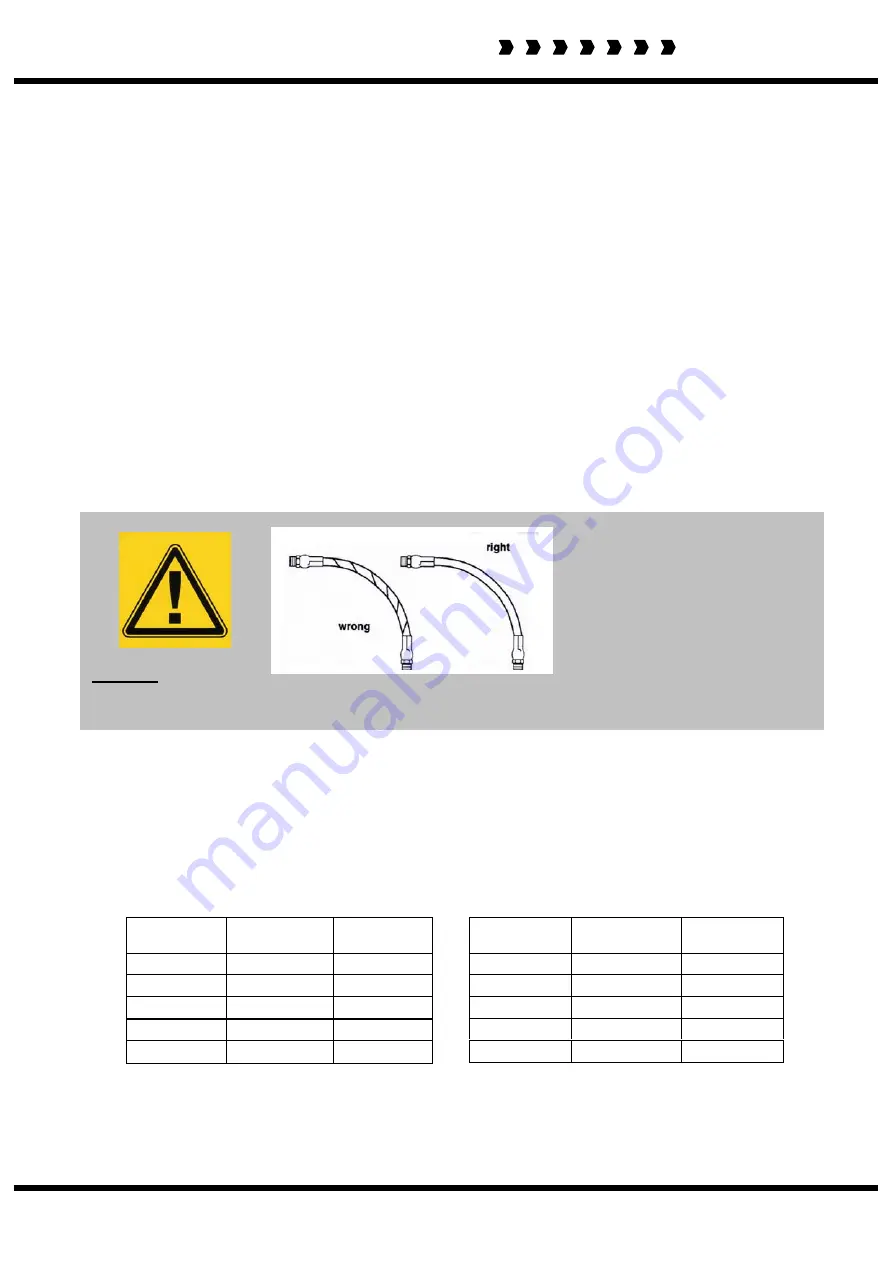
Recommended torque settings for hose unions
in conjunction with bonded seals
Service and maintenance
Hydraulic hoses
Carefully check condition of all hoses during routine service, paying particular attention to
chafed outer casing. Securely wrap with waterproof adhesive tape to stop the metal braid
from rusting.
Daily inspect all hydraulic hoses and fittings to be in good order. Any damages or leaks must
be rectified immediately, this is part of the daily maintenance and it is your responsibility to
help ensure a long reliable working life. Spearhead provide a tool kit to enable hoses to be
tightened as part of routine maintenance.
Hoses with damaged metal braid should be replaced.
When replacing hoses, quote number stamped on fitting at one end. The Spearhead
hydraulic system works at very high pressure. Use only genuine hoses, a burst hose could be
very dangerous.
Always replace hoses in exactly the same way they were removed, and to avoid twisting
during fitting use two spanners to slacken and tighten.
Always check the yellow protective sleeving is in good order, replacing sleeving is far cheaper
than replacing expensive hoses.
Hose warranty is limited to replacement of hoses due to faulty materials or manufacture.
Warranty will not be considered on hoses damaged by chaffing, abrasion, cuts or pinching
while in work, or to damaged threads due to over tightening.
All hose connections are of a “Parker” soft seal type and only need 1/2 a turn more than finger
tight to become leak proof. When dismantling, the hose should be manually flexed to relieve
any pressure, and the retaining nut slackened before complete disassembly.
BSP
(size)
Tightening
(Nm)
Torque
(ibs/ft)
1/4 “
24
18
3/8”
33
24
1/2”
44
35
3/4”
84
62
1”
115
85
BSP
(size)
Tightening
(Nm)
Torque
(ibs/ft)
1/4”
34
25
3/8”
75
55
1/2”
102
75
3/4”
183
135
1”
203
150
Spearhead
Warning
Hose is weakened when installed in twisted position. Also, pressure pulses in twisted hose tend to fatigue
wire and loosen fitting connections. Design so that machine motion produces bending rather than torsion.
Recommended torque settings for nut
Excel 606, 686, 726 & 836
49