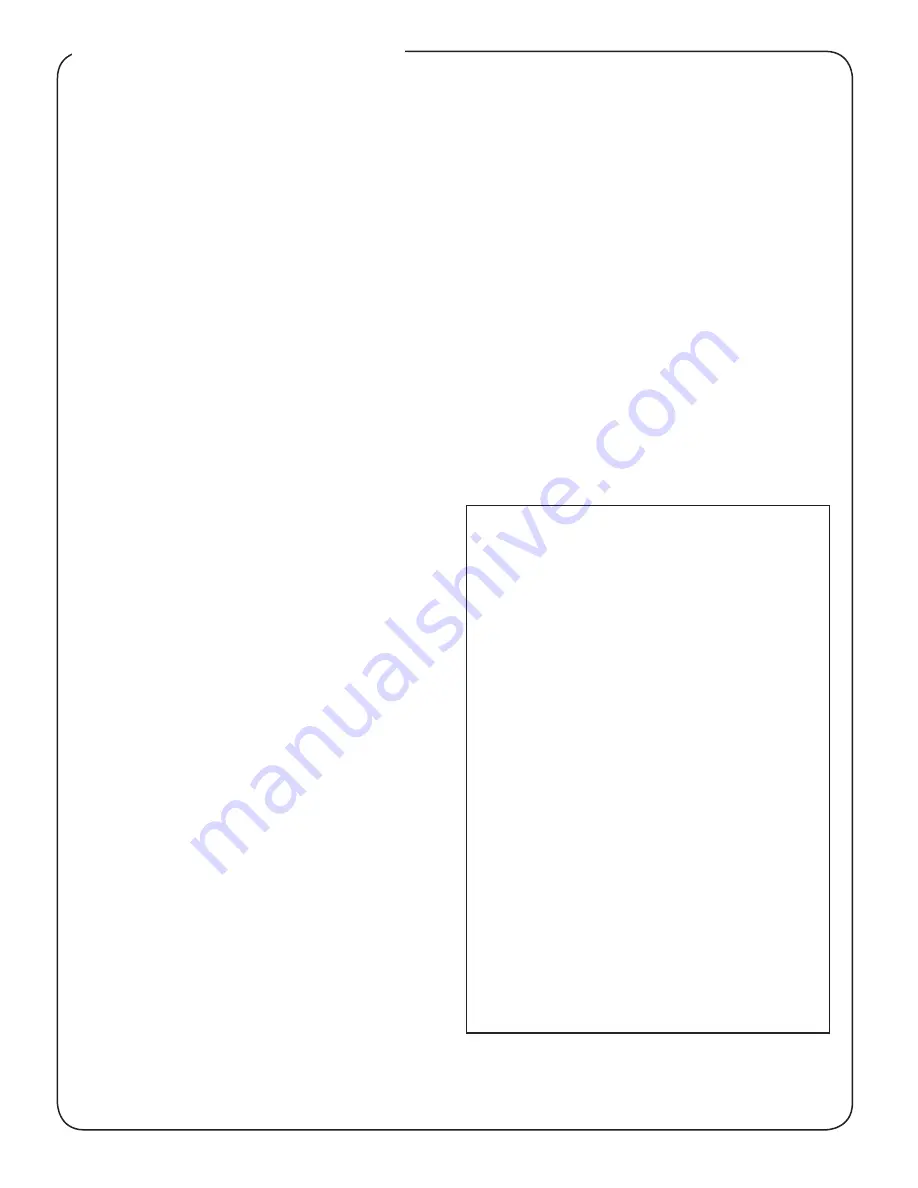
8
ZLS SERIES — FLOOR HEIGHT LIFT TABLES
ZLS Series Owner’s Manual
Positioning the Lift
1. Remove the shipping material and unskid the lift.
On the front of this manual, write down the model
number, serial number, and date the lift is placed in
service. You can find the model number and serial
number on the name plate.
2. Move the lift into position, supporting the base of
the lift. Use the lifting eyes at each end of the unit.
Once the unit is in position, remove the shipping
brace which connects the two base frames. This
brace is held in place by the two eyebolts on the
front of the unit. Remove these eyebolts, and also
the eyebolts on the rear of the unit.
3. Install the lift as shown in Fig. 2. Bolt the lift to the
floor using four lag bolts. These should run through
the lag plates at each end of the base frames.
Insert and tighten the lag bolts to secure the lift.
Grout under the base rails to prevent vibration and
distortion of the base frame.
CAUTION!
Do not try to move the lift by supporting the
table top. One end of the table top is free.
WARNING!
If the lift is mounted on an unstable surface,
it may tip over when it is in use. You may
be hurt, and the lift and load may be
damaged.
4. Attach the flexible safety lip to the front of the unit
using the screws supplied (#10-24 x 3/8’’).
5. The standard unit has a 5 foot hose (1.2m)
connecting the power unit to the lift. This can be
extended to a maximum of 50 feet (12.7m).
Hydraulic Connections
(External Power Units Only – If Internal Power Unit,
proceed to step 10.)
8. Install the power unit. Install the hydraulic line
between the power unit and the lift as shown on the pit
plan.
9. Blow out the hydraulic line with compressed air
before connecting it to the power unit. Replace the solid
plug on the hydraulic fluid tank with the vented plug
supplied, then attach the vent line to the vented plug.
WARNING!
Be sure that the hydraulic line will not be
pinched by the lift as it raises or lowers. If
you allow the line to be pinched, the lift may
not work properly. A hose may break, the
lift table may drop suddenly, and someone
may be hurt.
CAUTION!
It is very important to keep the hydraulic oil
free of dirt, dust, metal chips, water, and other
contamination. Most of the problems with
hydraulic systems are caused by contamination
in the oil. Be sure to flush all hydraulic lines
before connecting remote power units.
CAUTION!
If you do not install the vented plug in the tank,
the pump may be damaged.
Table 1 – Hydraulic Oil Specifications
If the lift will be used at normal ambient temperatures,
Southworth supplies the unit with CONOCO 32 oil. This
may be replaced by any other good quality oil with 150
SSU at 100° F and rust and oxidation inhibitors and
anti-wear properties. If the lift will be used at ambient
temperatures below 0°F, use aircraft hydraulic oil. Use
Type 15 aircraft hydraulic oil.
The following are equivalent to CONOCO 32:
TYPE
.......................
MANUFACTURER
DTE 24 ....................EXXON/MOBIL
NUTO H32 ...............EXXON/MOBIL
AMOCO AW32 ........CHEVRON (AMOCO CO.)
CITGO AW32 ............CITGO
CAUTION!
It is very important to keep the hydraulic
oil free of dirt, dust, metal chips, water, and
other contamination. Most of the problems
with hydraulic systems are caused by
contamination in the oil.