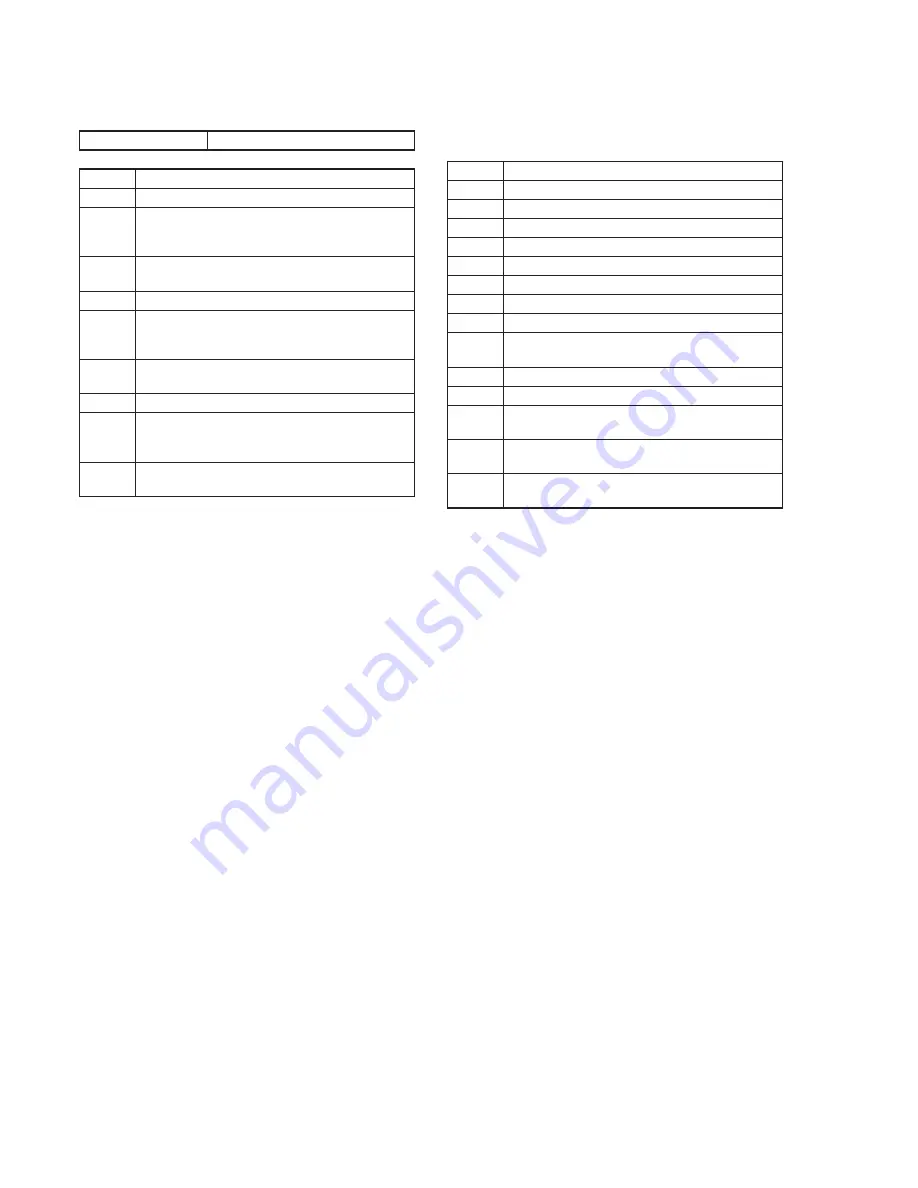
5-50
2. Emergency Memory Address
Page F
Address 10 to 1B
Address
Contents
10
1st EMG code
12
Upper: MSW code when the mechanism starts
shifting the 1st time
Lower: MSW code when the 1st emergency occurs
13
Lower: Target MSW code of the 1st emergency
occurs
14
2nd EMG code
16
Upper: MSW code when the mechanism starts
shifting the 2nd time
Lower: MSW code when the 2nd emergency occurs
17
Lower: Target MSW code of the 2nd emergency
occurs
18
Last EMG code
1A
Upper: MSW code when the mechanism starts
shifting the last time
Lower: MSW code when the last emergency occurs
1B
Lower: Target MSW code of the last emergency
occurs
When there are no emergency, data 00 will be written in the above
addresses (10 to 1B). When the first emergency occurs, the data
corresponding to the emergency will be written in the address (10
to 13) for this first emergency. In the same way, when the second
emergency occurs, the data corresponding to the emergency will be
written in the address (14 to 17) for this second emergency.
The data corresponding to the emergency occurring the last will be
written in the address (18 to 1B) for this last emergency.
Therefore the data of addresses 18 to 1B are renewed each time an
emergency occurs.
Note 1:
Be sure to rewrite the data of addresses 10 to 1B to 00 after repairs/
adjustments.
Note 2:
When rewriting the data, be sure to press the PAUSE button of the
remote commander after setting the data.
2-1. EMG code (Emergency code)
The codes shown in the following table which correspond to errors
that occur are recorded in addresses 10, 14, and 18.
Code
Type of Emergency
00
No error
10
Loading motor time-out during load
11
Loading motor time-out during unload
20
T reel emergency (reel slack) during unloading
21
S reel emergency (reel slack) during unloading
22
T reel emergency
23
S reel emergency
30
FG emergency at the start up of the capstan
31
FG emergency during the normal rotation of the
capstan
40
FG emergency at the start up of the drum
41
PG emergency at the start up of the drum
42
FG emergency during the normal rotation of the
drum
43
PG emergency during the normal rotation of the
drum
44
Phase emergency during the normal rotation of the
drum
Summary of Contents for CCD-TRV66PK
Page 11: ...1 2 ...
Page 12: ...1 3 ...
Page 13: ...1 4 ...
Page 14: ...1 5 ...
Page 15: ...1 6 ...
Page 16: ...1 7 ...
Page 17: ...1 8 ...
Page 18: ...1 9 ...
Page 19: ...1 10 ...
Page 20: ...1 11 ...
Page 21: ...1 12 ...
Page 22: ...1 13 ...
Page 23: ...1 14 ...
Page 24: ...1 15 ...
Page 25: ...1 16 ...
Page 26: ...1 17 ...
Page 27: ...1 18 ...
Page 28: ...1 19 ...
Page 29: ...1 20E ...
Page 40: ...CCD TRV63 TRV66 TRV66PK SECTION 3 BLOCK DIAGRAMS 3 1 OVERALL BLOCK DIAGRAM 3 1 3 2 3 3 3 4 ...
Page 48: ...CCD TRV63 TRV66 TRV66PK 3 9 POWER BLOCK DIAGRAM 3 29 3 30 3 31 3 32E ...
Page 50: ...CCD TRV63 TRV66 TRV66PK FRAME SCHEMATIC DIAGRAM 2 4 4 4 5 4 6 FRAME SCHEMATIC DIAGRAM 2 2 ...
Page 65: ...CCD TRV63 TRV66 TRV66PK 4 53 4 54 STEADY SHOT SE 83 AV IN OUT PJ 92 ...
Page 67: ...CCD TRV63 TRV66 TRV66PK 4 57 4 58 4 59 STEREO MIC AMP LASER LINK MA 351 ...
Page 73: ...CCD TRV63 TRV66 TRV66PK 4 75 4 76 4 77 USER CONTROL CF 56 MR 8500 ...
Page 76: ...CCD TRV63 TRV66 TRV66PK CCD TRV63 TRV66 TRV66PK 4 88E CONTROL SWITCH BLOCK FK 8500 SS 8500 ...