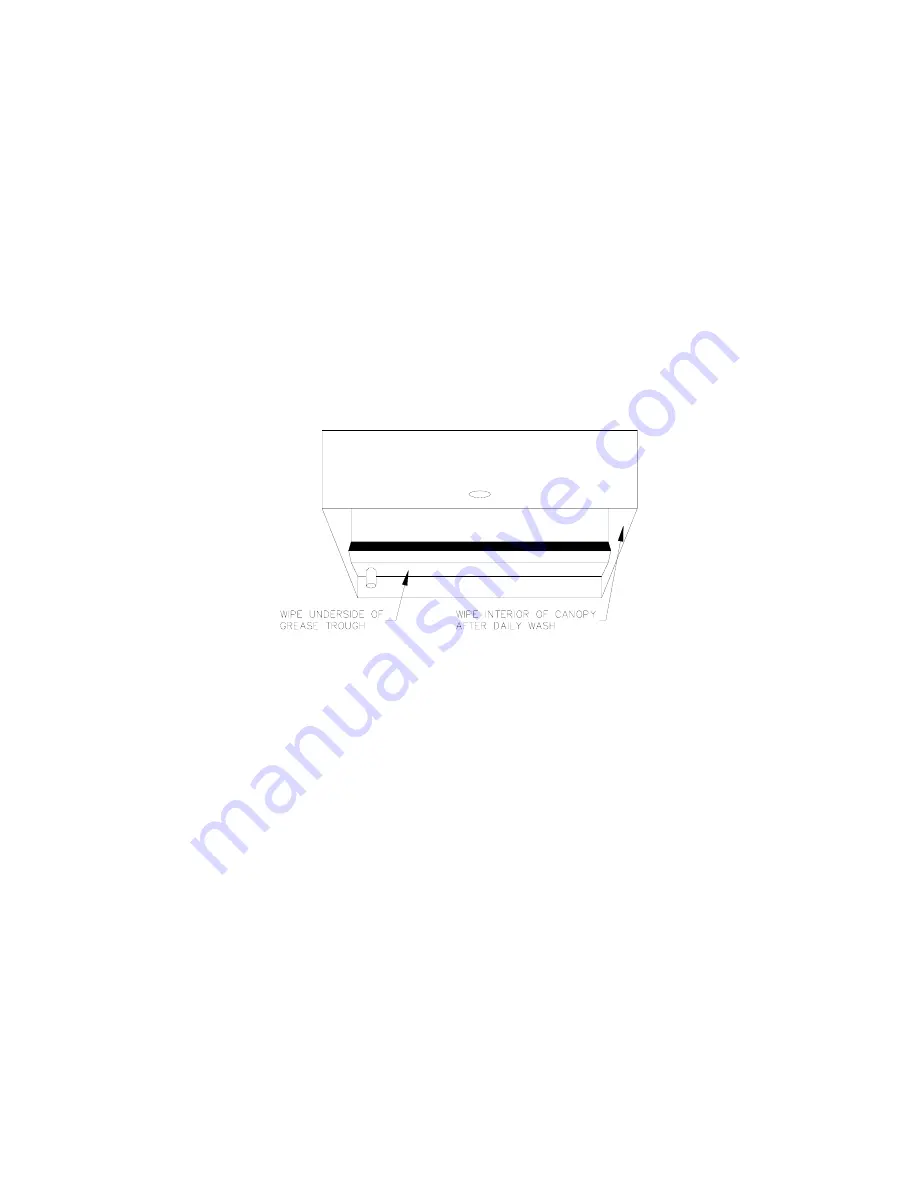
DN-Rev-LOW Maintenance and Operating
Manual
6
CLEANING THE EXTERIOR
Normal soil can be removed with a mild detergent and water mixture applied to a cloth. To
remove baked on grease, apply a cleanser to a damp cloth or sponge and rub on the metal in the
direction of the polishing lines. DO NOT RUB IN A CIRCULAR MOTION.
Burnt deposits, which do not respond, can usually be removed by rubbing the surface with a
SCOTCH-BRITE scouring pad of STAINLESS scouring pads. DO NOT USE ORDINARY STEEL
WOOL. Heat tint can be removed by a vigorous scouring in the direction of the polish lines using
a SCOTCH BRITE of STAINLESS scouring pad in conjunction with a powdered cleanser.
REV-LOW
MAINTENANCE SCHEDULE
DAILY:
1.At the end of the cooking day wipe off the interior and exterior of the dry ventilator canopy
and the underside of the grease trough with damp clothe.
WEEKLY:
1.Remove the grease inserts and wash in a mild detergent and water mixture.
2.Cleaning the Hood Exterior
Cleaning the Hood Exterior
Figure 7
Wipe off the interior of the dry ventilator plenum behind the grease extractor inserts and the
interior and exterior of the grease trough. Remove the grease cup and clean if necessary.
SIX MONTHS
1.Check the exhaust fan belts for alignment, tighten, and wear. Adjust an/or replace.
2.Inspect the fusible link fire damper. Clean and/or replace the fusible link if necessary.
TROUBLE SHOOTING
Low air
(i)
Improper exhaust fan rotation.
(ii)
Broken or slipping belt.
(iii)
Exhaust ductwork inspection door open.
(iv)
Obstruction in the ductwork.
(iv)
Flow-flow baffle must be adjusted
No Air
(i)
Broken belt.
(ii)
Exhaust fan overload tripped.
(iii)
Exhaust fan disconnect open.
(iv)
Exhaust fan motor fuse blown.
(v)
Fire damper closed.
(v)
Check if baffles are upside down in extractor.