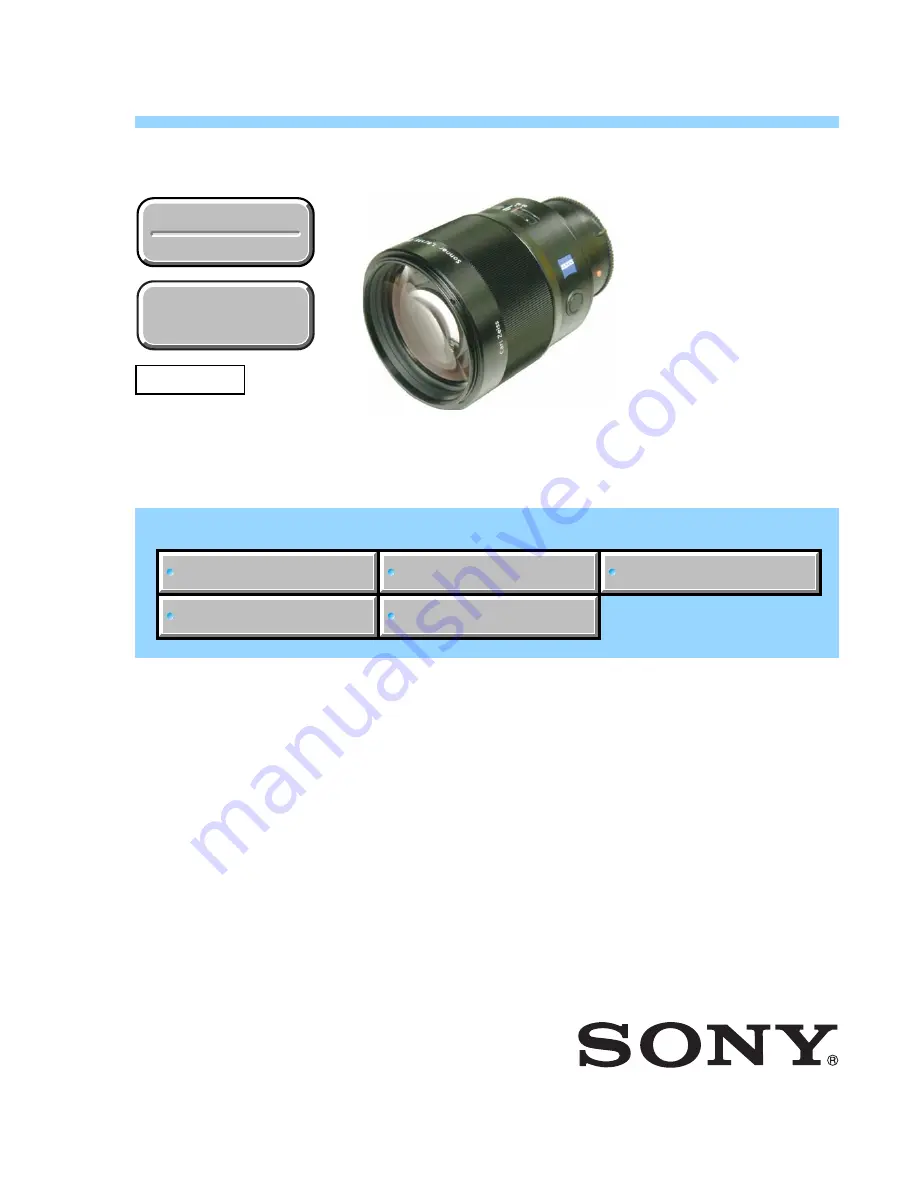
SERVICE NOTE
SPECIFICATIONS
REPAIR PARTS LIST
DISASSEMBLY
ADJUSTMENTS
SERVICE MANUAL
Link
Link
Revision History
Revision History
How to use
Acrobat Reader
How to use
Acrobat Reader
Sony EMCS Co.
SAL135F18Z (Sonnar 1.8/135 ZA) (Sonnar T
*
135mm F1.8 ZA)
Ver. 1.4 2007.12
LENS FOR DSLR CAMERA
2007L0800-1
© 2007.12
Published by Kohda TEC
9-852-110-12
US Model
Canadian Model
AEP Model
Chinese Model
SAL135F18Z
(Sonnar 1.8/135 ZA) (Sonnar T
*
135mm F1.8 ZA)
• About the Special Driver
• About the Lens Test Projector and Finished Inspection JIG
• About the Screw Filter Frame Assy.
• About the MTF measurement.
Revised-1
Replace the previously issued
SERVICE MANUAL 9-852-110-11
with this Manual.