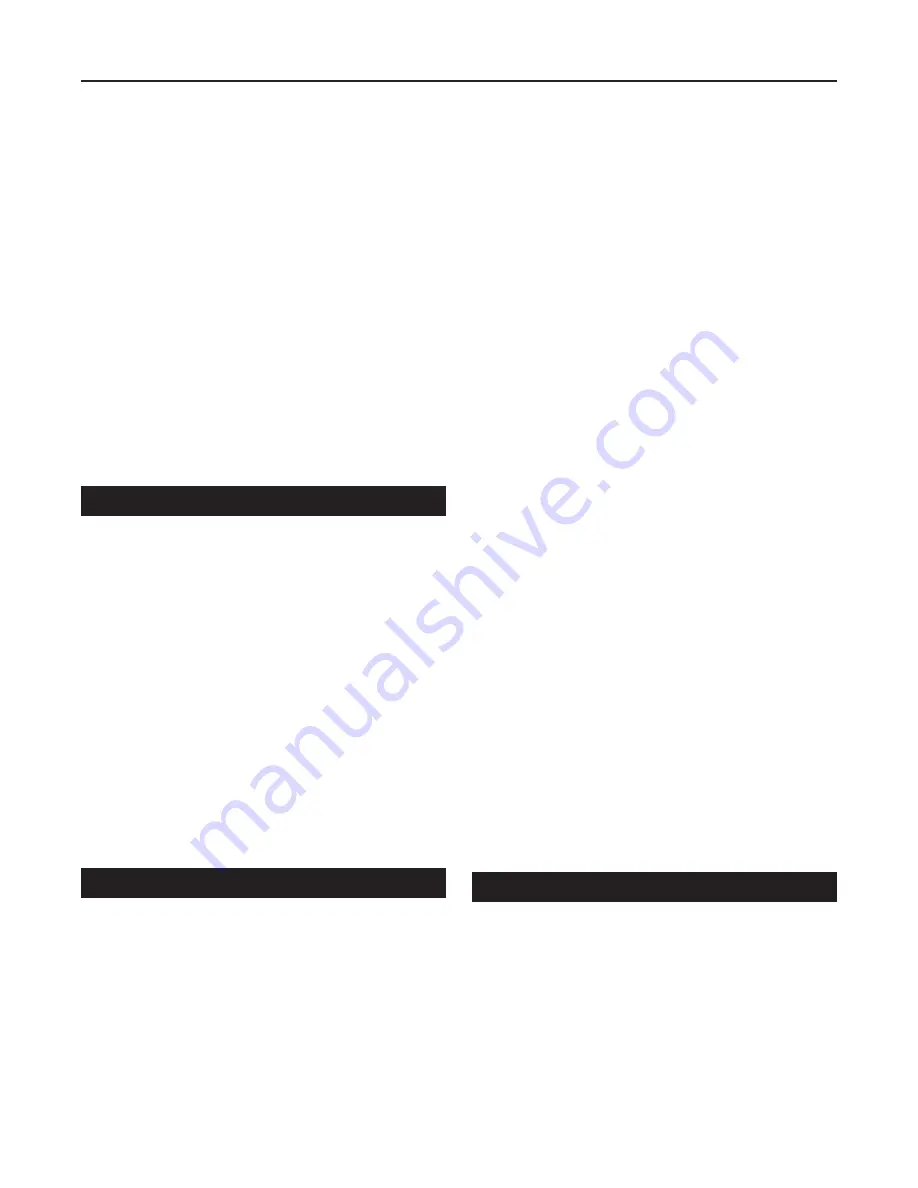
Principle of Operation
The regulator is operated by initial steam or fluid
pressure. It is normally closed, being held so by initial
pressure on the disk and by an internal main spring.
When the pilot is opened, initial pressure flows through
the pilot to the 8B tee. Bleedport 4A restricts the flow
and pressure builds under the diaphragm and opens
the main valve. The 5A restriction elbow steadies the
operation of the regulator.
Delivery pressure feeds back through the control pipe
to the pilot diaphragm. As this pressure approaches a
balance with the air loading signal, the pilot throttles
the loading pressure. In turn, the main valve takes
a position established by the loading pressure
where just enough steam flows to maintain the set
delivery pressure.
Installation
▲
WARNING
Personal injury or system damage may
result if this pilot is installed, without
appropriate overpressure protection,
where service conditions could exceed
the limits given in the Specifications
section and/or pilot nameplate.
Additionally, physical damage to the
pilot may result in personal injury or
property damage due to escaping
of accumulated gas. To avoid such
injury and damage, install the pilot in a
safe location.
All pressure equipment should be
installed in a non-seismic area;
should not be exposed to fire; and
should be protected from thunderbolt
(lightning) strikes.
△
CAUTION
The piping system must be
adequately designed and supported
to prevent extraordinary loads to the
pressure equipment.
Planning
1. Locate the regulator in a horizontal pipe.
2. Provide a trap ahead of the regulator to prevent
water hammer and erratic operation.
3. Use strainer to protect the regulator and avoid
damaging effects of scale and dirt in pipelines.
4. Provide a three valve bypass to facilitate
inspection of the regulator without
interrupting service.
Main Valve
1. Flush the main piping system thoroughly to clear it
from welding beads, scale, sand, etc.
2. Mount main valve with diaphragm chamber down
and arrow on body pointing in the direction of flow.
Screwed end valve should be mounted in unions.
Pilot
1. Mount the pilot on either side of the main valve
by means of a 1/4 in. / 6.35 mm nipple and
union provided Make this connection to the
1/4 in. / 6.35 mm pipe tap on the inlet of the
main valve.
2. Screw 4A bleedport fitting into 1/8 in. / 3.18 mm
pipe tap on the outlet of the main valve body.
Note
Bleed orifice in this fitting is vital to
operation of regulator.
3. Screw 8B tee into 1/8 in. / 3.18 mm pipe tap in
pilot. Select tap facing downstream.
4. Screw 5A elbow containing restriction orifice into
1/8 in. / 3.18 mm pipe tap on underside of main
valve diaphragm chamber. If initial pressure or
pressure drop is less than 15 psi / 1.03 bar, a 5B
open elbow without orifice is used.
5. Connect tubing bends as illustrated in Figure 2.
Maintenance
▲
WARNING
To avoid personal injury, property
damage or equipment damage caused
by sudden release of pressure or
explosion of accumulated gas, do
not attempt any maintenance or
disassembly without first isolating the
pilot from system pressure and relieving
all internal pressure from the pilot.
Pilots that have been disassembled
for repair must be tested for proper
4
D Series