
remove grounding prong from plug or modify
plug. Power cord on 1-phase units is a 3-wire conductor with
a 3-prong grounded plug. Plug pump into a 3-wire, ground-
ed, grounding-type receptacle. If there is no 3-wire grounded
receptacle to plug into, remove plug completely and wire
pump directly into terminal block in automatic float or
duplex controller box. Connect pump according to all applic-
able codes.
For automatic operation, plug or wire pump into an automatic
float switch or duplex controller. For continuous operation, plug
directly into an electrical outlet or wire directly into switch box.
Connect pump to its own circuit with nothing else on the cir-
cuit. See chart below for fuse or circuit breaker sizes.
Risk of electrical shock and fire. Be sure
that power supply information (Voltage/Hertz/Phase)
on pump motor nameplate matches incoming power
supply exactly. Install pump according to all electrical
codes that apply.
Dual Element
Voltage/
Time Delay
H.P.
Phase
Fuse Amps*
1/2
220/1
10
3/4
220/1 10
3/4
115/1
15
3/4
230/1
10
* Use time delay fuses or CBs in motor circuit. Do not use standard
fuses or CBs.
Operation and Installation
NOTICE:
Do not allow pump to run in a dry sump. It will void
the warranty and may damage the pump.
An automatic overload protector in the motor will protect motor
from burning out due to overheating/overloading. When motor
cools down, protector will automatically reset and start motor.
If overload trips frequently, check for cause. It could be a stuck
impeller, wrong/low voltage, or electrical failure in motor. If an
electrical failure in the motor is suspected, have it serviced by a
competent repairman.
Pump is permanently lubricated. No oiling or greasing is
required in normal service.
SERVICE
General
Hazardous voltage. Can shock, burn, or
cause death.
Before servicing pump, disconnect electrical
power to pump and control switch.
After removing basin cover and necessary discharge piping, lift
pump out of basin.
Place pump in an area where it can be cleaned thoroughly.
Remove all scale and deposits on pump.
Submerge pump in disinfectant (chlorox or chlorine) for at least
one hour before disassembling pump.
The pump motor housing contains a special lubricating oil.
Keep oil clean and free of water at all times.
NOTICE:
Whenever motor housing is being removed for ser-
vice, remove oil and replace with new oil at reassembly. Use
only oil listed in parts list (Part No. U197-8A). When filling
with new oil, DO NOT overfill. To allow room for expansion,
oil level with cold motor should be about 6 mm (1/4") above top
of motor assembly.
Impeller, Seal, and Capacitor Replacement
Risk of electrical shock. Disconnect elec-
trical power from pump before doing any service work
on it!
Numbers refer to assembly drawing, Page 3.
Disassembly
1. Remove motor assembly from volute and set it on its side in
a clean area.
2. Hold impeller (Key No. 10); remove impeller nut and wash-
ers (Key Nos. 11 and 12).
3. Unscrew impeller (turn counter-clockwise) for cleaning.
4. Remove oil fill plug (Key No. 2). Turn pump upside down
to drain oil.
Risk of electric shock. Before touching
capacitor, discharge it by shorting the terminals
together with an amber handled screwdriver.
5. Loosen cord nut and grommet (Key Nos. 20 and 19) to allow
cord to slide. Remove 4 socket head cap screws (Key No.
17) from seal plate and remove motor cover (Key No. 5).
6. If replacing capacitor, remove wires from capacitor (Key
No. 3A). Remove capacitor.
7. Remove rotating half of seal off of shaft.
8. Cradle motor assembly so that it stands vertically with
motor shaft extending out of the bottom.
2