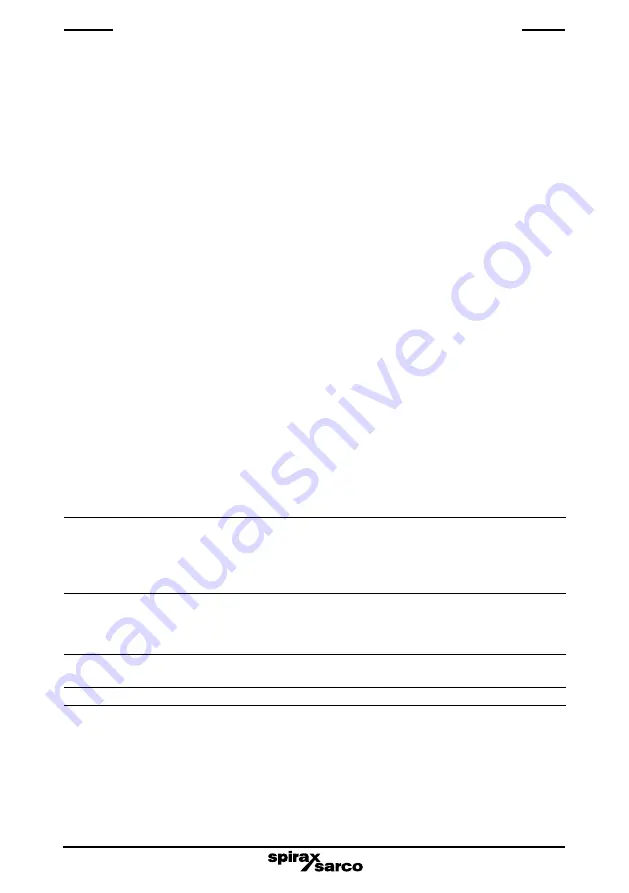
IM-P128-23
ST Issue 6
6
2.1 Description
The STS17.2 compact pipeline connector steam trapping station has been designed to provide
a convenient ready to install trapping solution, which includes: upstream and downstream
isolation valves (
2
), body incorporating quickfit con strainer (
1
) and check valve (
16
).
Available types
The STS17.2 is available with either single or double upstream isolation.
The STS17.2 trapping solution incorporates Spirax Sarco quickfit technology, which allows
speedy trap maintenance. The following swivel connector steam traps (sold separately) can
be used with this pipeline connector enabling it to be tailored to suit any application:
-
UTD30
and
UTD52
thermodynamic steam traps.
-
UBP32
balanced pressure steam trap.
-
USM
bimetallic steam trap.
-
UFT32
ball float steam trap.
-
UIB30
and
UIB30H
inverted bucket steam traps.
Standards
These products fully comply with the requirements of the European Pressure Equipment
Directive 97 / 23 / EC.
Certification
These products are available with certification to EN 10204 3.1.
Note:
All certification /
inspection requirements must be stated at the time of order placement. For other certification
contact Spirax Sarco.
Note:
For additional product information see Technical Information Sheet TI-P128-22.
Optional extras
Integral sensor type SSL1
(steam only)
or WLSL1
(for waterlogging) for use with R1C
or WLSL1 with DIODE
for use with RI6C are available as optional extras, to enable
operational monitoring of the steam trap.
Please note
that the optional Spiratec
SSL1
and
WLSL1
sensors
must not be fitted when the STS17.2 is installed in a vertical application
.
However a sensor can be fitted to a UTD30 steam trap if fitted.
BDV1 blowdown valve
is also available for cleaning the strainer during operation.
Care should be taken when using the BDV1 blowdown valve as the discharge may be hot.
Please note that a BDV1 cannot be used when a Spiratec sensor has been chosen to be
part of the unit.
Retrofit double isolation valve and spool piece
to convert a single upstream isolation
version to double isolation.
Insulation jacket
is available to reduce heat loss and energy wastage. See separate literature.
2.2 Sizes and pipe connections
½
",
¾
" and 1" screwed BSP, NPT or socket weld.
½
",
¾
" and 1" ASME 150 and ASME 300.
DN15, DN20 and DN25 flanged EN 1092 PN40.
2. General product information
Upstream isolation
valve
Summary of Contents for STS17.2
Page 2: ...IM P128 23 ST Issue 6 2 ...
Page 20: ...IM P128 23 ST Issue 6 20 ...