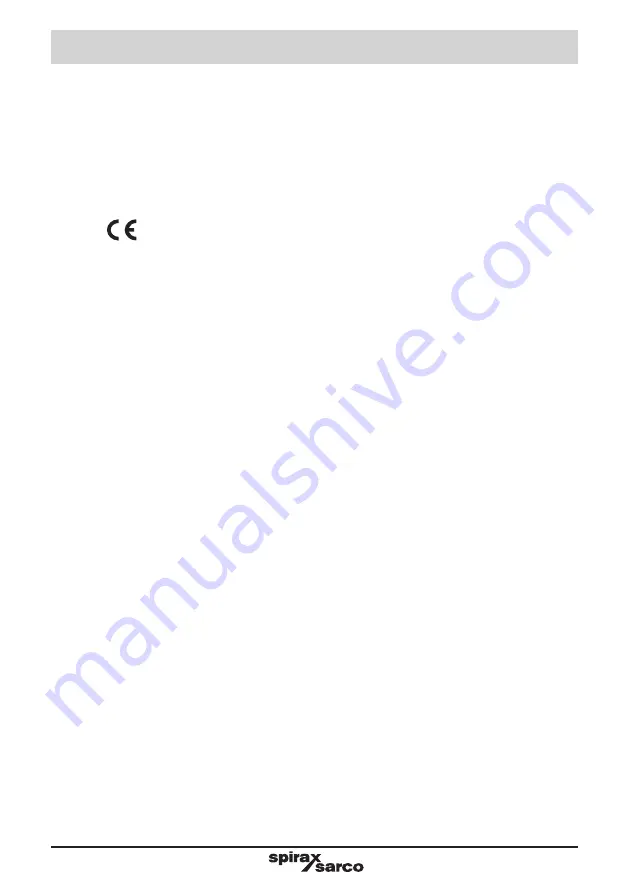
IM-P316-03
CTLS Issue 14
2
Safe operation of the unit can only be guaranteed if it is properly installed, commissioned and
maintained by a qualified person (see Section 1.11) in compliance with the operating instructions.
General installation and safety instructions for pipeline and plant construction, as well as the
proper use of tools and safety equipment must also be complied with.
1.1 Intended use
Referring to these Installation and Maintenance Instructions, Name-plate and Technical Information
Sheet, check that the product is suitable for the intended use/application. The requirements of the
Pressure Equipment Directive (PED) have been satisfied and, if applicable, the product accordingly
bears the
mark:
i) The product has been specifically designed for use on the fluids specified in the Technical
Information Sheets. (These fluids are in Group 2 of the above mentioned Pressure Equipment
Directive). The product’s use on other fluids may be possible but, if this is contemplated,
Spirax Sarco should be contacted to confirm the suitability of the product for the application
being considered.
ii) Check material suitability, pressure and temperature and their maximum and minimum values.
If the maximum operating limits of the product are lower than those of the system in which it
is being fitted, or if malfunction of the product could result in a dangerous overpressure or
overtemperature occurance, ensure a safety device is included in the system to prevent such
over-limit situations.
iii) Determine the correct installation situation and direction of fluid flow.
iv) Spirax Sarco products are not intended to withstand external stresses that may be induced
by any system to which they are fitted. It is the responsibility of the installer to consider these
stresses and take adequate precautions to minimise them.
v) Remove protective covers from all connections and protective film from all name-plates, where
appropriate, before installation on steam or other high temperature applications.
1.2 Access
Ensure safe access and if necessary a safe working platform (suitably guarded) before attempting
to work on the product. Arrange suitable lifting gear if required.
1.3 Lighting
Ensure adequate lighting, particularly where detailed or intricate work is required.
1.4 Hazardous liquids or gases in the pipeline
Consider what is in the pipeline or what may have been in the pipeline at some previous time.
Consider; flammable materials, substances hazardous to health, extremes of temperature.
1.5 Hazardous environment around the product
Consider; explosion risk areas, lack of oxygen (e.g. tanks, pits), dangerous gases, extremes of
temperature, hot surfaces, fire hazard (e.g. during welding), excessive noise, moving machinery.
1. Safety information
Summary of Contents for SV615
Page 19: ...IM P316 03 CTLS Issue 14 19...
Page 20: ...IM P316 03 CTLS Issue 14 20...