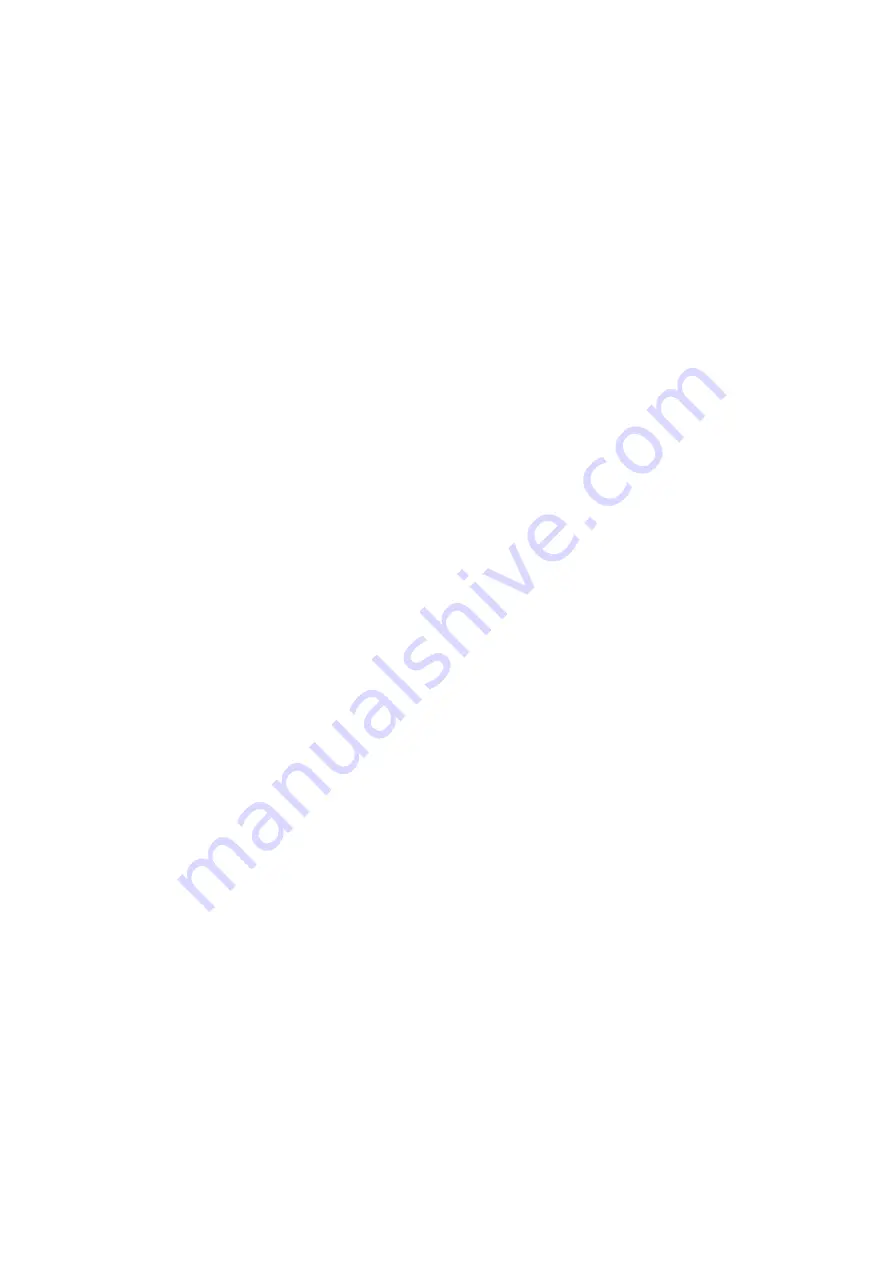
7 - Spedo 2600 Service Manual
SP 007 011
Maintenance Procedures
WARNINGS
Electrical
Before starting any maintenance, ensure that the forms cutter has been disconnected from the main
electrical supply.
Clothing & Jewellery
Never operate the forms cutter when wearing items of loose clothing or other decorative jewellery,
such as necklaces or bracelets as they could become entrapped in the machinery and cause injury.
Cutting blades
The putting into operation of the machine, especially the actuation of the cross-cut forms cutter
blade pre-supposes that the forms cutter has been correctly installed by a Spedo trained technician.
The first time that the cross-cutting blade is to be actuated, it must only be carried out manually by
a Spedo trained technician.
The angular blades on the edge trimmers, the centre cutter and the cross-cutter are extremely sharp
and care should be taken to protect fingers when the protective cover has been opened.
The manufacturer is not liable for damage caused by non-observance of the procedures given in this
manual. Never touch the working area of the longitudinal cross-cutting blade. This is applicable
especially when standing at the stacker end, when the motor is running. If any malfunction occurs,
contact the Customer Services Department of Spedo or their agent for assistance. DO NOT
ATTEMPT to correct any mechanical malfunction that occurs unless qualified to do so.