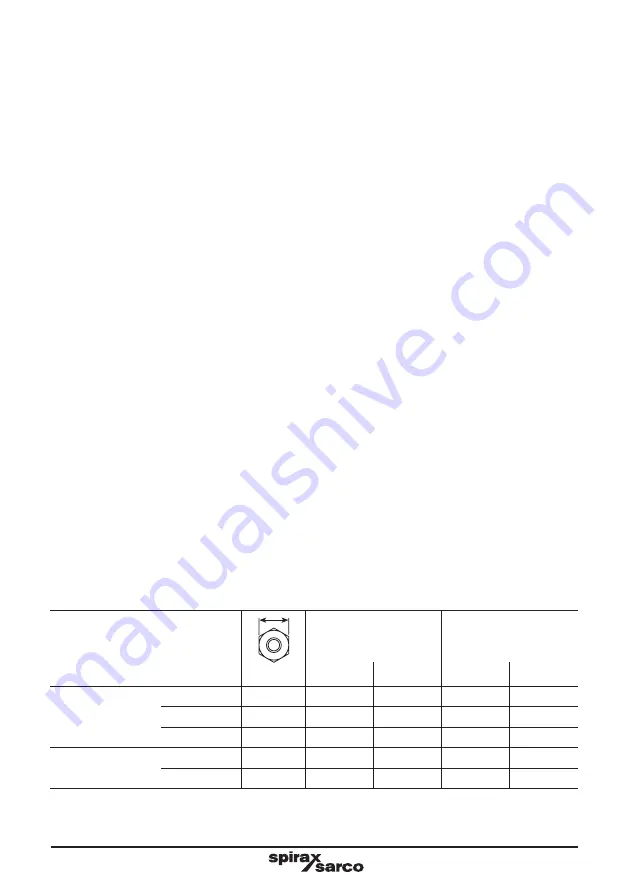
IM-P184-09
CMGT Issue 4
14
start of text under grey section header box
start of text continuing from previous page
TRANSLATION RUN OVER
6.6 How to fit the stem and bellows assembly
By following through Section 6.5 it is now possible to fit a new stem/bellows assembly (
6, 5
):
-
Fitting this is opposite to removal - remembering to fit a bellows collar gasket (
11a
) between the bellows
support collar and valve bonnet (
2
).
-
Ensure the bellows collar gasket (11a) is accurately located. Before fitting the new stem/bellows assembly
(
6 and 5
) into the bonnet (
2
).
-
Apply a small amount of lubricating compound such as Gulf Sovereign LC grease to the end of the stem
pin (which is pressed into the stem).
-
Ensure the stem pin is aligned with the slot inside the bonnet.
-
Carefully slide the stem up through the bonnet.
-
Before screwing the end of the stem into the bonnet bush remember to fit a new stem packing ring (
8
)
(see Section 6.5), the original gland washer (or gland follower) and gland nut (or gland flange) over the
stem (
6
). Do not allow the stem thread to damage the inner surface of the gland packing ring (
8
).
-
Carefully slide the new packing ring (
8
) down the stem into the cavity and slide the original gland washer
(or gland follower if fitted) on top of the packing ring (
8
).
-
After the valve has been fully assembled remember to create a safe seal between the gland packing
ring (
8
) and the stem (
6
) by tightening down the gland nut to the recommended tightening torque (see
Table 1).
6.7 How to fit the disc
By following through Section 6.5 it is now possible to replace the valve’s disc:
-
To replace the disc (
4
) simply remove the old stem pin and replace the disc (
4
).
-
Attach the new disc with the new stem pin (supplied). Where the disc (
4
) is attached using a retaining
nut and collet arrangement, simply prise the crimped skirt away from the retaining nut and unscrew.
Remove the collets remembering to save these and the retaining nut as they are not supplied as spares.
Fitting is the opposite to removal but ensure the collets and threads are lightly greased with lubricating
compound such as Molybdenum Sulphide.
-
If a new disc is being fitted then crimp the collet retaining nut securely across two corners by deforming
the disc’s thin metal skirt. If the original disc is being fitted then re-crimp using a fresh part of the skirt.
Table 1 Recommended tightening torques
Item
Size
PN40
ANSI 300
mm
N m
(lbf ft)
N m
(lbf ft)
Bonnet bolts and
nuts (9 & 10)
DN15 - DN25
17 A/F
35 - 40
(26 - 29)
50 - 55
(36 - 40)
DN40 - DN65
19 A/F
55 - 60
(40 - 44)
85 - 90
(63 - 66)
DN80 - DN100
24 A/F
130 - 140
(95 - 103)
190 - 200
(140 - 147)
Gland nut
DN15 - DN80
22 A/F
5 - 10
( 3.5 - 7)
5 - 10
( 3.5 - 7)
DN100
32 A/F
15 - 20
(10.5 - 14 )
15 - 20
(10.5 - 14)