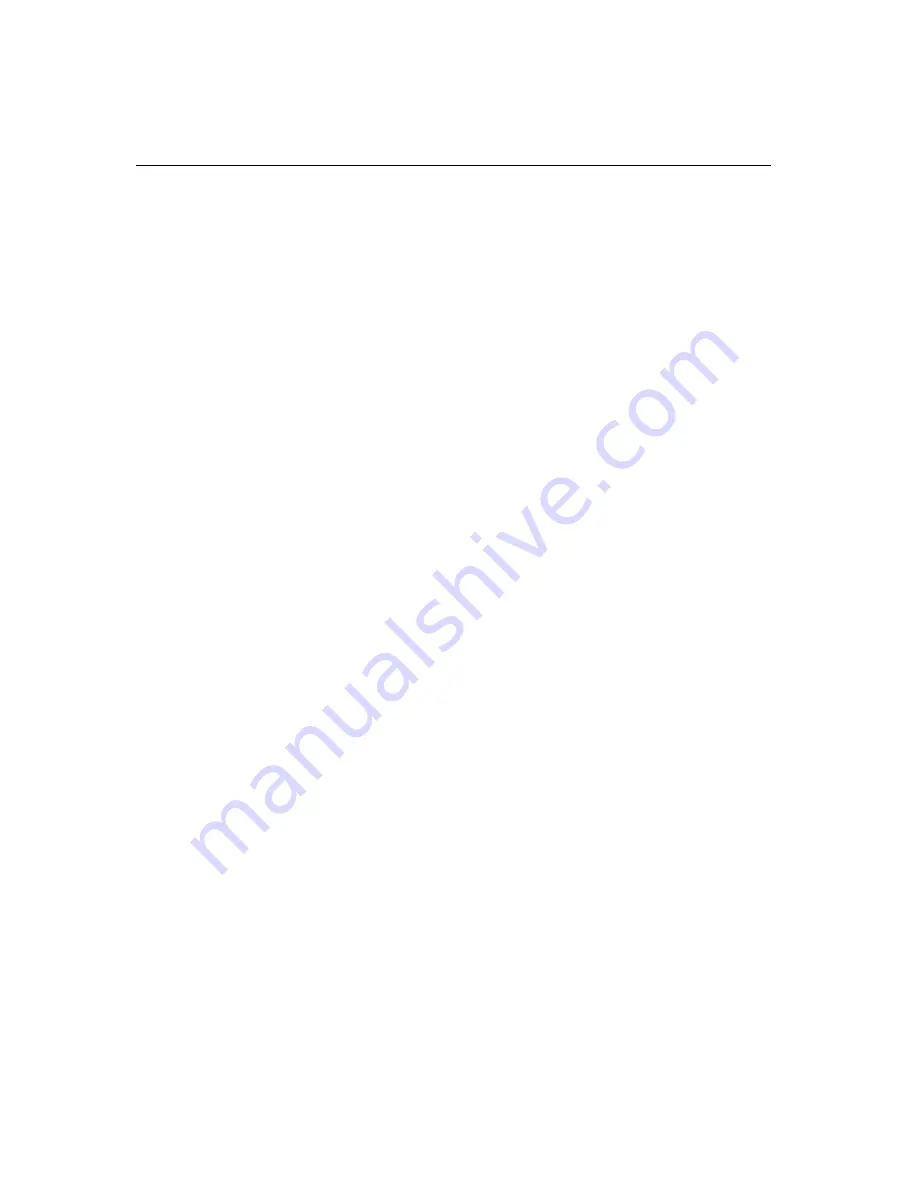
PERIODIC MAINTENANCE
SECTION 3:
STEAM-EX MODEL GCX-2
FLOOR MOUNTED CONVECTION STEAMER
Item I: Hot Water Solenoid Valve fastened to the bottom of Generator Control Box immediately in Front of Item J feeds hot
water to the Boiler but its functioning is entirely dependent on the Water Level Control (Item Q).
