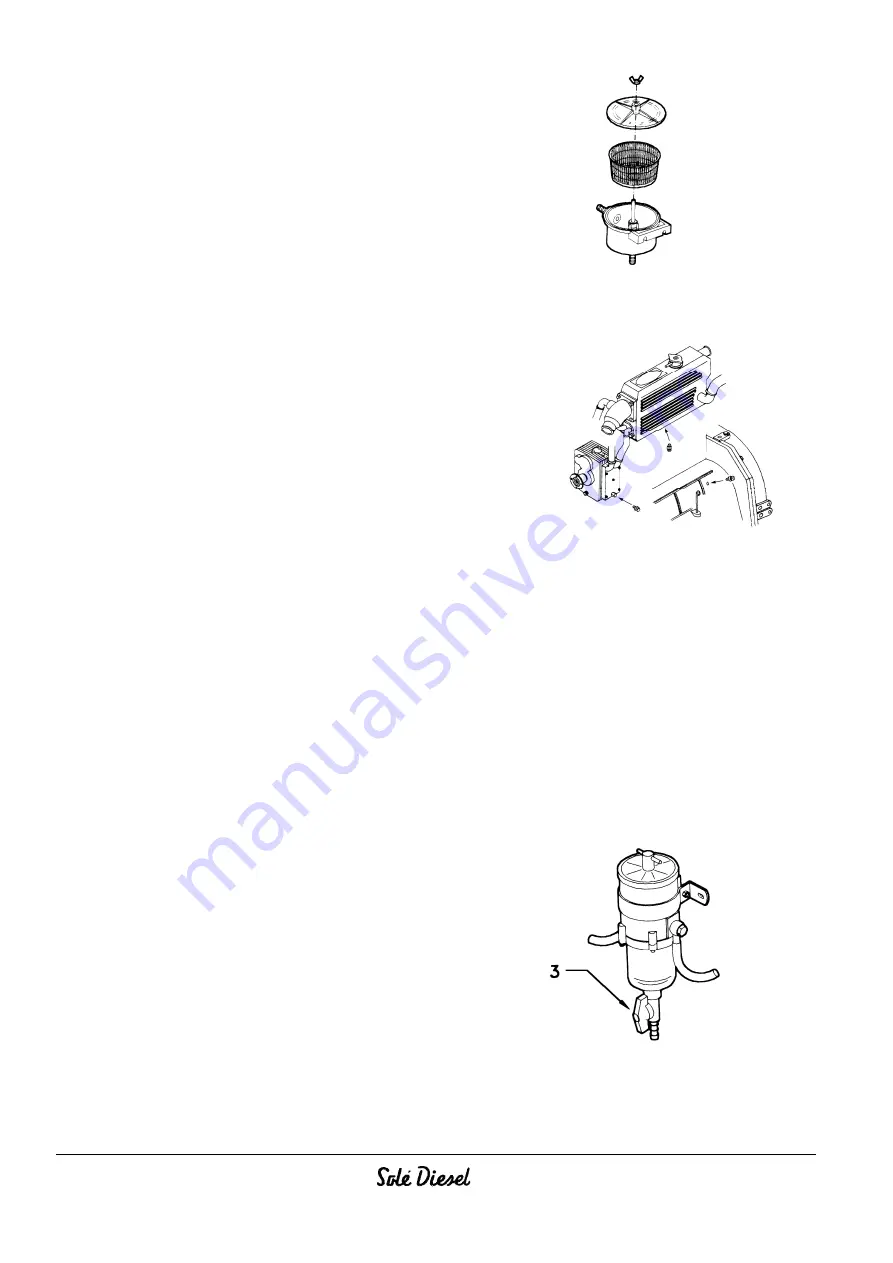
ENG - 28
03917101G.ENG rev. 0
(5)
Water filter cleaning:
It is important to fit between the engine and the bottom cock a filter
to avoid that any imputities existing in these a water might clog the
cooling conducts.
Filter shall be cleaned every 200 hours by loosening the wing nut
and removing the filtering component. Clean the filter and fit it
again taking care the cover is well seated on the O-ring (Fig. 7.4).
Then the engine is started to check if water is leaking from the
cover.
Fig. 7.4
(6)
Change cooling circuit water:
Drain off all the circuit water by opening the two drain cocks, one
in the exchanger an other in the cylinder block (Fig. 7.5).
When in cold climates, if the engine is not to be used for a long
period, it is advisable to drain the water circuit.
Once this operation has been completed, close the drain cocks
and fill to the hole in the tank cap (see heading 4.2.2 of this
manual).
Fig. 7.5
(7)
Checking battery electrolite level and charge:
Batteries require a very careful handling and frequent checkings. Proceed as shown below:
(1) Always keep batteries dry and cleaned.
(2) Regularly check terminal cleanliness. If dust is settled, terminals should be loosened, cleaned and smeared with a
neutral grease layer.
(3) Metal objects must not be placed over the battery.
(4) Batteries or containers containing acids should carefully be handled.
(5) Monthly or every 200 hours check the acid level and supplement it with DISTILLED WATER required. Level should not
exceed the battery inside mark.
(6) Never use open flames to light battery components: there is explosion danger.
(7) In winter, batteries should be detached and placed following the manufacturer’s instructions.
Before battery is charged with an external charger, disconnect both terminals.
(8)
Fuel decanting filter drainage ( optional ):
Loosen the wing nut (3) (Fig. 7.6) located at the lower side of the
glass vessel and let go all the acrued water. Shut again off the
wing nut and check it does not drip.
Fig. 7.6
Summary of Contents for G-20M-15
Page 1: ...INSTRUCTIONS MANUAL GENSET G 20T 15 G 20M 15 OPTIONAL CANOPY VERSION MARINE GENSETS...
Page 12: ...ENG 8 03917101G ENG rev 0 CANOPY VERSION WITH FAN DELTA CONNECTION...
Page 13: ...ENG 9 03917101G ENG rev 0 STANDARD VERSION 3 PHASES 400V 230V...
Page 14: ...ENG 10 03917101G ENG rev 0 STANDARD VERSION 1 PHASE 230V...
Page 17: ...ENG 13 03917101G ENG rev 0 c GENSET G20T15 G20M15 CONEXIONES Taladros Anclaje Grupo...
Page 39: ......