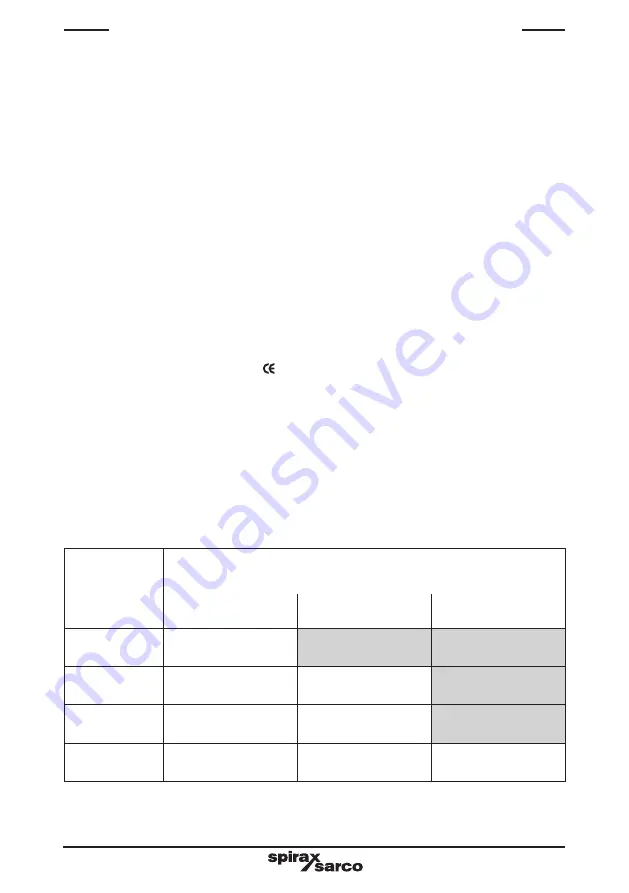
IM-P681-02
ST Issue 2
6
2. General product information
2.1 Description
The Spirax Sarco MFP14-PPU vented automatic pump packaged units are plug-in systems
specifically designed to collect and pump hot condensate; commonly returned for use as
boiler feedwater.
The MFP14-PPU is available with either single, duplex or triplex pumps, mounted on a single
base plate, that can be used for duty only or duty / stand-by applications.
Operated by steam, the MFP14-PPU can be tailored to suit a wide range of condensate
handling applications.
The standard pump is manufactured from SG iron, although cast steel and stainless steel
versions are available on request.
Please note:
Versions suitable for use with compressed air as the motive power and or other
combinations are available as bespoke items. For further details contact your local Spirax
Sarco office or representative.
Optional extras
A pump insulation jacket is available at extra cost - see TI-P136-07.
Standards
The MFP14-PPU fully complies with the requirements of the European Pressure Equipment
Directive 97 / 23 / EC and carries the mark when so required.
All welding is in accordance with the requirements of the European Pressure Equipment
Directive 97 / 23 / EC (PED).
Certification
This product is available with a declaration of conformity. For other certification requirements
contact Spirax Sarco.
Note:
All certification / inspection requirements must be stated at
the time of order placement. Retrospective certification / inspection may not be possible.
Note:
For additional product data see Technical Information sheet TI-P680-03.
2.2 Capacities
Unit size
Approximate maximum capacities kg / h (with 4M lift).
See separate TI sheet for full capacity details.
Single
MFP14-PPU
Duplex
MFP14-PPU
Triplex
MFP14-PPU
DN25
(1")
1 300
DN40
(1½")
2 000
4 000
DN50
(2")
4 000
8 000
DN80 x DN50
(3" x 2")
6 000
12 000
18 000
Summary of Contents for MFP14-PPU
Page 2: ...IM P681 02 ST Issue 2 2...
Page 20: ...IM P681 02 ST Issue 2 20...