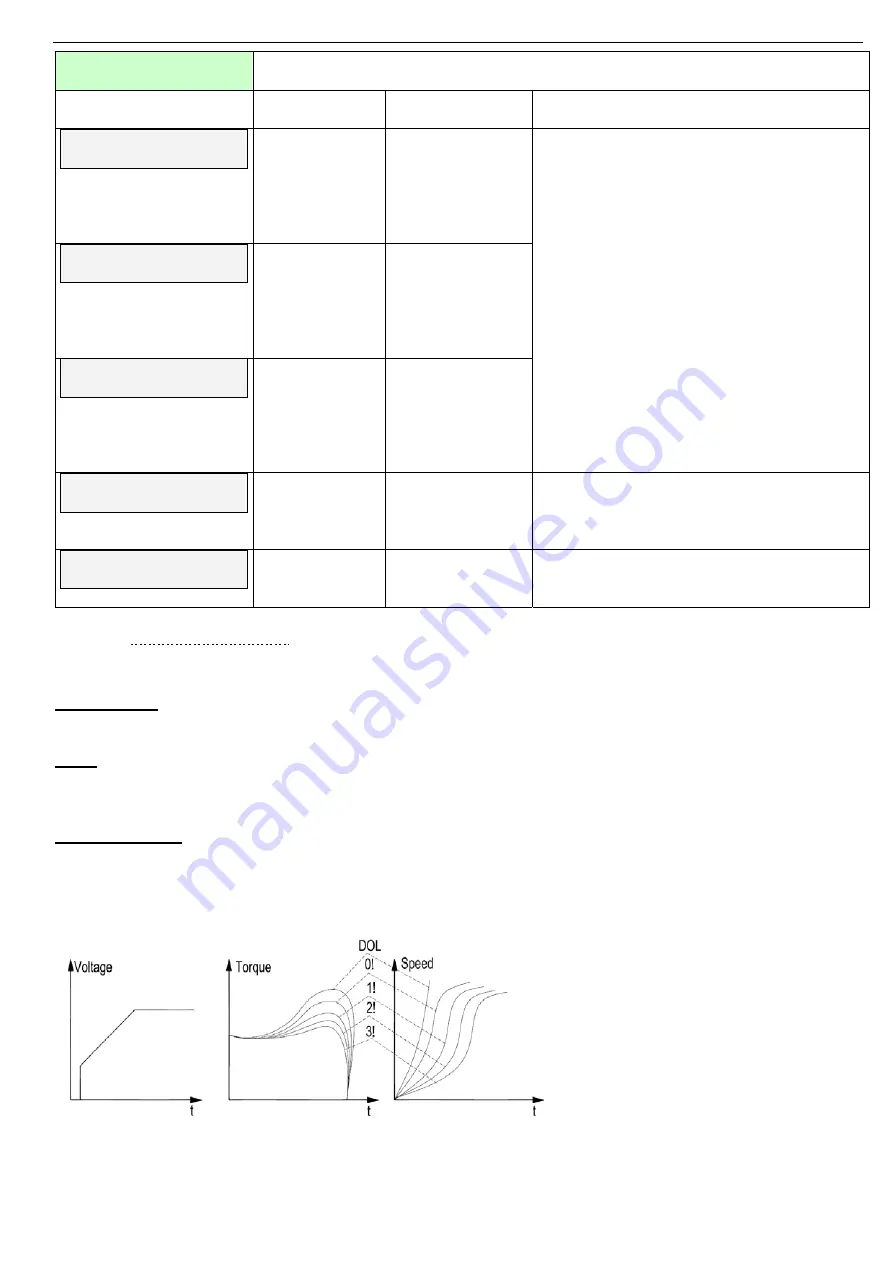
75 • Control Keypad
________________________________________________________________________________________________
START PARAMETERS
- **** -
Displays in MINIMIZED MODE and MAXIMIZED MODE
Display and Default
Values
Range Description
Remarks
NUMBER OF STARTS
10
1-10, OFF
Sets NUMBER
OF STARTS
permitted during
STARTS
PERIOD (see
below).
Limits the NUMBER OF STARTS during
the period of time defined by STARTS
PERIOD.
If you try to start even one more time within
that period the START INHIBIT period will
take effect.
STARTS PERIOD
30 MIN.
1–60min. Sets
STARTS
PERIOD
during which
NUMBER OF
STARTS is being
counted.
During the START INHIBIT period the
WAIT BEFORE RST XX MIN message will
be displayed.
START INHIBIT
15 MIN.
1–60min. Sets
START
INHIBIT time
which starting is
disabled after
TOO MANY
STARTS trip.
RUN CONTACT DEL.
5 sec.
0-120sec.
Sets time delay
for End of
Acceleration
relay to close.
End of Acceleration relay can signal that
motor is at its RUN position which can be
used for motor loading.
STORE ENABLE
START PARAMETERS
Same as STORE ENABLE MAIN
PARAMETERS on page 71.
7.7.3.1
Soft Start Parameters
The RVS-DN incorporates five starting curves to enable you to select a suitable torque curve.
Start Curve 0
– Standard curve (Default). This curve is the most suitable curve for preventing prolonged
starting and motor overheating.
Note:
When RVS-DN is connected Inside Delta, the RVS-DN will always use CURVE 0 regardless of the curve
defined.
Start Curves 1-3 -
Pump Control - Induction motors produce peak torque of up to 3 times the rated torque
towards the end of starting process. In some pump applications, this peak may cause pressure surge in the
pipes.
Start Curves 1, 2, 3 – During acceleration, before reaching peak torque, the Pump Control Program
automatically controls the voltage ramp-up, thus, reducing peak torque.
Choice of four pump control acceleration curves: 0!, 1!, 2!, 3!