Item J: Operating Pressure Switch fastened to the inside bottom front of the Generator Control Box is plumbed to sense
the pressure in the Boiler and thence control the operating cycle of the Gas Combination Control Valve (Item I). This
switch is factory set to energize the Gas Combination Control Valve and ignite the Main Burners at 6 psi but to de-energize
the Valve and turn off Burners at
7
-1/2 psi thus maintaining a pressure range in the Boiler between 6 psi to approximately
8 psi (override considered).
Item K: Hi-Limit Pressure Switch similar to and located directly behind the above switch is a protective device intended to
shut off the Gas Combination Control Valve and Burners at approximately 14 psi and will only function if the Operating
Pressure Switch fails.
Item L: Power Switch fastened to the front face of the Generator Control Box when switched ON will automatically begin
the steam generating process in the Boiler.
Item M: Pilot Light is located directly above the Power Switch and when lit (green) indicates power is ON.
Item N: A Thermostat mounted on the back wall of the Generator Control Box has its heat sensing capilliary bulb fastened
to the appliance Drain. When excessive heat (i.e.. steam) comes in contact with the bulb, the Thermostat will energize the
Cold Water Solenoid Valve (Item J).
Item 0: The Pressure Gauge is directly above and threaded to the Water Level Control. It should read '0' during shut down
and function in a range of approximately 6 to 7.5 psi during operation of the appliance.
Item P: Safety Valve is a protective device set at 15 psi. Malfunction or improper setting of controls may allow the pressure
to exceed 15 psi in the Boiler and will consequently set off this valve.
ONCE A WEEK THIS VALVE SHOULD BE TRIPPED DURING OPERATION TO ASSURE THAT IT
FUNCTIONS PROPERLY.
Item Q: The Water Level Control is a mechanical switch intended to maintain proper water level in the Boiler. A Float is
contained within the chamber of the Water Level Control and when it drops, it will trip the switch in the control and demand
sufficient water to replenish it to the proper level.
A MANUAL VALVE LOCATED DIRECTLY BELOW THE WATER LEVEL CONTROL CHAMBER
MUST BE OPENED BRIEFLY AT LEAS T ONCE A WEEK TO BLOWDOWN SEDIMENT AND
SCALANT THAT MAY BE LODGED IN THE CHAMBER. FAILURE TO DO SO MAY CAUSE
EXCESSIVE ACCUMULATION. SEIZURE OF THE FLOAT AND EVENTUAL MALFUNCTION OF
THE WATER LEVEL CONTROL.
Item R: A Thermostatic Steam Trap is plumbed to the steam supply piping from the Boiler and is a mechanical device that
closes on high temperatures and opens when the temperature drops. This Trap allows air and water formed from
condensed steam to exhaust into the appliance Drain but will retain steam being of a higher temperature.
8
Summary of Contents for GCX-2S
Page 8: ...PARTS LIST SECTION 7 STEAM EX MODEL GCX 2 COOKER CONTROL COMPONENTS FIG 2 6...
Page 12: ...PERIODIC MAINTENANCE SECTION 3 STEAM EX MODEL GCX 2 FLOOR MOUNTED CONVECTION STEAMER FIG 3 10...
Page 24: ...Parts ListPARTS LIST SECTION 7 STEAM EX MODEL GCX 2 GENERATOR ASSEMBLY FIG 5 21...
Page 26: ...PARTS LIST SECTION 7 MODEL GCX 2 GAS BOILER ASSEMBLY 23...
Page 28: ...PARTS LIST SECTION 7 STEAM EX MODEL GCX 2 GENERATOR CONTROL BOX ASSEMBLY FIG 7 25...
Page 30: ...PARTS LIST SECTION 7 STEAM EX MODEL GCX 2 COOKER ASSEMBLY FIG 8 27...
Page 32: ...SECTION 7 STEAM EX MODEL GCX 2 DOOR ASSEMBLY FIG 9 29...
Page 34: ...PARTS LIST SECTION 7 STEAM EX MODEL GCX 2 COOKER CONTROL COMPONENTS FIG 10 31...
Page 36: ...WIRING DIAGRAM MODEL GCX 2 33...
Page 37: ...WIRING DIAGRAM MODEL GCX 2 34...