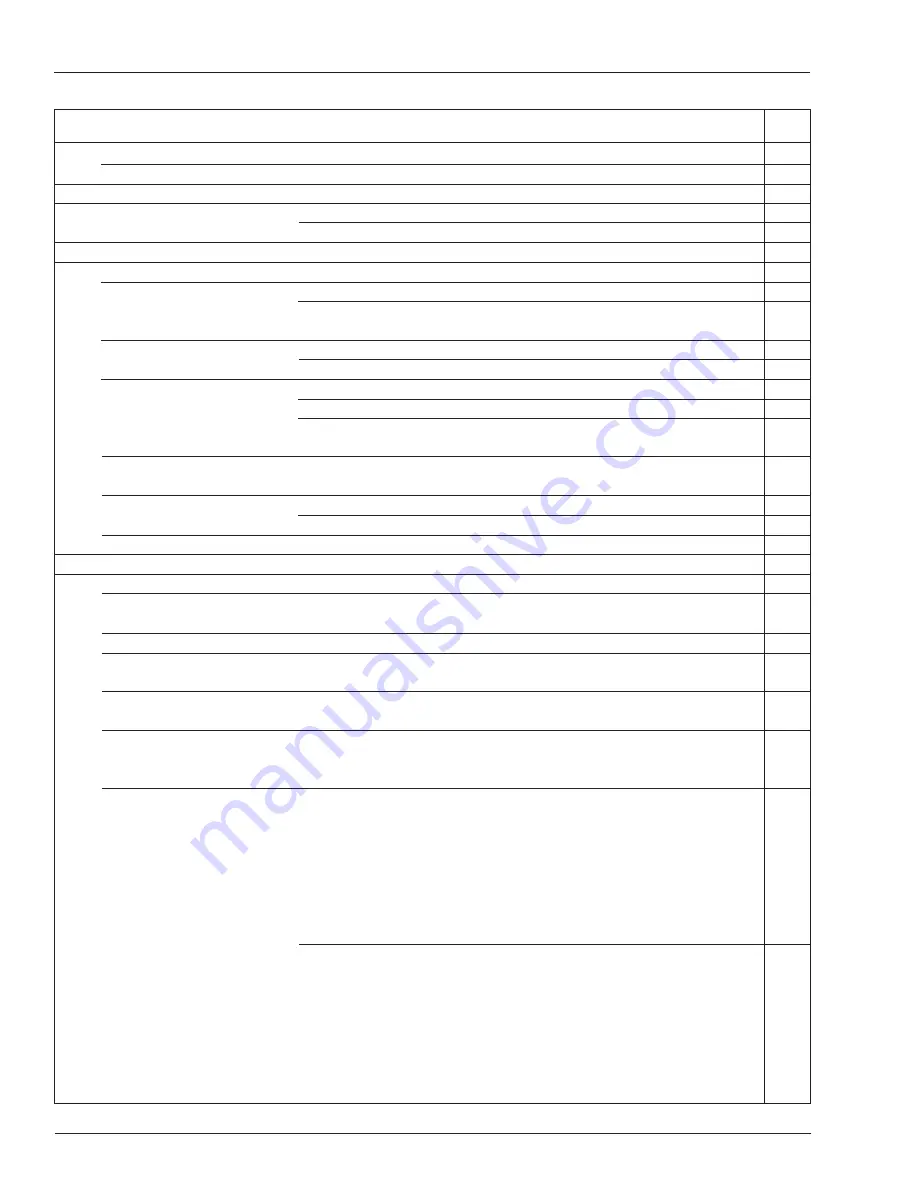
Appendix C – Inspection Checklists
S3215L/S3215E/S3219E/S3220E/S3226E/S4726E/S4732E – 1500834
Frequent Inspection and Maintenance – Every 90 Days or 150 Hours
Swing-out Trays
Hinges and latches
Placards and Decals
Operator’s Manual
Platform
Guardrail
system
Platform floor
Platform
extension
Swing-down rails–if equipped
Entry doors
Lanyard anchors
Emergency Lowering System
Lower Controls
Operating
controls
Emergency
stop
Lowering alarm–if equipped
Lowering interrupt – CE only
Control selector switch
Lift
capacity
Check for damage and proper operation
Check for damage and readability
Order replacements as necessary
Proper manual in document holder
Welds intact, no damage or deformation
All fasteners in place, no loose or
missing parts
Check for damage and deformation
Clean to prevent slip and fall hazards
Check for damage and deformation
Smooth operation
Check for proper operation of
latch handles
Verify that all fasteners are in place
and that the rails fold down properly.
Check for damage and deformation
Check for proper operation
Check for wear and damage
Check for proper operation
Check for smooth operation and
proper speed
Shuts off power to lower controls
Verify that alarm sounds while the plat-
form is lowering
Verify that the platform stops lowering
when it reaches about 1.8 m (6
′
)
Check for proper operation
Check lift function at maximum
load capacity
While the platform is loaded, raise
the platform and with a pen, mark the
chassis next to the slide pad. Mark on
the side of the pad toward the front of
the chassis. Wait for 15 minutes to de-
termine if the lift cylinder is drifting. If the
slide pad covers the mark, the cylinder
or holding valve is leaking.
Refer to Parts Manual
Refer to Operator’s Manual
for function speeds
In the lower controls position,
the upper controls should not
be functional.
Maximum Load
S3215L 670 lb (305kg)
S3215E 600 lb (273 kg)
S3219E 550 lb (250 kg)
S3220E 900 lb (409 kg)
S3226E 500 lb (227 kg)
S4726E 1000 lb (455 kg)
S4732E 700 lb (318 kg)
If the cylinder or holding valve
leaks, remove the machine
from service and correct the
cause of the hydraulic leak
before further operation.
Item
Procedure
Information
P/F/R
Summary of Contents for S3215E
Page 6: ......
Page 24: ...Chapter 3 Safety 16 S3215L S3215E S3219E S3220E S3226E S4726E S4732E 1500834...
Page 30: ...Chapter 4 Safety Devices 22 S3215L S3215E S3219E S3220E S3226E S4726E S4732E 1500834...
Page 34: ...Chapter 6 Batteries 26 S3215L S3215E S3219E S3220E S3226E S4726E S4732E 1500834...
Page 52: ...Chapter 8 Prestart Inspection 44 S3215L S3215E S3219E S3220E S3226E S4726E S4732E 1500834...
Page 70: ...Chapter 11 Emergency Operation 62 S3215L S3215E S3219E S3220E S3226E S4726E S4732E 1500834...
Page 74: ...Appendix A Glossary S3215L S3215E S3219E S3220E S3226E S4726E S4732E 1500834...
Page 78: ...Appendix C Inspection Checklists S3215L S3215E S3219E S3220E S3226E S4726E S4732E 1500834...
Page 84: ...Appendix C Inspection Checklists S3215L S3215E S3219E S3220E S3226E S4726E S4732E 1500834...