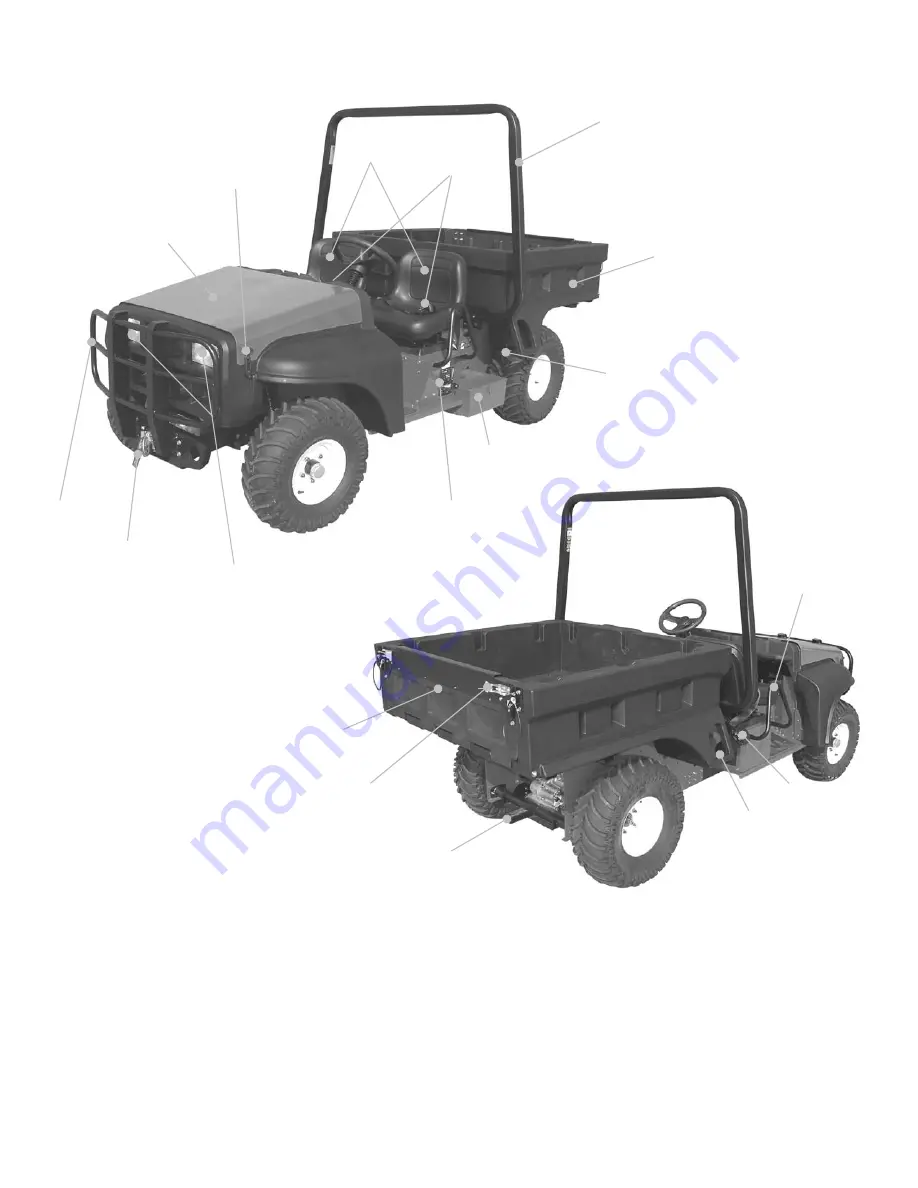
7
SECTION 1 – FAMILIARIZATION
1.1 INTRODUCTION
This manual has been prepared for the operators of
Turf Cruiser™ & Trail Cruiser™ utility vehicles. Its
purpose, aside from recommending standard operating
procedures and routine service requirements, is to
promote SAFETY through the use of accepted
operating practices.
Read, Understand and Follow
the
IMPORTANT SAFETY INSTRUCTIONS on Pages 2
thru 6 of this manual and
All
SAFETY messages on the
utility vehicle and its accessories before operating.
1.2 NOMENCLATURE
The nomenclature information above shows the
essential parts of the vehicle. It is recommended that all
operators of this equipment become thoroughly familiar
with the controls, components, and operation of this
machine before operating. Specific details involving the
engine are found in the separate engine owner’s
manual. Study these manuals before operating and
keep both handy for future reference.
ELECTRIC
WINCH *
BRUSH
GUARD *
CARGO BED
HOOD
RETAINING
LATCH (2)
OPERATOR PROTECTIVE
STRUCTURE (OPS)
SEAT
BELT (2)
STORAGE
COMPARTMENT
8
CARGO BED
LATCH LEVER
POWERLINK™
GENERATOR SYSTEM *
TOOL
BOX
TAILGATE
RECEIVER
HITCH
FUEL FILL
TAILGATE
LATCH (2)
CARGO BED
LIFT HANDLE
(ONE EACH SIDE)
SEAT SIDE
BAR (ONE
EACH SIDE)
HEADLIGHTS
* NOT ON ALL MODELS
SEAT (2)