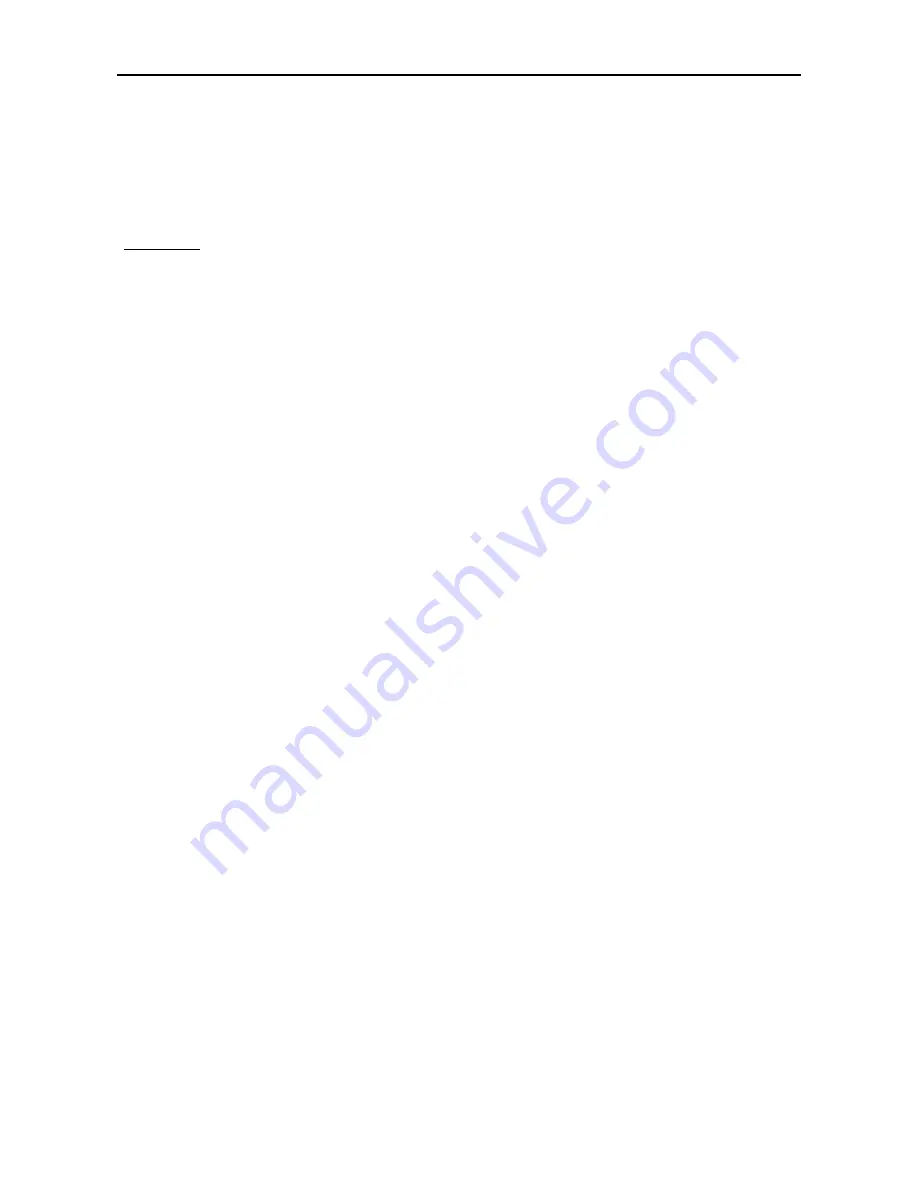
Operating Instructions Continued
© SPX FLOW, Inc.
13
Form No. 1000996
Rev. 0 Oct. 3, 2016
WARNING: Before bolt torquing, verify that:
The procedure and data to be used is authorized by a responsible engineer.
The joints/pipework being worked on are not live. Joints must be at zero pressure
and free from hazardous substances.
The torque value selected must be based upon the lubricant applied.
Procedure
1. Working in a crisscross pattern, number each bolt in order of torque sequence.
2. Square up the flanged joint using hydraulic torque wrenches, if necessary.
3. Set the pump at its lowest possible output, 103 bar (1,500 psi), and following the numbers on
the bolts, apply the minimum torque to the bolts.
4. In the same tightening sequence, apply approximately 25% of the torque value specified in the
torque data.
5. In the same tightening sequence, apply approximately 50% of the torque value specified in the
torque data.
6. In the same tightening sequence, apply the full torque value specified in the torque data.
7. Working in a clockwise (or counter-clockwise) direction, make a final pass around the flange,
tightening each bolt to the full torque value specified in the torque data.
8.
Using a hammer, “ring” each nut to verify that each bolt has been correctly loaded and that no
slack bolts remain.
Loosening Bolts
Loosening bolts using hydraulic torque wrenches can be unpredictable and often unsuccessful,
especially if the nuts and bolts are severely corroded. However, some measures can be carried
out to increase the success rate of nut breakout:
In general, loosening mildly rusted bolts requires up to twice the makeup torque to release
the nut. Heavily corroded bolts may take up to three times the makeup torque. Verify that
the bolt and nut material is strong enough to accept these higher torques.
Remove surface rust and scale using a wire brush. Apply releasing oil to the nut, bolt, and
bearing face, and allow time for the release oil to soak in and penetrate.
Only use the hydraulic torque wrench to break the nut free. Using the torque tool to wind
the nut from the bolt can induce high torsion and reaction forces. Therefore, it is better to
use an impact wrench to completely remove the nut.
Never strike the torque wrench or nut/bolt in an attempt to 'shock' the nut free. This can
cause damage to the hydraulic torque wrench and operator injury. Evidence of torque
wrench abuse will void the Manufacturer's Warranty.
NOTE: Should maximum pump pressure be reached, and the nut has not broken
free, use a higher capacity hydraulic torque wrench (if the nut/bolt material will
accept the higher torques without damage). Do not, under any circumstances,
strike the hydraulic torque wrench or nut/bolt in an attempt to 'shock' the nut free.