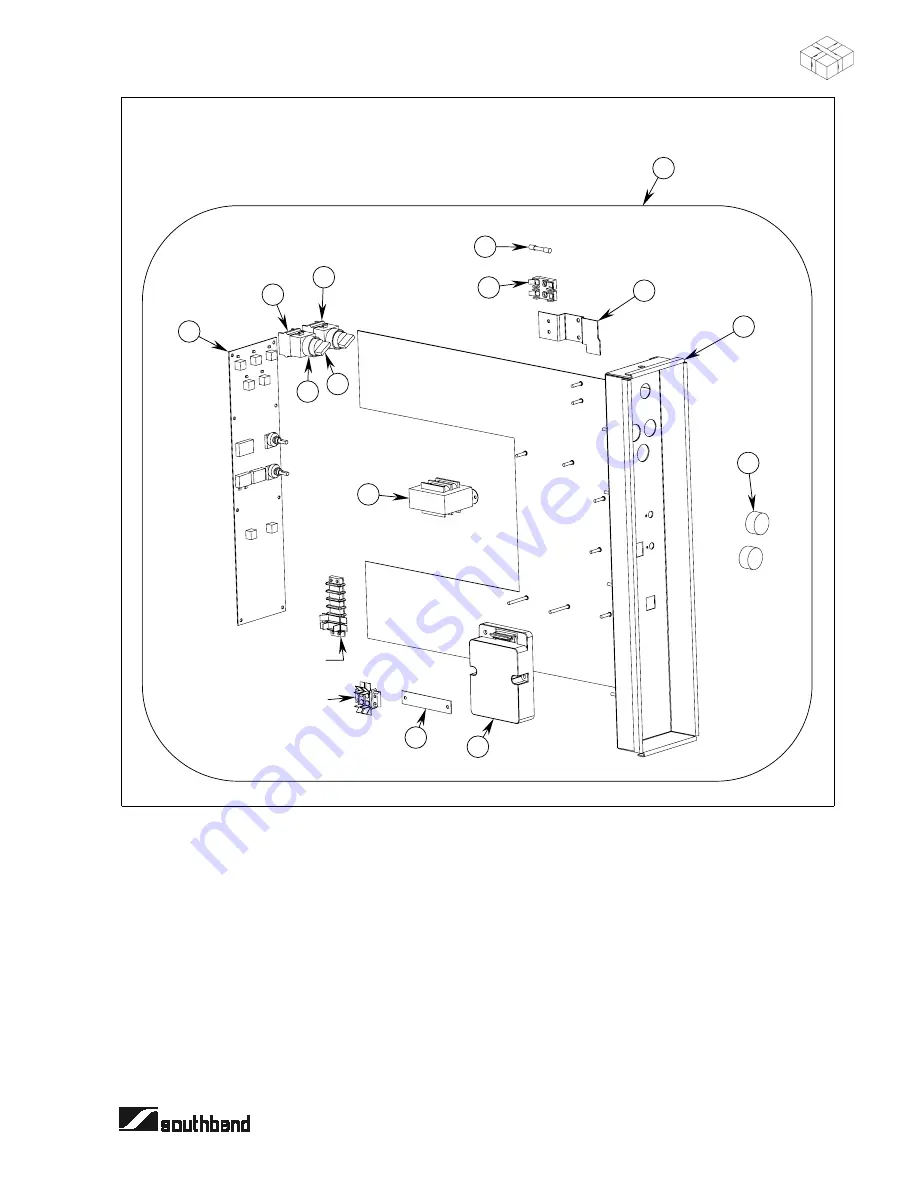
EZ C
OM
C
OMBINATION
O
VEN
P
ARTS
O
PERATOR
’
S
M
ANUAL
1182851
REV
2
P
AGE
37
PARTS
6 POSITION TERMINAL STRIP
(PART OF WIRING HARNESS, 1182398)
2 POSITION TERMINAL STRIP
(PART OF WIRING HARNESS, 1182398)
1
2
3
4
5
6
7
8
9
10
11
12
13
14
Control Panel Subassembly Parts
See parts list on previous page.