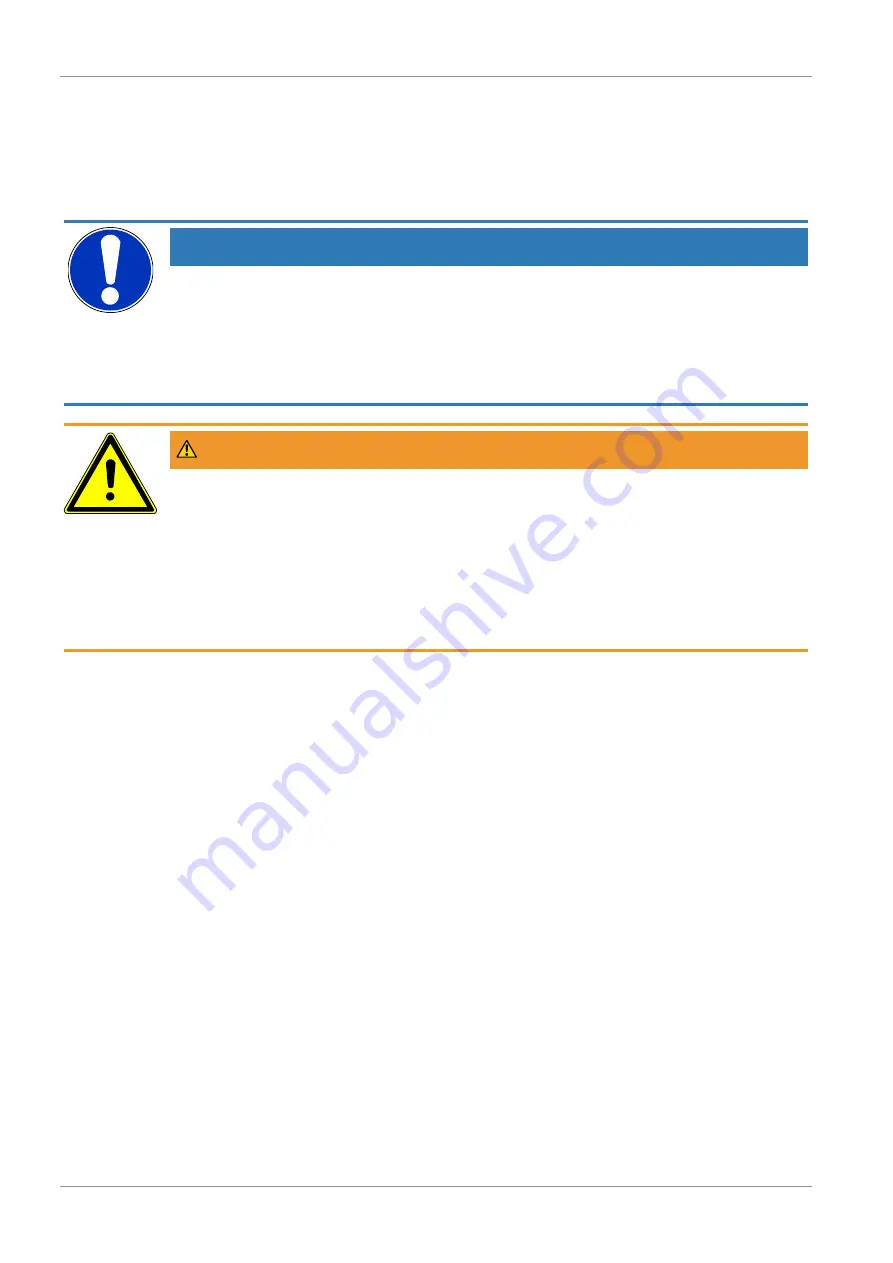
7 | Operation
Spectron Gas Control Systems GmbH
16
GES_CRF62_0222
7 Operation
7.1 Exchanging the process gas source
NOTICE
Penetration of ambient air into the system
Each time you change the cylinder, ambient air gets into the connecting parts of the system. To
prevent the gas and the entire system from being contaminated, the connection must be purged
before gas is drawn from the cylinder again. In the case of non-toxic, non-corrosive gases, this
can be done by means of multiple pressure purges with process gas. In the case of corrosive or
toxic gases or gases that are hazardous in some other way, purging must be carried out with in-
ert gas.
WARNING
Gas source exchange
If a gas source exchange is performed incorrectly, gas leakage and poisoning of persons may
occur.
a) The gas source exchange are to be carried out by trained specialist personnel and never
unattended.
b) A pressure test must be conducted after each gas source exchange.
c) For each gas source exchange, a new seal suitable for the used gas is to be used.
d) Wear the personal protective equipment prescribed in the risk assessment.
With each gas source exchange, check the port for leak-tightness. We strongly recommend re-
placing the gasket every time the gas source is exchanged. Always turn the shut-off valves
slowly and as far as the stop when opening or closing them!
Removing the empty process gas source:
1. Close the process gas source valve.
2. Briefly open the venting valve or decrease the pressure via the process.
3. Ensure that the pressure gauges indicate 0 bar and thus that the pressure regulator is fully
relieved.
4. Fully release the adjustable pressure regulator.
5. Disconnect the process gas source connection.
6. Mount the sealing nut on the gas source valve and protective cap on the process gas
source.
7. Identify, secure and remove the empty process gas source.
Connecting the new process gas source:
1. Provide new process gas source, position in front of the bracket and secure using the safety
chain.
2. Remove and retain the protective cap and screw plug.
3. Check the port thread and gasket; a new gasket must be used each time the gas source is
exchanged.
4. Screw the process gas connection onto the gas source valve by hand and tighten it gastight
with a spanner.