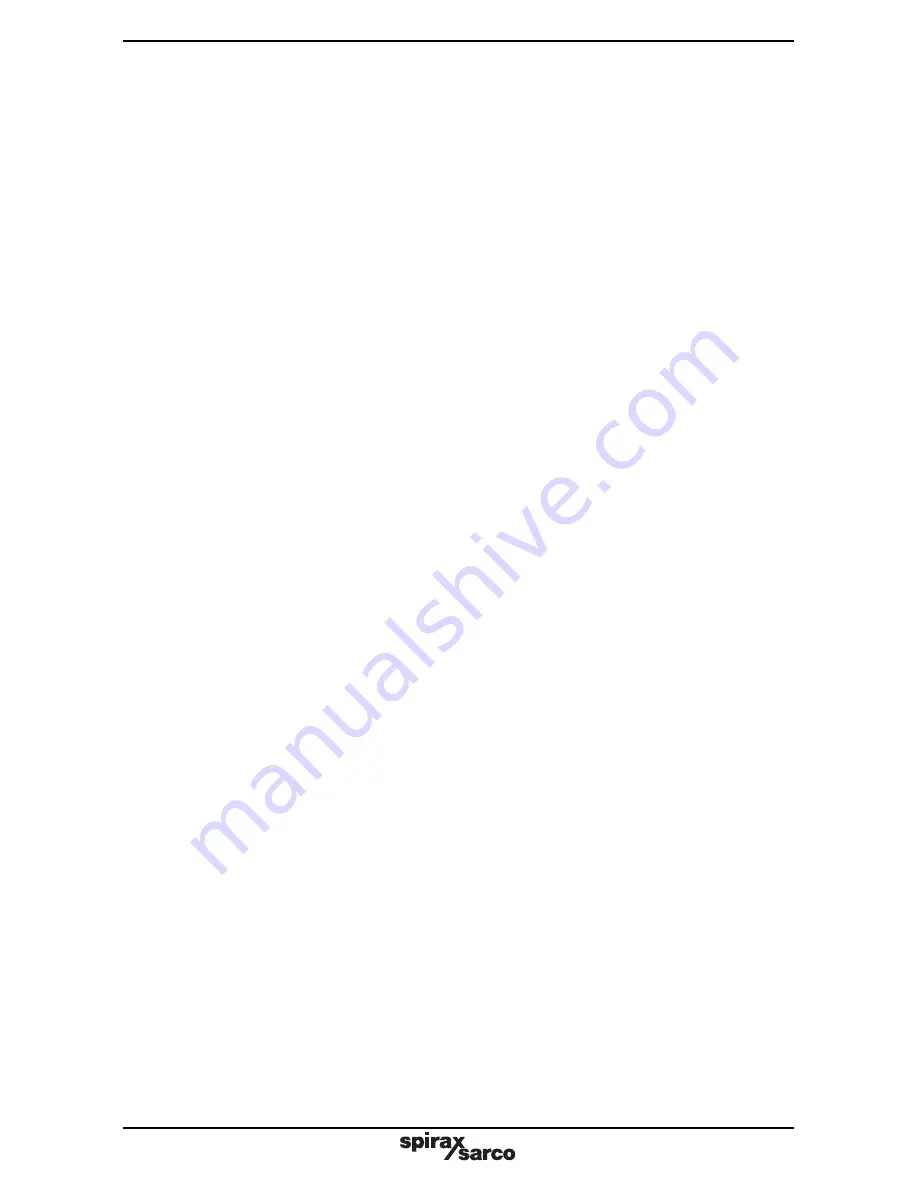
IM-P612-18 ST Issue 3
22
Please ensure the safety recommendations are observed before commencing with
any maintenance of this product.
Tools required
19 mm A / F socket, 13 mm A / F socket, Flat blade screw driver, Torque wrench, Long nose pliers
To replace the float and lever
1. Remove the cover and old gasket (see cover gasket replacement procedure, Section 7.1).
2. Lift the cover assembly to a bench or other convenient working surface and clamp securely,
avoiding contact with the gasket face.
3. Remove the split pin and washer from one side of the spring retaining shaft (Y) and carefully
remove. (See Fig. 20).
Note: It is extremely important this is done first to prevent over stressing the spring
during Step 4.
4. Remove the split pin and washer from one side of trap pivot retaining shaft (Z) and carefully
remove.
5. Carefully slide the shafts out from their respective positions observing the orientation of the
spring and actuator arm (item 14, 24) within the pump bracket (item 13) as these will need
to be refitted later.
6. Remove the split pin and washer from one side of pump pivot retaining shaft (X).
7. To remove shaft (X), the whole pump bracket (13) will need to be separated from the cover. This
can be done by unscrewing the three M8 retaining bolts, and removing the circlip from the
steam inlet valve (17). Remove the pump pivot retaining shaft (X).
8. The float and lever assembly can now be removed and discarded as the replacement float
and lever is supplied fully assembled in the spares kit.
9. Assembly is the opposite to removal. Always fit new split pins and washers.
10. It is easier to fit the replacement shafts in the following sequence:- (See Fig. 21).
X.
Pump pivot
(shaft length 52 mm)
Refit pump bracket (13) to cover and tighten the three M8 bolts using the 13 mm A/ F
socket to 18 ± 2 N m (13 ± 1.5 lbf ft). Refit the new circlip to the steam inlet valve.
Z.
Trap pivot
(shaft length 40 mm)
Y.
Spring retainer
(shaft length 30 mm)
leaving the spring retaining shaft until after the spring and actuator arm have been correctly
aligned and located within the slot of the pump bracket (item 13).
Ensure the tanged spigot of the actuator arm is correctly engaged with the exhaust valve.
11. When all the shafts have been secured using new split pins and washers, move the float to its
upper and lower limit to ensure the mechanism operates smoothly and the spring and actuator
arm snaps over to operate the motive steam inlet and exhaust valves (items 17, 18).
Note: The mechanism has been designed to be adjustment-free, simplifying the fitting of new
parts. If after assembly the mechanism does not operate correctly, check all the parts are
assembled and aligned as per the diagram.
12. With the mechanism fully assembled, refit the cover assembly to the body, ensuring the gasket
faces are carefully aligned and no parts of the gasket are trapped or pinched outside the
sealing areas.
7.4 Replacement of float
Summary of Contents for APT10-2
Page 2: ...IM P612 18 ST Issue 3 2...
Page 17: ...IM P612 18 ST Issue 3 17 Fig 15 2 Fig 16...
Page 19: ...IM P612 18 ST Issue 3 19 Fig 17 17 Circlip 12...
Page 21: ...IM P612 18 ST Issue 3 21 Fig 18 Fig 19 13 13 18 Spring retaining shaft Y 18 24...
Page 29: ...IM P612 18 ST Issue 3 29 Fig 25 13 Spring retaining shaft Y...
Page 32: ...IM P612 18 ST Issue 3 32...