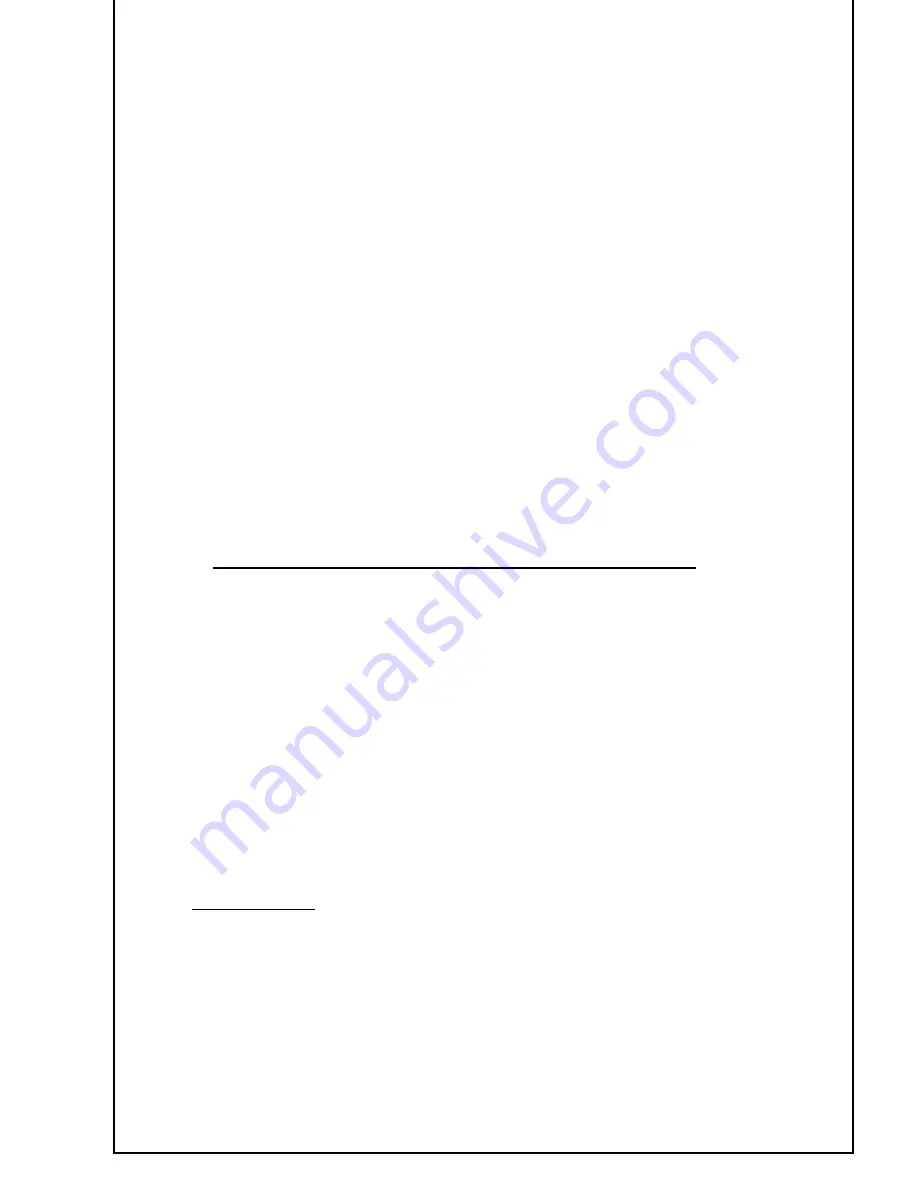
12
Maintenance
Only proper maintenance can ensure constant performance, reduction in wear and thus,
a decrease in operating costs and an increase in service life.
AIR BAND SAW
SERVICE LIFE
and
PERFORMANCE
of the Air band saw are determined by
a) Degree of air purity
Blow the air hose clear before connecting it to the saw.
Install dirt and water separators upstream of the saw, if it is not possible
to prevent the formation of rust and water condensation in the air distribution lines.
b) Lubrication
The motor must be lubricated by a line oiler or service unit.
Fill the lubricator with resin- and acid-free „SAE 5 W“ to „SAE 10 W“ oil.
Heavy oils will cause the vanes to stick, thereby making the motor difficult to start
and impairing its performance.
Optimum lubrication significantly prolongs service life. We therefore
highly recommend to install service units (combined filters, regulators and
lubricators) upstream of the saw.
c) Maintenance
Regularly check and clean the air inlet screen.
Replace wear parts - in particular the motor vanes - when necessary.
Vanes are considerd worn if their width is less than 9.7 mm (3/8“)
ELECTRIC BAND SAW:
For your continued safety and electrical protection, brush inspection and replacement
on this tool should ONLY be performed by an Authorized CS Unitec Service Station.
At approximately 100 hours of use, take or send your tool to your nearest authorized
CS Unitec Service Station to be thoroughly cleaned and inspected. Have worn parts
replaced and lubricate with fresh lubricant. Have new brushes installed, and test the
tool for performance.
Any loss of power before the above maintence check may indicate the need for
immediate servicing of your tool. DO NOT CONTINUE TO OPERATE TOOL
UNDER THIS CONDITION. If proper operating voltage is present, return your tool
to the service station for immediate service.
Keep Tool Clean
Periodically blow out all air passages with compressed air.
Caution: Wear safety glasses while using compressed air.
Remove wax and chip buildup from drive pulleys and blade guides.
All plastic parts should be cleaned with soft damp cloth.
Never
use solvents
to clean plastic parts. They could possibly dissolve or otherwise damage the
material.
After use, clean the saw. Rinse it with light oil or provide alternate corrosion
protection after having worked in wet surroundings.