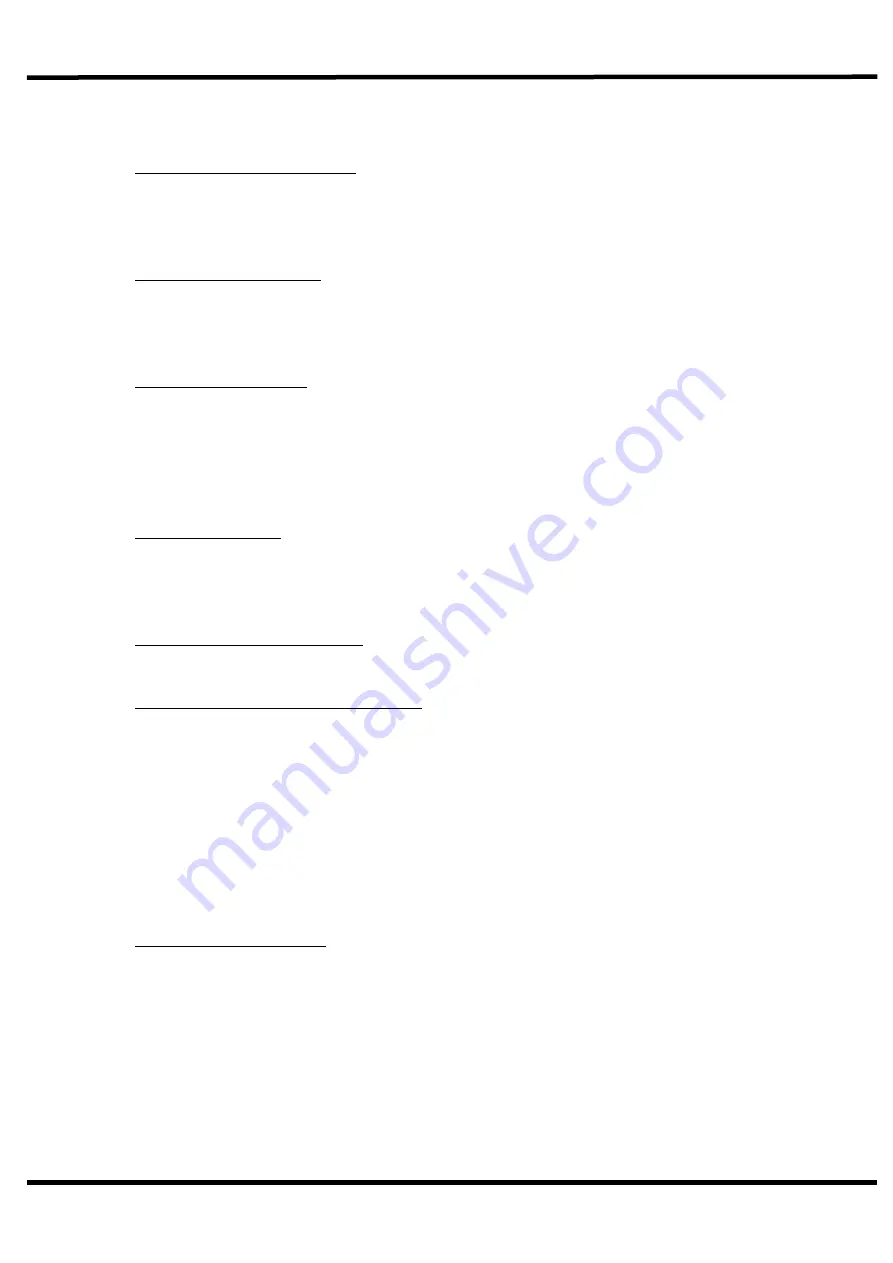
STARCUT
300
Trouble Shooting Guide
Broken or Damaged Blades
•
Raise cutting height
•
Avoid obstacles
•
Ensure a steady feed into drive (do not snatch the PTO)
Damage Blade Holders
•
Raise cutting height
•
Avoid obstacles
•
Failure to keep retaining nuts and bolts tight
Gearbox Overheating
•
Incorrect oil level
•
Incorrect grade of oil
•
Incorrect operating speed
•
Machine overloaded
•
Rubbish around the gearbox reducing air circulation
Slip Clutch Failure
•
Machine overloaded
•
PTO engaged with too much power/revs
•
Blades hitting the ground
Damage to Rubber Coupling
•
Shock loading from either poor start-up or blades hitting something
Damage to PTO Shaft & Gearboxes
•
Inoperative torque limiter
•
Seized slip clutch
•
Telescopic tube bottoming out
•
Engaging drive with too much power/revs
•
Lifting machine too high
•
Not enough overlap
•
Lack of grease on sliding tubes of drive shaft
•
Shock loading as a result of impact damage due to the blade carrier
striking an obstacle.
Metal Fatigue on Frame
•
Too fast a travelling or operating speed for the conditions
•
Machine not floating, i.e. not following the ground controls (check
position of top link).
17