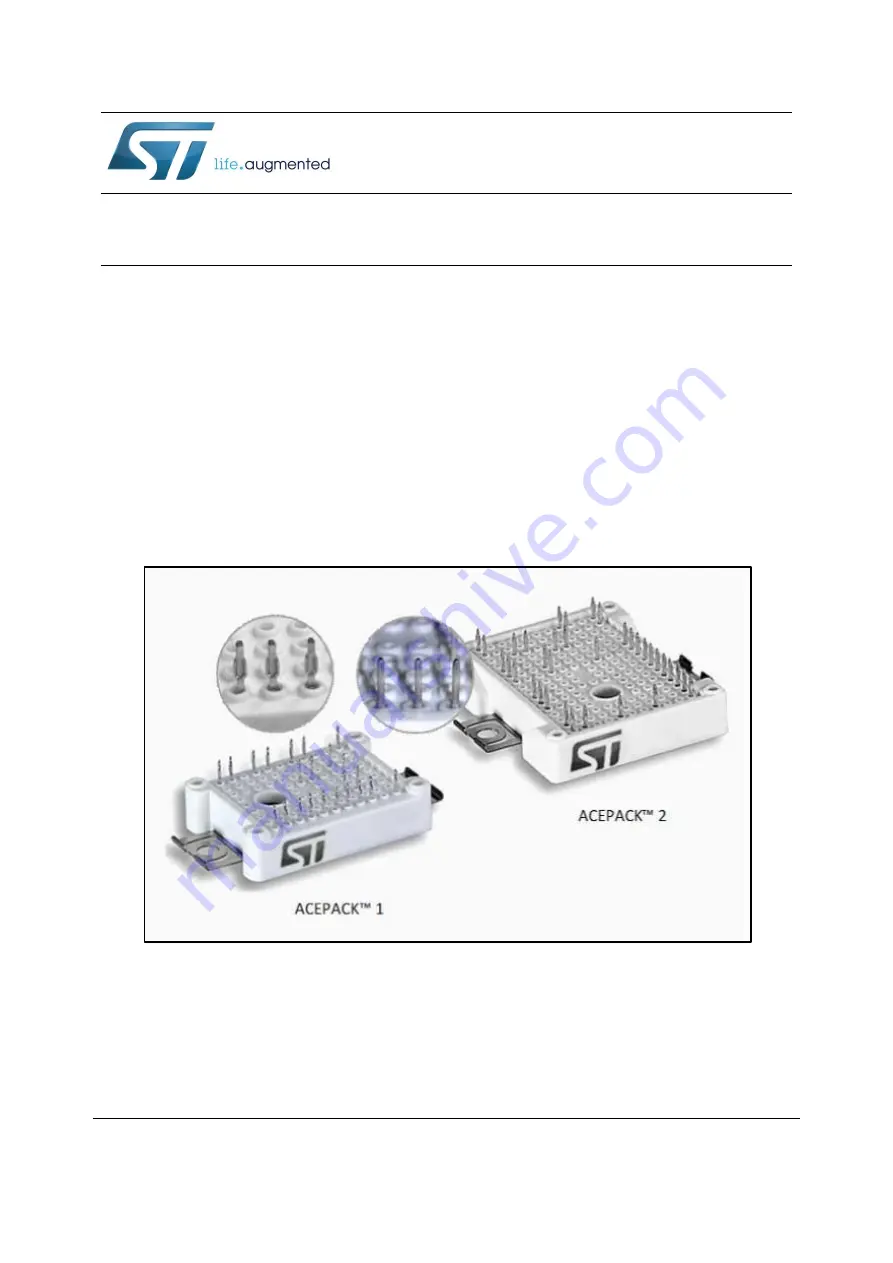
November 2017
DocID030935 Rev 1
1/16
www.st.com
TN1250
Technical note
Press-
fit ACEPACK™ power modules mounting instructions
Introduction
ST introduces the ACEPACK™ Power Module family, designed for easy mounting and reliable
performance in rugged applications. The available module form facto
rs are ACEPACK™ 1 with 33.8 mm
x 48
mm and ACEPACK™ 2 with 56.7 mm x 48 mm body dimensions. Various die selections in silicon
and silicon carbide substrates can be housed in several configurations.
These modules feature a compact, fully isolated, low profile housing able to integrate very high power
density components in a low junction-to-case thermal resistance DBC. Power modules simplify the
design and increase reliability, while PCB size and system costs are optimized.
The following sections provide recommendations for the connection of these modules to a printed circuit
board (PCB) and mounting and dismounting methods to achieve adequate connections, reliability and
performance in typical applications.
Figure 1
: ACEPACK™ 1 and ACEPACK™ 2