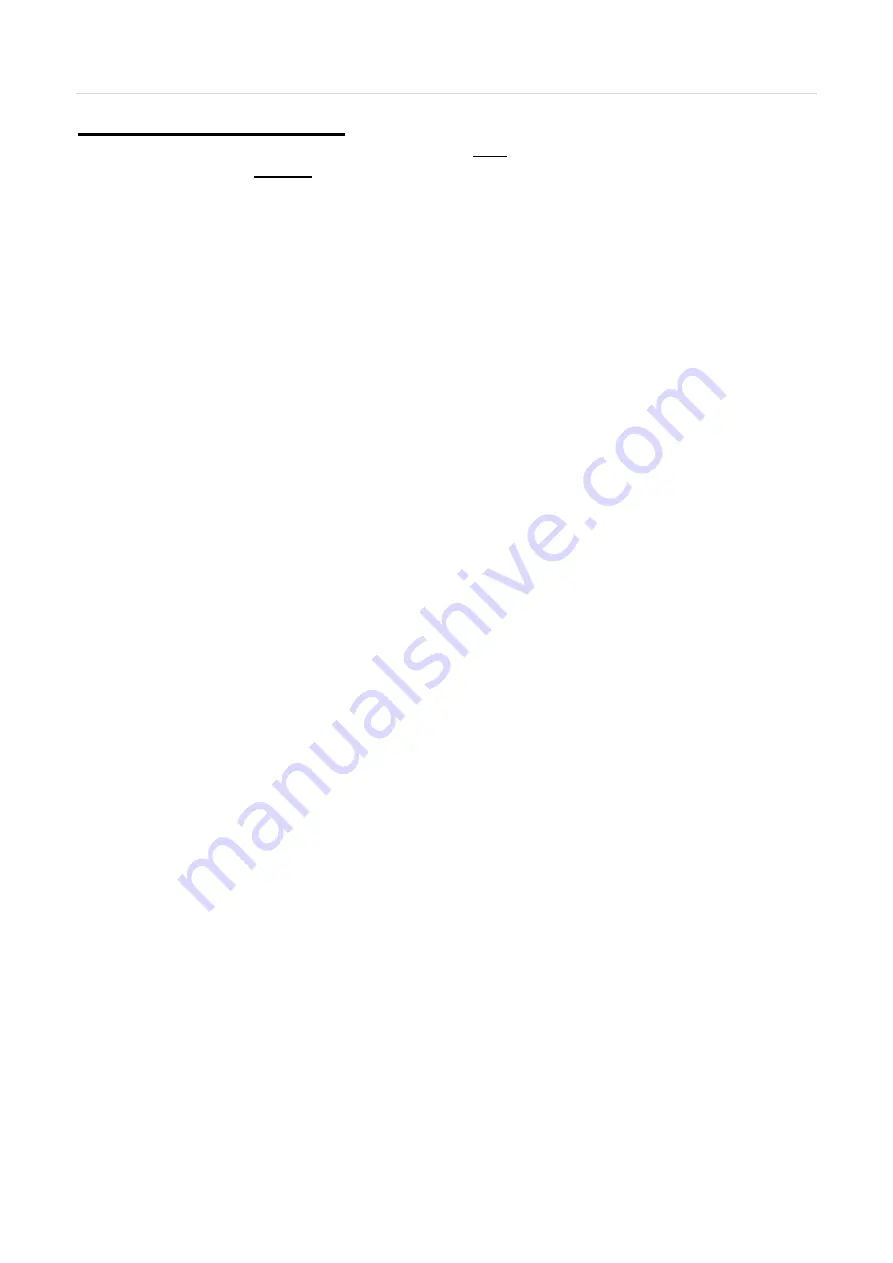
BEF200N
PARTS BOOK
OIPB-S18001
7
GENERAL OPERATION
•
Excessive downward pressure on the cutters may marginally improve the work
rate/finish but the definite increase in wear rates on the cutter drum assembly, machine
components and overloading the motor is the negative result.
•
Two light passes are quicker and more cost effective than one slow heavy pass. Tests
have proven conclusively that heavy downward pressure reduces cutter and drum life by
over 50%.
•
To remove dust, connect an industrial dust collector or vacuum to the 50mm port at the
rear of the machine. We recommend SPE Dust Control units for near-100% dust control.
In the absence of a dust control unit it is acceptable to spray water onto the surface or
to feed water down the vacuum port. Cutter drum assembly life is increased by around
10% when operating the machine in this way.
•
Electrical motors and switches are not waterproof, take care to protect them from
splashes.
•
The BEF200N is normally operated in a forward direction. The operator varies the speed
of travel to determine the final finish, having already pre-set the depth control. It is
permissible to operate the machine with a backwards and forwards action. Each pass
should be overlapped to produce a uniform finish.
Summary of Contents for BEF200N
Page 14: ...BEF200N PARTS BOOK OIPB S18001 14 PARTS LIST 1 SCARIFIER GENERAL ASSEMBLY DIAGRAM BEF200N ...
Page 16: ...BEF200N PARTS BOOK OIPB S18001 16 PARTS LIST 2 SCARIFIER FASTENERS BEF200N ...
Page 18: ...BEF200N PARTS BOOK OIPB S18001 18 ELECTICAL DIAGRAM BEF200N 1 ...
Page 19: ...BEF200N PARTS BOOK OIPB S18001 19 BEF200N 2 ...
Page 20: ...BEF200N PARTS BOOK OIPB S18001 20 BEF200N 2A ...
Page 21: ...BEF200N PARTS BOOK OIPB S18001 21 BEF200N 3 ...
Page 32: ......