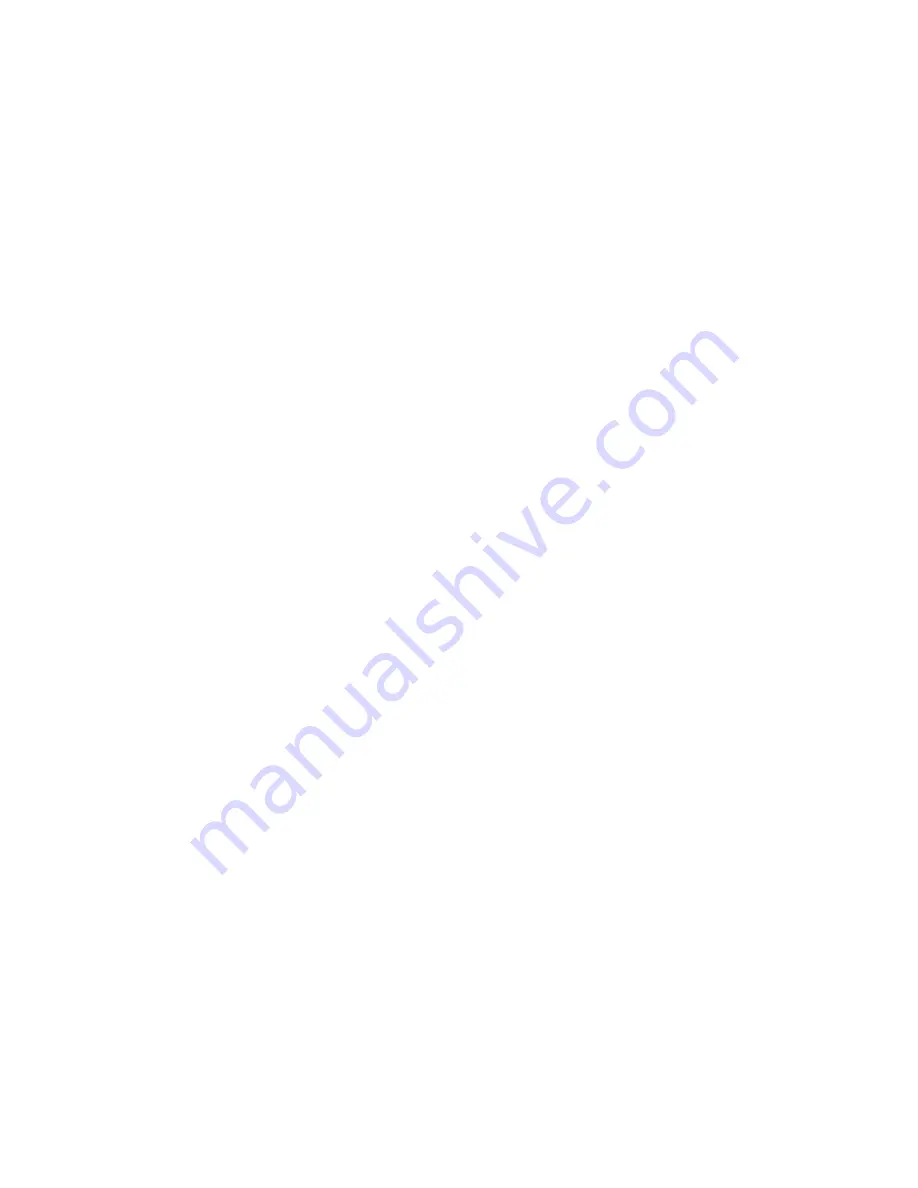
4. Hoist and storage
There are two handles on the top of the arc-welding rectifier for
hoisting purpose.
The arc-welding rectifier and wire feeder are packed with the carton.
It can be transferred manually or with a forklift. However, be sure to
avoid its hit or fall.
The arc-welding rectifier and wire feeder should he stored in a dry,
ventilated, and rainproof place. The storage temperature is -25
~
55'C.
5. Installation and attention
First, please read the user's manual carefully. Check if the
product and accessories are complete and in good condition.
Put the arc-welding rectifier in a dry, dustproof, rainproof, and
anticorrosive place. Make the installation and connection in the
following ways (refer to Diagram 2). Put the arc-welding rectifier in a
well-ventilated environment to facilitate heat dissipation. Air outlet opening
should be not less than 800mm away from the wall, and not less than 100mm
away from the right and left wall.
The three-phase power cable must go to the arc-welding rectifier through the
air switch. Select the capacity of the air switch in accordance with technical
parameter requirements of the welder.
Attention:
The case of the arc-welding rectifier must be securely grounded
(in the place with a grounding mark) to avoid an electric shock.
The arc-welding rectifier must be securely connected to the three-
phase power cable. Otherwise, the equipment would function improperly,
or the local area of the joint be heated and damaged.
It is strictly prohibited to pull the air switch when the load is
applied to avoid the damage.
The "+" output of the arc-welding rectifier should be connected to the wire-
feeder, and the "-" output to the to-be-welded workpiece.
One end of the gas hose is connected to the gas outlet opening of the gas
adjuster, and the other end to the inlet opening of the gas valve of the
wire feeder.