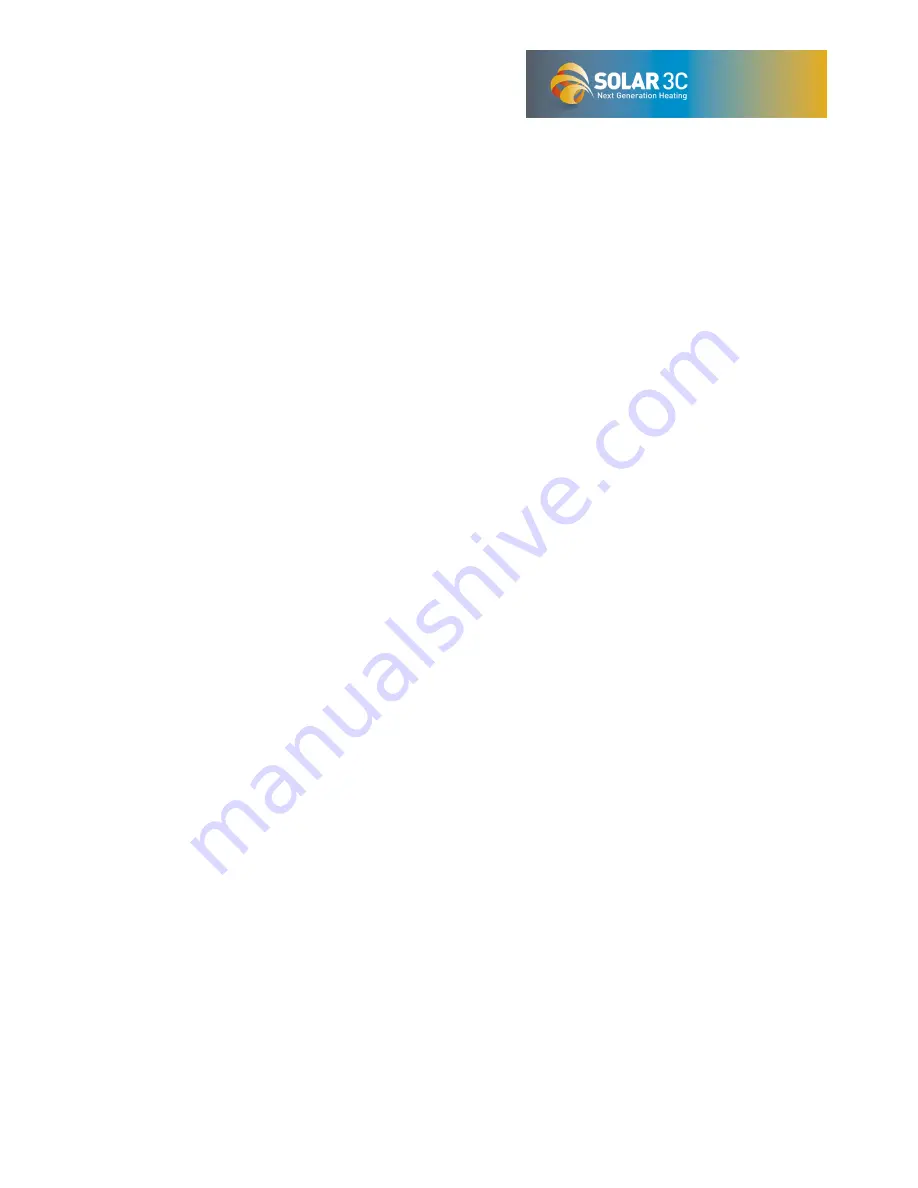
8. Electrical installation
WARNING - THIS EQUIPMENT MUST BE EARTHED.
8.1. All electrical wiring must be carried out by a competent person and in accordance with the current
I.E.E. Wiring Regulations. A suitable Earthing point is provided on the cylinder pedestal directly
below the immersion heater (see Fig 8).
8.2. The control equipment supplied will ensure that the cylinder functions safely. All control equipment
must be supplied via a 3Amp supply and a double pole switch with a minimum 3mm gap. From an
economic and convenience point of view, it is intended that these controls operate in conjunction
with other control packages for example: Solar 3C Solar Heating System or “S” and “Y” plan systems
which incorporate a programmable time clock etc.
8.3. The immersion heaters – 2 x 3kW 230v 50Hz-immersion heaters should be wired in accordance
with the instructions given in Fig 8. The cable MUST be routed through the strain relief bush. We
recommend that the control thermostat is set at 60°C; the high limit trip is factory set at 85°C. The
immersion heater conforms to EEC Directive 76/889 for radio interference and complies with
BS 800:1977.
WARNING: NEVER FIT AN IMMERSION HEATER WITHOUT A THERMAL CUT OUT.
8.4. The indirect temperature controller - The control and high limit thermostat for use with indirect
systems is supplied separately with the unvented hot water safety kit. It should be fitted into
the sensor pocket in the cylinder (see Fig 1 for position). The control thermostat has an adjustment
range between 30°C and 90°C, however it is recommended this it be set to 60°C
WARNING: THE MANUAL RE-SET HIGH LIMIT THERMOSTAT MUST NOT UNDER ANY CIRCUMSTANCES
BE BYPASSED. THIS IS PRE-SET TO 80°C AND TO PREVENT NUISANCE TRIPPING THE CONTROL
THERMOSTAT SHOULD ALWAYS BE AT LEAST 15°C BELOW THIS.
8.5. The 2 port valve - To prevent gravity circulation when the boiler switches off, the 2 port motorised
valve supplied with the unvented hot water kit MUST be fitted in the primary flow pipe to the
cylinder and wired in accordance with Figs 2, 3, 4 (depending on system design), to comply with
current legislation.
Installation and Servicing Manual
Immersion heater installation and wiring instructions
1. Ensure the main’s voltage corresponds to the voltage rating of the immersion heater as shown on the
rating label on the terminal cover.
2. Install the immersion heater into the domestic hot water cylinder using the gasket provided. Use a shaped
spanner-Stillsons or pipe grips should not be used. The use of sealing compound is not recommended.
3. Wire the immersion heater in accordance with Fig 8. It should be wired through a double pole isolator
switch or controller, having contact separation of at least 3 mm, using 1.5mm sq. flexible cable, 85°C
rubber insulated HOFR sheathed, to comply with BS 6141 table 8 and must be fully earthed.
4.
The BEAB approval certification on this immersion heater only applies if rod type thermostats, types Sunvic
VKL or Cotherm SHD are used. The temperature setting of the control thermostat must not exceed 60°C.
5. In the event of the manual reset cut-out operating, isolate the immersion heater from the mains supply,
investigate and identify the cause of the operation of this cut-out, rectify the fault before manually resetting
the cut-out via the reset button on the cut-out. Finally switch the mains electricity supply back on.
17
Summary of Contents for 3C382B
Page 24: ...24 Notes ...
Page 38: ...14 Notes ...