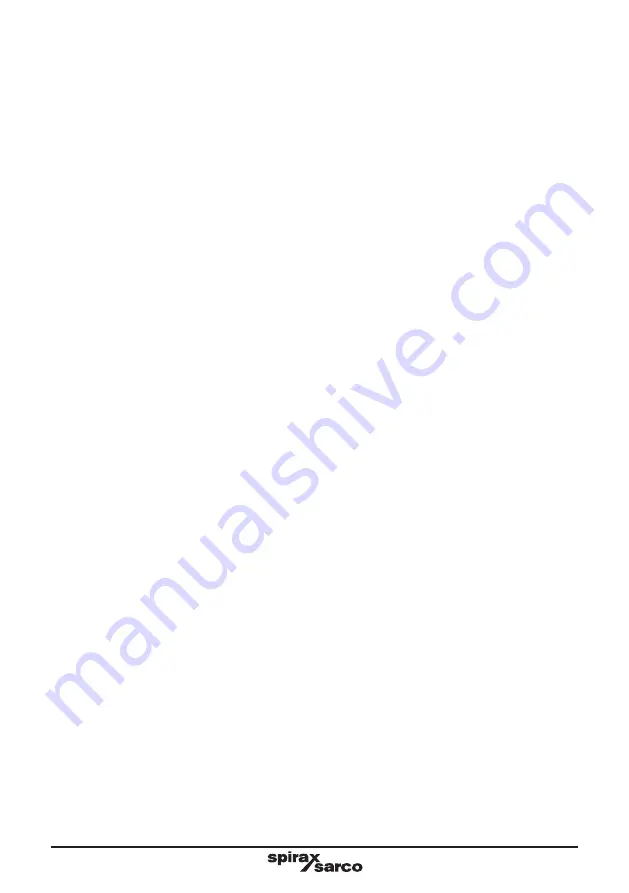
IM-P134-08
CMGT Issue 10
3
1.5 Hazardous environment around the product
Consider: explosion risk areas, lack of oxygen (e.g. tanks, pits), dangerous gases, extremes of
temperature, hot surfaces, fire hazard (e.g. during welding), excessive noise, moving machinery.
1.6 The system
Consider the effect on the complete system of the work proposed. Will any proposed action (e.g.
closing isolation valves, electrical isolation) put any other part of the system or any personnel at risk?
Dangers might include isolation of vents or protective devices or the rendering ineffective of
controls or alarms. Ensure isolation valves are turned on and off in a gradual way to avoid system
shocks.
1.7 Pressure systems
Ensure that any pressure is isolated and safely vented to atmospheric pressure. Consider double
isolation (double block and bleed) and the locking or labelling of closed valves. Do not assume
that the system has depressurised even when the pressure gauge indicates zero.
1.8 Temperature
Allow time for temperature to normalise after isolation to avoid danger of burns and consider
whether protective clothing (including safety glasses) are required.
Viton seat:
If the Viton seat has been subjected to a temperature approaching 315 °C (599 °F) or higher it may
have decomposed and formed hydrofluoric acid. Avoid skin contact and inhalation of any fumes
as the acid will cause deep skin burns and damage the respiratory system.
1.9 Tools and consumables
Before starting work ensure that you have suitable tools and/or consumables available. Use only
genuine Spirax Sarco replacement parts.
1.10 Protective clothing
Consider whether you and/or others in the vicinity require any protective clothing to protect against
the hazards of, for example, chemicals, high/low temperature, radiation, noise, falling objects, and
dangers to eyes and face.
1.11 Permits to work
All work must be carried out or be supervised by a suitably competent person.
Installation and operating personnel should be trained in the correct use of the product according
to the Installation and Maintenance Instructions.
Where a formal 'permit to work' system is in force it must be complied with. Where there is no such
system, it is recommended that a responsible person should know what work is going on and, where
necessary, arrange to have an assistant whose primary responsibility is safety.
Post 'warning notices' if necessary.
1.12 Handling
Manual handling of large and/or heavy products may present a risk of injury. Lifting, pushing,
pulling, carrying or supporting a load by bodily force can cause injury particularly to the back.
You are advised to assess the risks taking into account the task, the individual, the load and the
working environment and use the appropriate handling method depending on the circumstances
of the work being done.
Summary of Contents for DCV4
Page 12: ...IM P134 08 CMGT Issue 10 12...