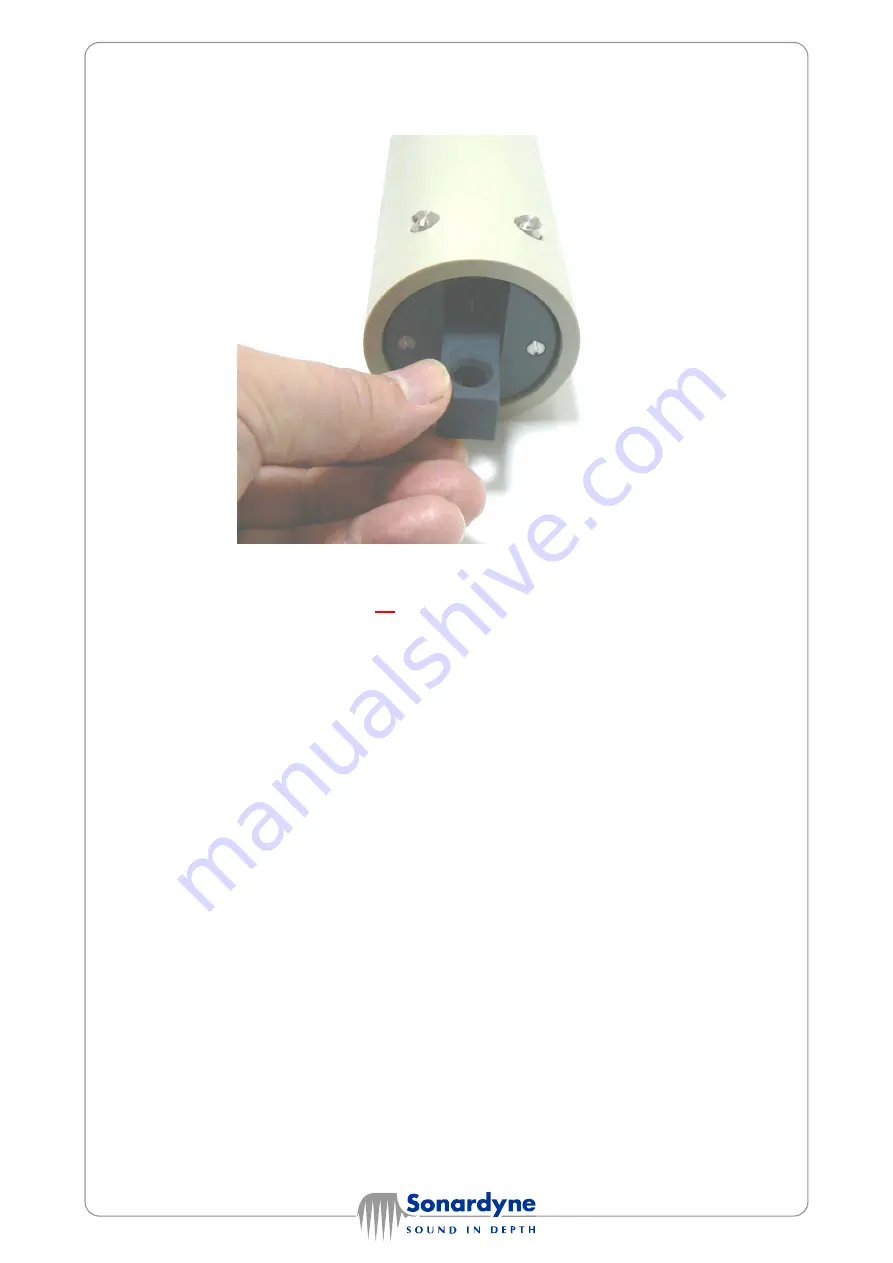
OM-7986
Page 7 of 23
Issue A - Rev 8
Fig.3 – Loading the release nut into the release mechanism
WARNING
– Ensure the nut is not engaged at an angle as this may cause the nut to cross-
thread causing damage, replace the nut if this happens. If the nut becomes cross-threaded
during loading the release mechanism may current-limit and stop before the nut bottoms
against the endcap. Always watch the nut being loaded and ensure that the nut stops
against the endcap during loading, or the SWL of the unit may be compromised.
Once significant load has been applied to a release nut then it should be replaced.
When operating the rope canister ensure the nut is loaded in the correct orientation, see
section 2.10.
2.5
Testing the Release Mechanism Prior to Deployment
The programming loop communicates with the LRT electrically. It cannot test the acoustic
output from the transducer, so it is always recommended that the remote transducer is used
to test the operation of the LRT in water.
WARNING
– Before deployment in water ensure that the red pressure-relief valve in the
release mechanism endcap is pushed home (note it is also sprung loaded).
Load the release nut and attach the LRT and nut by a short line and deploy in greater than 1
metre depth of water (a bucket can be used if necessary). Deploy the remote transducer
near to the LRT in the water and connect to the surface unit.
On the surface unit select the LRTs programmed acoustic identity, address group and
frequency. Press the TEST/RANGE button, the surface unit will interrogate the transponder
and listen for the reply. If a valid reply is received then the range in metres, if greater than
0.6m, will be displayed and a beep will be heard. If less than 0.6m away then ‘
PASS
’ will be
displayed. If no valid range is received then ‘
FAIL
’ will be displayed and no beep will be
heard.
NOTE -
if the LRT has the Tilt feature fitted, only every other interrogation will give a Range
reply if the unit is tilted beyond 30 degrees.
Summary of Contents for 7986
Page 25: ......