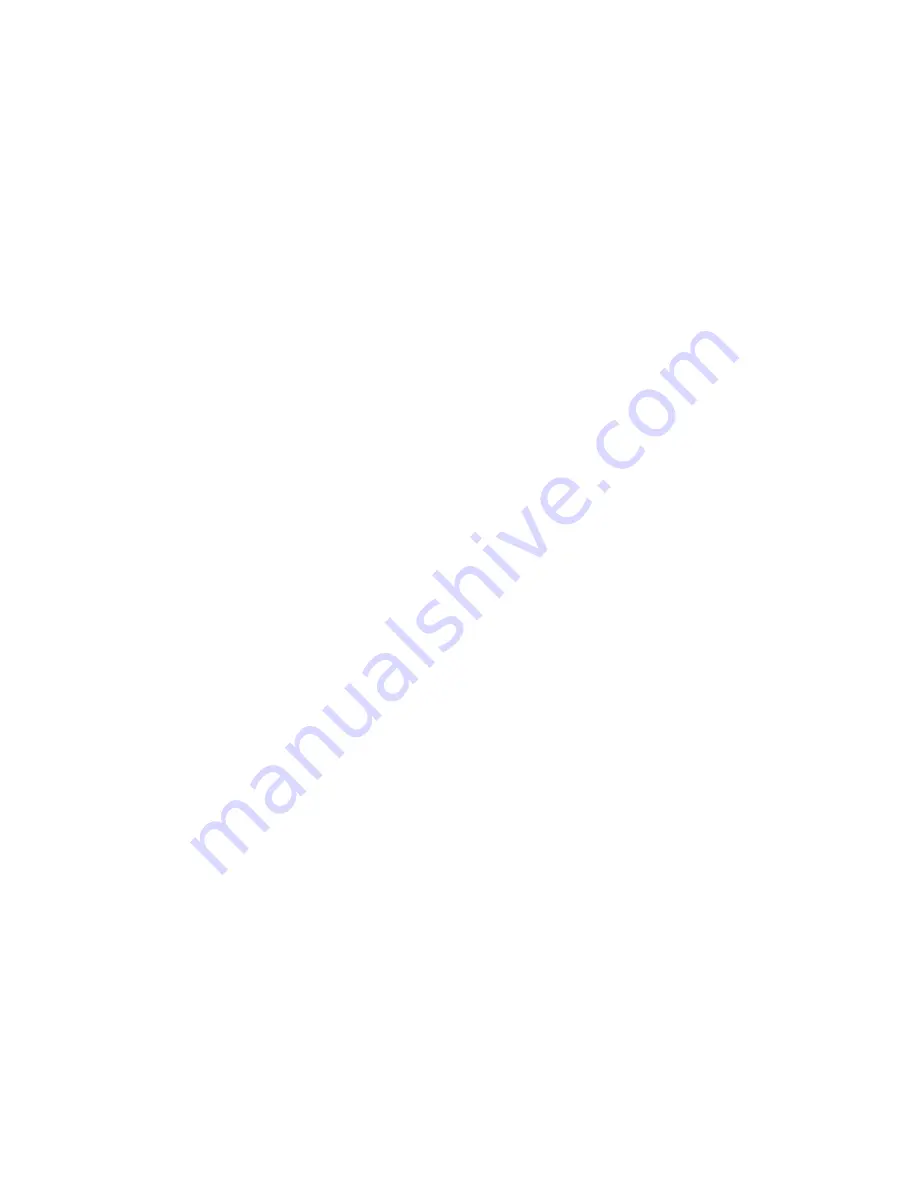
12
OPERATION
Before operating the air compressor, always check first to ensure that it has been received, inspected and installed in
accordance with the instructions herein. Rectify any discrepancies before proceeding further.
Check the compressor pump oil level by looking at the sight glass. The oil level should be at the top of the red circle on
the oil sight glass. Add oil, if required, through the oil fill cap and only when the unit is not operating. Do not overfill with
oil. Refer to the Maintenance and Repair section for recommended oil specifications. Check that the outlet valve, if fitted,
is closed. Any connected air hose(s) and/or distribution pipe(s) should not be open to the atmosphere. This is to prevent
any injuries from “hose whip” and/or high pressure air discharge and also to avoid unattended compressed air discharge
to the atmosphere. In the event that an air line is cut or broken, the air supply must be immediately closed off at the
compressor either by shutting the discharge outlet valve or switching off the compressor. Do not attempt to “catch” the
loose end of a discharging air hose.
Check that the tank drain valve is closed. Take care when discharging air from the tank, i.e. from the safety valve, the
drain valve or the air outlet, to ensure that it does not cause dirt, stones, metal swarf or other particles to be blown
around.
Any unusual noise or vibration likely indicates a problem with the compressor. Do not continue to operate the unit until
the source of the problem has been identified and corrected.
Duty Cycle
To maximize service life, the air compressor should be adequately sized for its given application. It should ideally
operate in a repeating run-stop or pump-unload cycle, with total compressor “pumping” time not exceeding 50% or 30
minutes in every hour on average. The elapsed time between the start and finish of any given pumping cycle (i.e. the
continuous duration that the electric motor operates) should not exceed 30 minutes. If the unit cannot supply the
compressed air demand without exceeding the above duty cycle limits, then either the demand should be reduced or the
compressor should be replaced with a larger unit having greater free air delivery.
The duty cycle limit is intended to protect the compressor pump valves and heads against stabilized high operating
temperatures that can cause premature pump failure.
Run in procedure
When starting for the first time leave the air compressor run for 10 minutes without load, leave the air cock completely
open. After 10 minutes check that the drain cock is closed and shut the main air cock. As tank pressure increases
check that the compressor stops automatically once maximum pressure is reached.
*Note: All compressors are delivered only after a successful testing period at the factory.
For the long life of your compressor it is recommended that you drain and replace the pump lubricant
after 10 hours
of use
,
Drain the oil while it is still warm this will help remove any abrasive particles loosened from the initial run in
period. Replace pump oil with Scorpion Compressor oil AC-68.