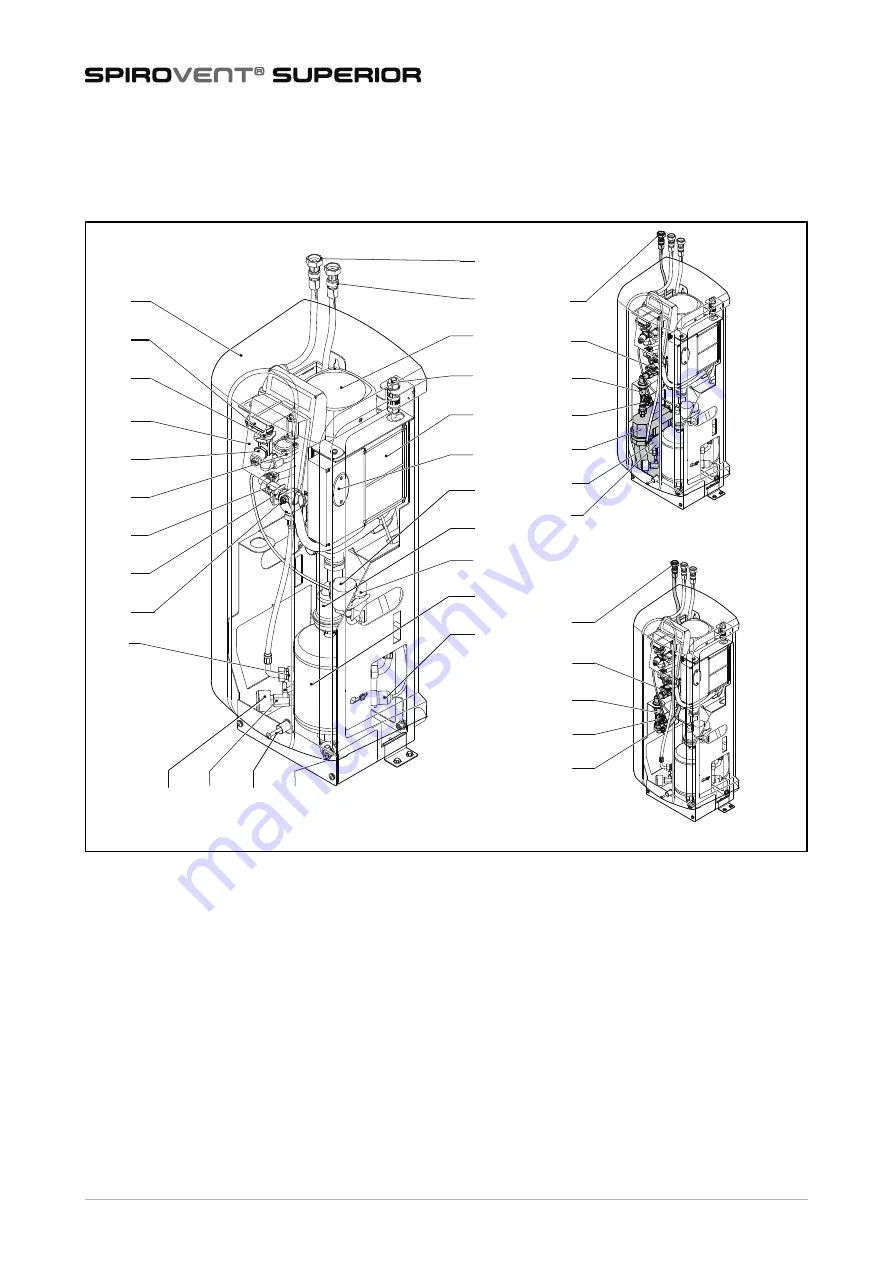
(QJOLVK
8VHUPDQXDO
2
INTRODUCTION
2.1
Overview of the unit
1
Outlet connection
2
Inlet connection
3
Pump
4
Power terminal
5
Control unit - Power box
6
Fuses
7
SmartSwitch
8
Automatic air vent
9
Check valve of the air vent
10
Deaeration vessel
11
Level sensor
12
Drain connection
13
Bolt
14
Valve behind the pressure gauge
15
Pressure gauge
16
Flow limiter bypass
17
Deaeration valve
18
Check valve of the outlet
19
Flow limiter outlet
20
Solenoid valve
21
Pressure sensor
22
Control unit (HMI)
23
Flow limiter inlet
24
Y-filter
25
Cover
26
Refill connection
27
Solenoid valve refill
28
Check valve refill
29
Water flow meter
30
Break tank
31
Float valve
32
Float switch
33
Flow limiter refill
S400-B
S400-R
S400
22
21
20
19
18
16
17
25
24
23
1
2
4
7
8
3
6
10
11
9
5
13
12
15
14
28
29
30
31
32
26
27
28
29
33
26
27