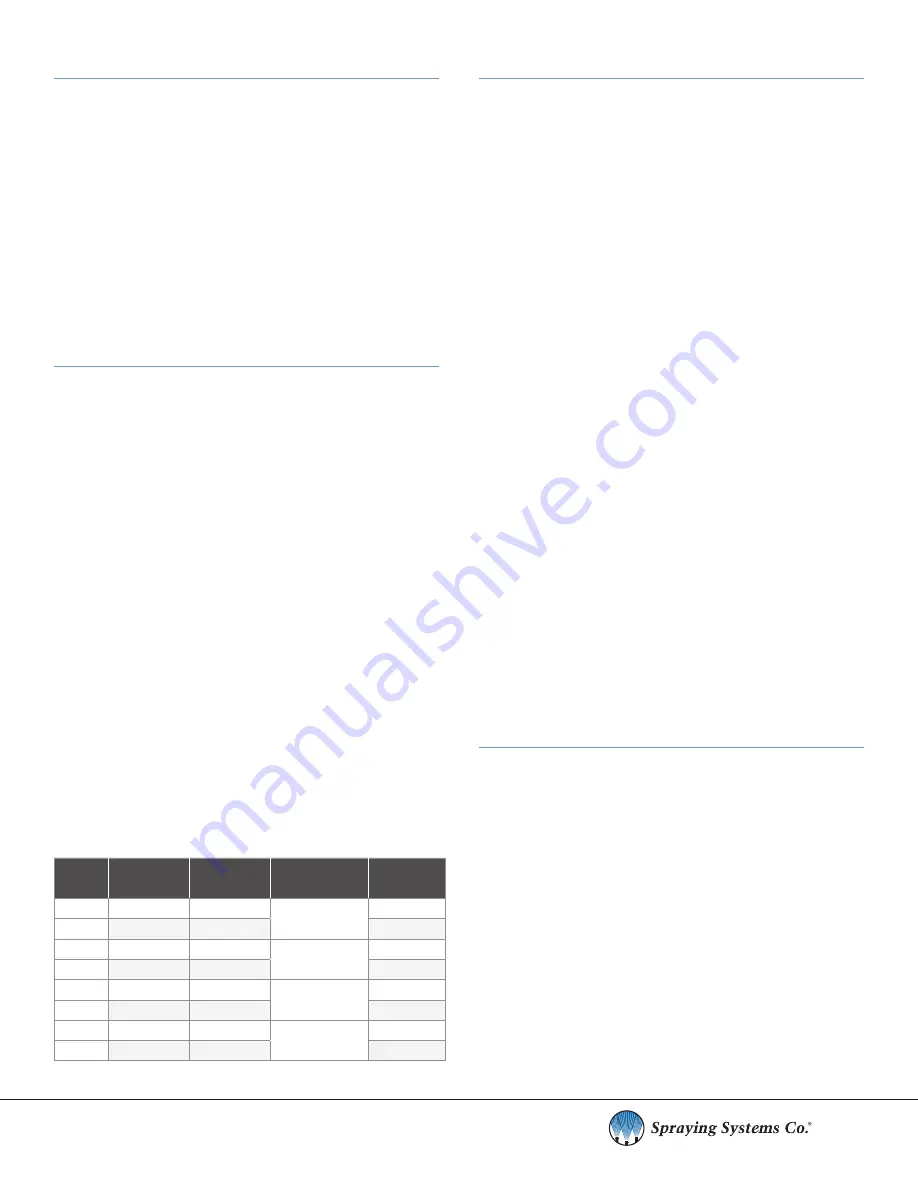
5
spray.com | 1.800.95.SPRAY | Intl. Tel: 1.630.665.5000
INSTALLATION
The TankJet
®
75 is easy to install as it has a single 3/4" female
pipe thread connection (NPT or BSPT) or 1" sanitary tri-clover
flange fitting. It may be installed on a tripod, a manhole cover,
or suspended from a pipe. In all installations position TankJet
75 vertically upright or upside down and a suitable (200 mesh)
strainer should be used to prevent dirt or scale from clogging the
waterways or openings.
WARNING:
In closed tanks, provisions should be made for
adequate venting during operation to allow the escape of
any gases or volatile vapors which may be produced during
operation.
OPERATION
To start the unit, turn on the fluid. An in-line valve is required for
a slow build-up of liquid pressure in the unit to prevent “water
hammer”. To stop the unit, turn off the liquid. The unit should
always be handled carefully. If the unit is dropped or maltreated
it may cause internal damage to the drive pod assembly, which in
turn can affect the performance of the unit.
OPERATION & SPECIFICATION
Refer to drawing 75-2, 75-4 and 75H models for assembly and
parts list.
Inlet Connection:
3/4" Female NPT or BSPT or
1" sanitary tri-clover flange
Operating Pressure Range:
75-300 psi (5.2-20.7 bar)
(Based on Models)
Max . Operating Temp:
250° F (121° C)
Flow Capacity:
15 to 33 gpm (57 to 125 lpm)
(Based on Models)
Head Rotation Speed:
7 to 17 rpm
Effective Cleaning Dia .:
To 30 ft. maximum (9.1 m)
Recommended Strainer:
200 mesh (80 micron)
(not included)
Approximate Weight and Dimensions:
TROUBLESHOOTING
Due to the simplicity of the unit, very few problems should occur.
If any trouble should arise, the following steps may be taken:
Refer to the Parts List.
A . Check unit for external damage, look for evidence of
mishandling that may have damaged shafts, bearings,
or alignment .
B . If the nozzle body fails to rotate and no liquid passes:
1. Check for liquid pressure and volume at the unit.
2. Check strainer for filter blockage.
3. Remove nozzles and check for obstructions.
4. While nozzles are off, recheck for flow through
the nozzle body.
C . If the unit fails to rotate and sufficient liquid passes:
1. Check for freedom of rotation, by hand, in the vertical and
rotational axis.
2. If the unit is free, insert a solid motor bypass plug. The
motor bypass plug port is located in the top center of the
motor. The purpose of the plug is to divert the pressurized
fluid to the side drive holes of the motor, thus providing
more driving power to overcome any frictional build-up
that may occur after extended use. If the unit still does not
rotate, check for:
a. Contamination in the unit.
b. Wear of any one of the following parts:
the bushings, washers, and the rotor.
c. Galling and straightness of the shafts.
D . Replace all defective parts .
WARRANTY
For newly purchased units the warranty is 18 months from the
date of shipment or 12 months from the date of installation,
whichever occurs first. This warranty includes manufacturing
defects but does not cover the wear parts that include the
bushings. This warranty will be void if parts other than those
supplied by Spraying System Co. are used.
Model
Inlet
Conn.
Overall Length
in. (mm)
Min. Tank Opening
in. (mm)
Net Weight
lbs. (kg)
75-2
Threaded
6 .13 (156)
3 .0 (76)
2 .6 (1 .2)
75SF-2
Sanitary Flange
7 .13 (181)
2 .9 (1 .3)
75H-2
Threaded
6 .25 (159)
3 .0 (76)
2 .6 (1 .2)
75HSF-2
Sanitary Flange
7 .25 (184)
2 .9 (1 .3)
75-4
Threaded
6 .13 (156)
4 .2 (107)
3 .0 (1 .4)
75SF-4
Sanitary Flange
7 .13 (181)
3 .3 (1 .5)
75H-4
Threaded
6 .25 (159)
4 .2 (107)
3 .0 (1 .4)
75HSF-4
Sanitary Flange
7 .25 (184)
3 .3 (1 .5)