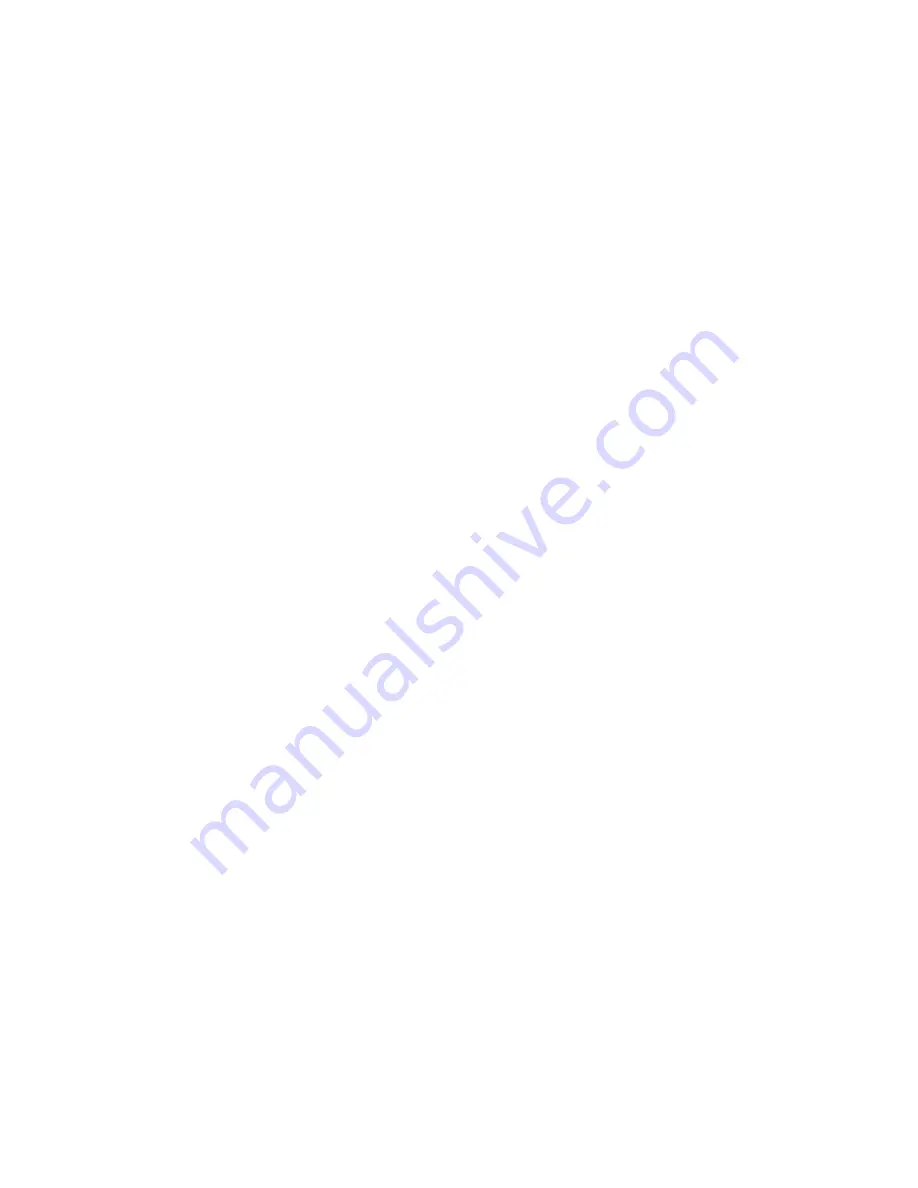
Introduction
Welcome
To the manual for the Smithy MI-1440L lathe. It will teach you about the
parts of the machine and how to take care of your investment. This manual
is complete and current at the time of printing*. In our continuing effort to
bring you the best in machine tools, changes may be made - please visit us
at
www.smithy.com
for the latest updates.
This manual—and any other manuals associated with this Smithy machine—
should remain with the machine. If ownership changes, please include the
Operating Manual with the machine.
Please read the operating manual carefully and closely. Follow the
procedures described. If you don’t understand how your machine works, you
risk injury to yourself or others. Misuse can cause damage to the machine or
to your project. To learn more about general machining practices you can
turn to a number of sources. The Smithy website has a series of Machinist
Training Videos under the Machining Helps section of website heading.
Smithy also offers books that meet the needs of Congratulations on the
purchase of your Smithy Milling Machine. We welcome you to the Smithy
family of quality machine owners. Smithy strives to provide you with the best
in machines and service. Please read through this manual carefully to ensure
that you achieve maximum performance from your MI-1440L lathe.
We also suggest your local library as a resource. Enrolling in a machining
class will give you the best opportunity to learn about machining from
professionals in a supportive environment.
Suggestions or Comments
We are interested in any suggestions you might have to improve our
products and services. Feel free to contact us with your suggestions by
phone or in writing. If you have comments about this operator’s manual, or if
05