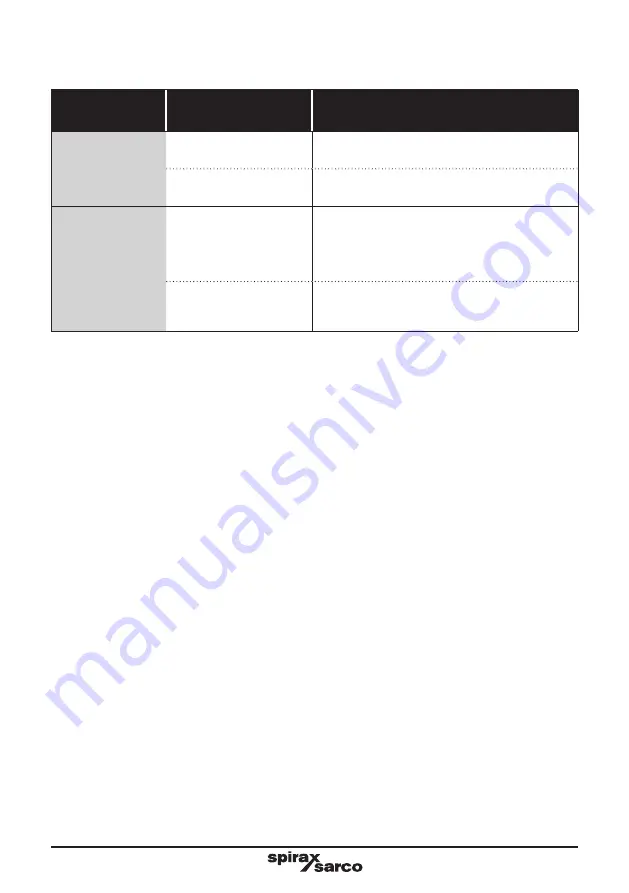
IM-P481-04
CTLS Issue 4
51
Fault
Possible cause
Remidial action
TVA flowmeter
does not power up
Field wiring fault
Check wiring of TVA to terminal X8
Loss of loop power
Check control fuse CF3
TVA input is not
showing correctly
Scaling value incorrect
Ensure that the minimum and maximum
engineering units from the TVA commissoining
match those on the HMI (this data is found on the
Spirax Sarco engineers 4-20 mA page)
Polarity of 4-20 mA
incorrect
Reverse polarity and wire as per electrical
drawings